Home » Triple Shaft Mixer: Ideal Equipment for Ink Production
Triple Shaft Mixer: Ideal Equipment for Ink Production
Triple Shaft Mixer
Triple shaft mixers are capable of handling a wide range of ink formulations, including solvent-based, water-based, UV-curable, and hybrid inks. Their adaptability lies in the ability to create ideal processing conditions for various viscosities, allowing manufacturers to produce inks for different applications, such as flexography, gravure, screen printing, and digital printing.
Advantages of Triple Shaft mixer
- Long life with a sturdy mixing bowl made by a fully automatic welding robot
Can manufacture all kinds of concrete - High uniformity even with a short mixing time
Parts with excellent durability and wear resistance - Easy maintenance with replaceable bolt lining for large maintenance doors
Automatic lubrication system - Compact design and universal compatibility with existing concrete plants
Application: Paint, Adhesive, Battery, Pharmaceutical industry, Cosmetic
The field of ink production has witnessed tremendous advancements in recent years, with manufacturers constantly striving for improved quality, consistency, and efficiency in their products. Central to this pursuit is the utilization of state-of-the-art mixing technologies. Among these, triple shaft mixers have emerged as indispensable tools, revolutionizing the ink industry.
Understanding Triple Shaft Mixers
Triple shaft mixers are innovative mixing machines specifically engineered to handle complex ink formulations. They boast three independently driven mixing shafts – two high-speed dispersers and a slow-speed anchor agitator. This unique design allows for efficient blending, high shear dispersion, and effective temperature control, ensuring impeccable ink quality.
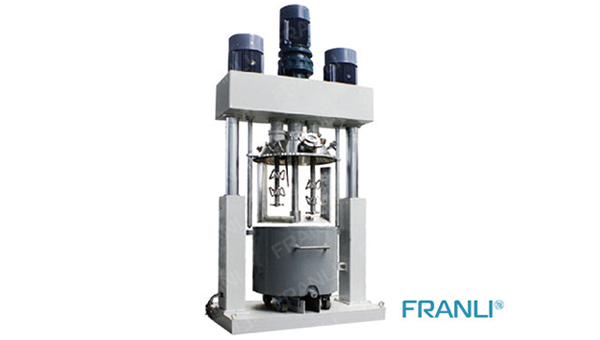
Advantages of Triple Shaft Mixers in Ink Production
1. Enhanced Mixing Efficiency:
Triple shaft mixers excel in distributing and homogenizing ink components, ensuring consistent color and viscosity throughout. The combination of high-speed dispersers and anchor agitators efficiently breaks down agglomerates, dissolves additives, and incorporates pigments into the ink base. The result is a perfectly blended ink ready for optimal performance in printing applications.
2. Improved Dispersion Quality:
Ink formulations often require even distribution of specialty pigments, such as metallics, fluorescents, and pearlescents. The high shear forces generated by the high-speed dispersers in triple shaft mixers enable thorough dispersion of such challenging pigments, resulting in vibrant, visually captivating inks.
3. Temperature Control:
Maintaining optimal temperature during ink production is critical, as changes in temperature can affect ink viscosity, pigment stability, and overall quality. Triple shaft mixers are equipped with jacketed mixing vessels and optional temperature control systems, enabling manufacturers to precisely regulate and monitor temperature during the mixing process. This ensures that ink batches are produced consistently, regardless of ambient conditions.
4. Facilitated Cleaning and Maintenance:
Triple shaft mixers are designed with accessibility and ease of maintenance in mind. Removable mixing shafts, easy-to-clean mixing vessels, and streamlined machine interfaces simplify the cleaning process, minimizing downtime between different ink formulations. The ability to quickly switch between color batches or different ink compositions reduces production lead time, enhancing productivity and overall efficiency.
Versatility of triple shaft mixers
1. Metallic Effect Inks:
Triple shaft mixers have proven instrumental in producing metallic effect inks, which usually contain reflective pigments. The high shear forces facilitate the dispersion of the pigments, ensuring uniform particle distribution and maximizing the visual impact of the ink in printed materials.
2. UV-Curable Inks:
Triple shaft mixers are particularly valuable in the production of UV-curable inks. These inks often require accurate dispersion of photosensitive components and resins. The triple shaft design effectively breaks down aggregates and reduces particle size, enabling a more efficient and uniform curing process.
Triple shaft mixers have revolutionized ink production with their versatility, precision, and efficiency. Their capability to handle a wide range of ink formulations and create ideal processing conditions makes them an essential tool for ink manufacturers seeking to produce high-quality, consistent, and visually appealing inks. As the ink industry continues to evolve and innovate, triple shaft mixers will undoubtedly remain at the forefront, enabling manufacturers to unleash their creative potential in ink production.
Welcome to send inquiry to us and let’s make a win win business together !
Guidelines For Multi Shaft Mixer
FRANLI customized different kinds of multi-shaft mixers for more than 300+ customers. This kind of machine works in the coating industry, medicine industry, cosmetic industry, and other high technology chemical industries.
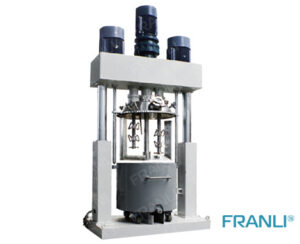
The Application of Triple Shaft Mixers in Adhesives
Triple-shaft mixers, also known as multi-shaft mixers, are innovative blending machines designed to efficiently mix and disperse various components in adhesives.
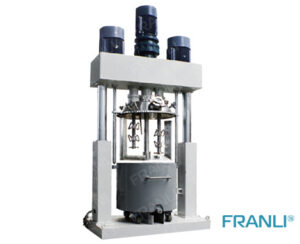
Triple Shaft Mixer: Ideal Equipment for Ink Production
Triple shaft mixers are capable of handling a wide range of ink formulations, including solvent-based, water-based, UV-curable, and hybrid inks.
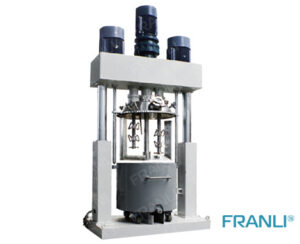
The Versatility and Application of Triple Shaft Mixers in Coatings
Triple shaft mixers have revolutionized the coating industry by providing efficient and versatile solutions for mixing raw materials.
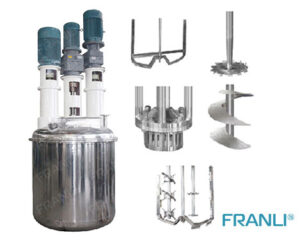
What is a Multi-Shaft Mixer?
A multi-shaft mixer is a type of industrial mixer that has more than one mixing shaft. These mixers are designed to mix multiple ingredients simultaneously, allowing for more efficient and effective mixing.
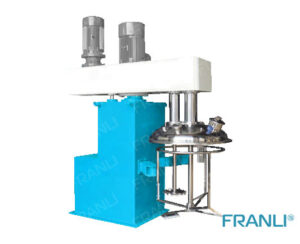
Dual Shaft Mixer – Dispersion & Stirring
The dual shaft mixer is the best mixer to dissolve the specific ingredients with appropriate shear capacity. This activity is performed by the high-speed shafts situated in the mixer and provides you with the perfect uniformity of the product. It also contains an Anchor agitator and a High-Speed Disperser that offer you the best quality and consistency.
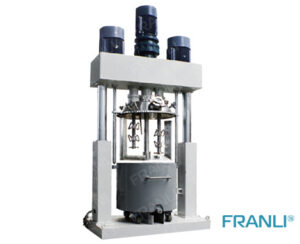
Triple Shaft Mixer | anchor type, butterfly type & frame type
The FRANLI triple shaft mixer extends the working area by adding a rotating stator mixer with a large displacement or a second quick distributor. High shear stator and rotary mixer can emulsify and homogenize products that require higher shear forces to reduce particles into smaller sizes.