Home » Twin Shaft Disperser: Dynamic Shear Mixing
Twin Shaft Disperser: Dynamic Shear Mixing
Twin Shaft Disperser
A twin shaft disperser is a type of industrial machine used for dispersing or mixing various materials on a large scale. It consists of two parallel counter-rotating shafts fitted with mixing elements like paddles or discs. As the shafts rotate in opposite directions, they work together to efficiently break up, distribute, and blend solid or semi-solid materials with liquids, gases, or each other.
Details of Twin Shaft Disperser
- Hydraulic lifting, 360-degree rotation, step-less speed regulation, and other functions.
- Good uniformity, high production efficiency, and large capacity.
- Stir evenly without dead ends, easy to clean.
Application: Paint, Adhesive, Battery, Pharmaceutical industry, Cosmetic
Twin shaft dispersers offer several advantages over other mixing technologies. Their intermeshing counter-rotating design provides powerful shearing forces that can thoroughly disperse even very viscous or non-flowable substances. They also minimize dead zones where materials can get trapped, ensuring uniform mixing throughout the mixing chamber. Their large throughput capacities make them well-suited for high-volume industrial applications.
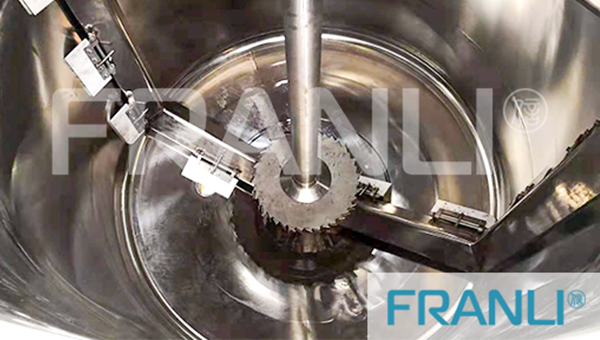
How Twin Shaft Dispersers Work
Twin shaft dispersers work on the principle of dynamic shear mixing. The two parallel shafts are fitted with mixing elements and rotate at different speeds, usually in opposite directions. As the shafts turn, the elements on one shaft pass between the elements on the other shaft. This intermeshing motion subjects the materials being mixed to intense shearing forces.
The shearing action breaks up solid lumps or agglomerates into smaller particles. It also distributes these particles evenly throughout the mixing chamber along with any liquids or gases present. The counter-rotating motion further enhances mixing by continually folding and refolding the materials. This repeated shearing, folding, and redistribution allows twin shaft dispersers to thoroughly blend even very difficult-to-mix formulations.
Mixing Elements
The type of mixing elements used on the shafts depends on the specific application. Common element styles include:
– Paddles: Flat or curved plates that scrape and fold materials for dispersing and blending. Ideal for low to medium-viscosity mixtures.
– Discs: Circular plates fitted along the shafts. Provide shearing action and folding of materials. Suitable for a wide range of viscosities.
– Pins/Knives: Projecting pins or blades that cut, fold, and redistribute materials. Effective for high viscosity or non-flowable mixtures.
– Wires: Strands of wire wound helically along the shafts. Provide cutting and folding action through their twisting motion. Used for shear-sensitive products.
Elements can have either a radial or axial configuration depending on the flow pattern required. Their design, arrangement, and clearances between shafts are optimized based on the properties of the materials being mixed.
Process Parameters
Several process parameters influence the performance of twin shaft dispersers:
– Shaft Speed: Varies depending on viscosity, typically 50-1000 rpm. Higher speeds provide greater shear forces but can cause over-mixing.
– Shaft Configuration: Co-rotating vs counter-rotating shafts, radial vs axial elements, number of mixing zones. Alters flow patterns.
– Residence Time: Time materials are spent in the mixing chamber, typically 1-60 minutes. Longer times ensure complete mixing but risk degradation.
– Temperature Control: Jacketed vessels allow heating/cooling to control viscosity for optimal mixing.
– Impeller Clearance: The gap between shafts affects shear rate and mixing efficiency. Too close can cause damage, and too far reduces forces.
– Feed Method: Batch, continuous, or gated feed systems. Influences mixing homogeneity and throughput.
Careful control and optimization of these parameters are crucial for achieving the desired mixing results for a given formulation.
Applications
Given their powerful shearing action and large throughput capacities, twin shaft dispersers find wide application across many process industries:
– Pharmaceuticals: Dispersing or granulating active ingredients, producing ointments, creams, and suspensions.
– Food Processing: Mixing dough, batters, sauces, and other viscous food mixtures on an industrial scale.
– Paints & Coatings: Preparing pigment pastes, and dispersing additives into base formulations.
– Plastics & Rubber: Compounding polymers with fillers, plasticizers and other additives.
– Mining & Minerals: Pre-treatment of ores through milling, leaching and flotation processes.
– Chemicals: Emulsifying, dispersing, or reacting a variety of liquid, solid, and slurry mixtures.
– Cosmetics: Formulating creams, lotions, gels, and other personal care products.
With their versatility, sanitary designs, and large capacities, twin shaft dispersers are indispensable production equipment for many continuous and batch manufacturing industries. Their dynamic mixing action through shearing forces makes them highly effective for a wide range of dispersing and blending applications.
Twin shaft dispersers are an important type of industrial mixing equipment that utilize counter-rotating shafts and intermeshing elements to provide powerful shear forces for dispersing, granulating, and homogenously blending various materials. Their advantages of thorough mixing, minimized dead zones and high throughput capacities make them well-suited to large-scale process applications across multiple industries. Careful control and optimization of operating parameters allow twin shaft dispersers to mix various formulations effectively.
Welcome to send inquiry to us and let’s make a win win business together !
Guidelines For Filling Machine
FRANLI is manufactured as a professional filling machine equipment, our filling machine can be filled from a minimum of 100g to a maximum of 250kg, and the filling dose can be adjusted by itself.
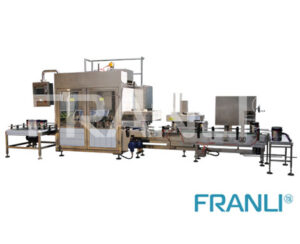
Paint Filling Machines: Enhancing Efficiency and Precision
Paint filling machines are vital equipment in the paint and coatings industry, designed to accurately fill various types of paint into containers of different sizes and shapes.
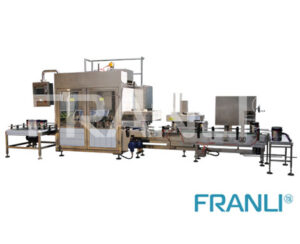
Paint Filling Machine | Liquid Filling Machine
Paint filling machines are automated industrial equipment used for filling paint, coatings, adhesives, and other liquid products into containers.
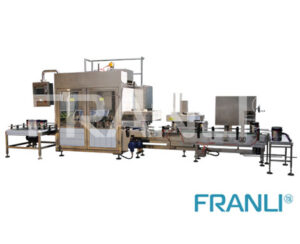
Paint Filling Machine: Efficient and Accurate Filling of Paint
A paint filling machine is a specialized piece of equipment used to fill paint cans with liquid paint. It consists of a conveyor system, a filling station, and a control panel.
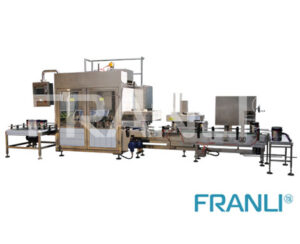
Paint Filling Machine:Accurate Filling of Viscous Liquids
Paint filling machines are specialized equipment used in the paint and coatings industry to accurately measure and fill paint into various containers.
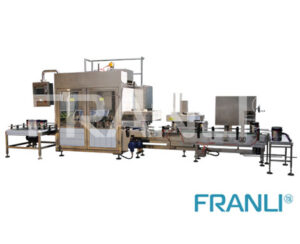
Filling Machines in Lubricating Oil Filling: Streamlining Efficiency & Precision
Filling machines have revolutionized this process by automating the entire operation. These machines are designed to precisely control the amount of oil-filled, ensuring accuracy and reducing wastage.
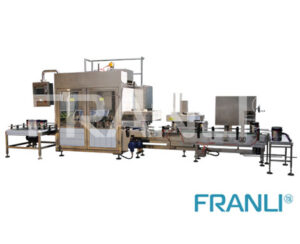
Glue Filling Machine: High Precision & High Efficiency
Filling machines used in the glue field are designed to deliver precise amounts of adhesive into containers, including bottles, cans, tubes, and cartridges.