Home » The Application of Triple Shaft Mixers in Adhesives
The Application of Triple Shaft Mixers in Adhesives
Triple Shaft Mixer
Triple-shaft mixers, also known as multi-shaft mixers, are innovative blending machines designed to efficiently mix and disperse various components in adhesives. The primary components of triple shaft mixers include a high-speed disperser blade, a sweep blade, and an anchor agitator. Each component performs a specific function in the mixing process, leading to exceptional results.
Advantages of Triple Shaft mixer
- Long life with a sturdy mixing bowl made by a fully automatic welding robot
Can manufacture all kinds of concrete - High uniformity even with a short mixing time
Parts with excellent durability and wear resistance - Easy maintenance with replaceable bolt lining for large maintenance doors
Automatic lubrication system - Compact design and universal compatibility with existing concrete plants
Application: Paint, Adhesive, Battery, Pharmaceutical industry, Cosmetic
In today’s industrial landscape, the demand for high-quality adhesives is paramount, spanning a multitude of sectors such as automotive, construction, packaging, and manufacturing. As adhesives play a crucial role in bonding materials, ensuring their uniformity, consistency, and performance is vital. With advancements in technology, the application of triple-shaft mixers in the adhesive manufacturing process has emerged as a game-changer, revolutionizing efficiency and quality.
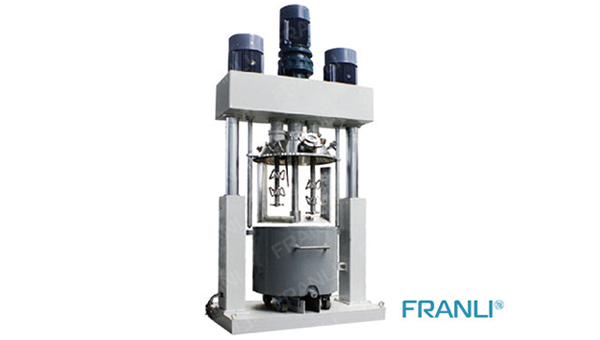
Applications in Adhesive Manufacturing
1. Homogenization and Dispersion:
Triple shaft mixers excel in homogenizing and dispersing different components of adhesives, such as resins, fillers, solvents, and additives. The high-speed disperser blade rapidly breaks down agglomerates, ensuring uniform distribution and eliminating any residual lumps. This process enhances the adhesive’s stability, durability, and overall quality.
2. Temperature Control:
Adhesive formulations often require precise temperature control during the mixing process. Triple shaft mixers are equipped with advanced jacketed vessels that allow for effective heat transfer. This feature helps in maintaining the adhesive’s desired temperature, thus improving the consistency of the final product.
3. Shear Stress and Viscosity Reduction:
Many adhesives require a specific viscosity range for optimal application. Triple shaft mixers are designed to create sufficient shear stress that reduces the viscosity and enables easy flow of the adhesive. This capability ensures improved spreadability and adhesion, catering to a wide range of industrial applications.
Advantages of Triple Shaft Mixers in Adhesive Manufacturing
1. Increased Efficiency:
Triple shaft mixers significantly reduce batch processing times due to their superior mixing capabilities. The combination of high-speed dispersion, sweep mixing, and anchor agitation optimizes the homogenization process, eliminating the need for extended mixing durations. This results in increased productivity, reduced labor costs, and improved overall efficiency in adhesive production.
2. Enhanced Product Quality:
Through their precise and effective mixing capabilities, triple-shaft mixers contribute to the creation of high-quality adhesives. The elimination of agglomerates and the uniform distribution of additives and fillers ensure consistent performance and product reliability. Homogeneity and dispersion play a crucial role in the final adhesive bond strength, ensuring customer satisfaction and industry compliance.
3. Versatility:
Triple shaft mixers are versatile machines that can handle various types of adhesives, including solvent-based, water-based, and reactive adhesives. Their adaptability allows adhesive manufacturers to cater to a wide range of customer demands. Additionally, the mixers can accommodate different batch sizes, making them suitable for both small-scale and large-scale production.
4. Simplicity and Ease of Use:
Despite their advanced capabilities, triple shaft mixers are designed with user-friendliness in mind. Operators can control the mixing process through modern control panels, adjusting settings such as speed, temperature, and duration with ease. The intuitive design ensures streamlined operation, minimizing human error and maximizing productivity.
In the evolving landscape of adhesive manufacturing, triple shaft mixers have become a vital asset. With their ability to homogenize, disperse, control temperature, and reduce viscosity, these machines have revolutionized the industry, improving efficiency, consistency, and overall product quality. The versatility and ease of use further contribute to their widespread adoption. As the demand for high-performing adhesives continues to grow, the application of triple shaft mixers will undoubtedly play a crucial role in meeting those demands while driving the adhesive industry forward.
Welcome to send inquiry to us and let’s make a win win business together !
Guidelines For Multi Shaft Mixer
FRANLI customized different kinds of multi-shaft mixers for more than 300+ customers. This kind of machine works in the coating industry, medicine industry, cosmetic industry, and other high technology chemical industries.
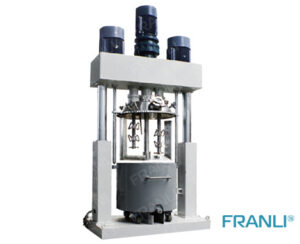
The Application of Triple Shaft Mixers in Adhesives
Triple-shaft mixers, also known as multi-shaft mixers, are innovative blending machines designed to efficiently mix and disperse various components in adhesives.
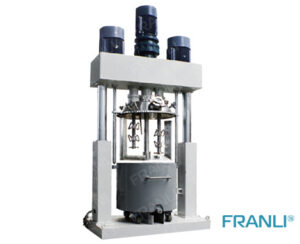
Triple Shaft Mixer: Ideal Equipment for Ink Production
Triple shaft mixers are capable of handling a wide range of ink formulations, including solvent-based, water-based, UV-curable, and hybrid inks.
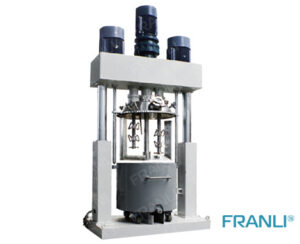
The Versatility and Application of Triple Shaft Mixers in Coatings
Triple shaft mixers have revolutionized the coating industry by providing efficient and versatile solutions for mixing raw materials.
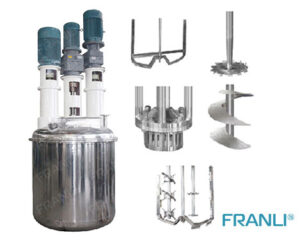
What is a Multi-Shaft Mixer?
A multi-shaft mixer is a type of industrial mixer that has more than one mixing shaft. These mixers are designed to mix multiple ingredients simultaneously, allowing for more efficient and effective mixing.
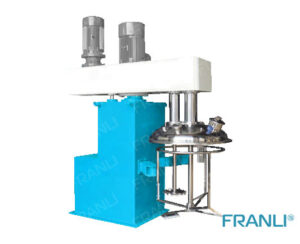
Dual Shaft Mixer – Dispersion & Stirring
The dual shaft mixer is the best mixer to dissolve the specific ingredients with appropriate shear capacity. This activity is performed by the high-speed shafts situated in the mixer and provides you with the perfect uniformity of the product. It also contains an Anchor agitator and a High-Speed Disperser that offer you the best quality and consistency.
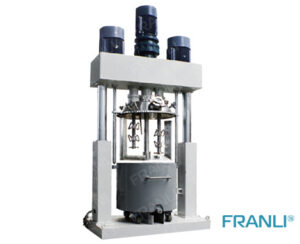
Triple Shaft Mixer | anchor type, butterfly type & frame type
The FRANLI triple shaft mixer extends the working area by adding a rotating stator mixer with a large displacement or a second quick distributor. High shear stator and rotary mixer can emulsify and homogenize products that require higher shear forces to reduce particles into smaller sizes.