Home » The Versatile Application of Ribbon Blenders in Pesticide Manufacturing
The Versatile Application of Ribbon Blenders in Pesticide Manufacturing
Ribbon Blender
Ribbon blenders, sometimes referred to as ribbon mixers, are industrial blending machines widely used in the pesticide manufacturing industry. These machines are specifically designed to mix dry or powdered materials, ensuring the homogeneity of the final product.
Advantages of Ribbon Mixer
- fast and efficient
- safe and stable
Application: chemical, pesticide, dye, medicine, feed, fertilizer, metallurgy, mining, food, plastic, additives, and other industries.
In the realm of pesticide manufacturing, the efficacy and safety of the final product heavily rely on the careful and precise blending of various materials. Ribbon blenders have emerged as powerful tools in this industry, enabling manufacturers to achieve homogeneity, maximize productivity, and ensure the consistent quality of pesticide formulations.
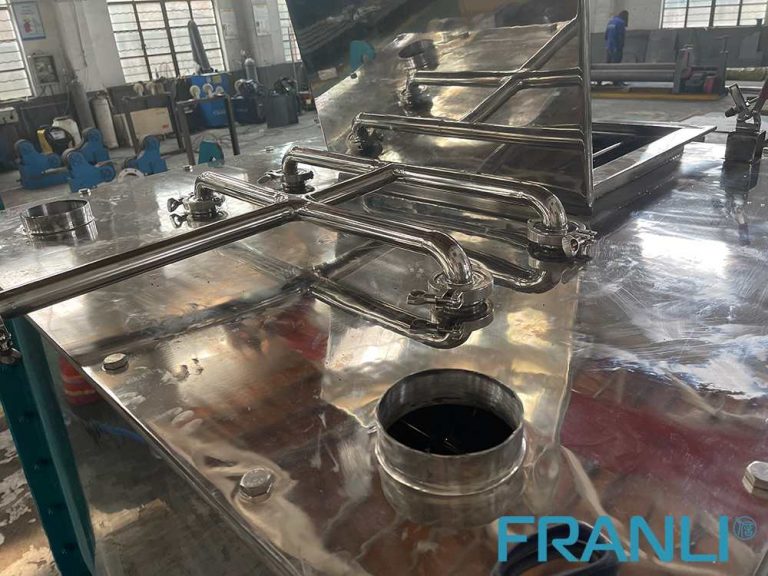
Design Characteristics
1. Construction: Ribbon blenders consist of a U-shaped trough with a revolving double helical ribbon agitator. The agitator, comprising inner and outer helical ribbons, rotates at moderate speed to guarantee efficient mixing.
2. Capacity: Ribbon blenders are available in various capacities, ranging from small-scale models suitable for laboratories to large-scale machines tailored for industrial production.
3. Materials: Ribbon blenders are predominantly constructed with stainless steel or carbon steel due to their exceptional durability and ability to withstand the corrosive nature of the materials being processed.
4. Safety Features: These blenders often include safety features such as dust-tight covers, safety grates, interlocking mechanisms, and emergency stop buttons to ensure operator safety during operation.
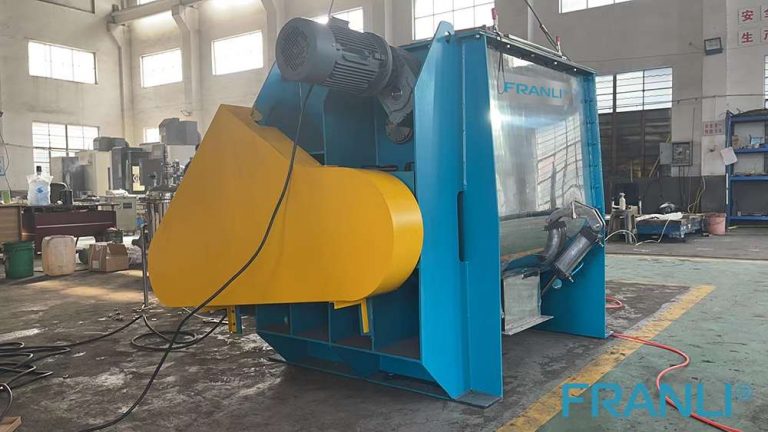
Operation Principles of Ribbon Blenders
A. Loading and Unloading
1. Loading: The raw materials needed for the pesticide formulation are measured and added into the ribbon blender’s trough through an inlet. The order of material introduction is crucial for achieving desired blend uniformity.
2. Blending Process: Once the raw materials are introduced, the ribbon agitator consistently conducts a gentle folding, cutting, and shearing motion, homogenously blending the materials together.
3. Discharge: Upon completion of the blending process, the blended pesticide formulation is discharged through an outlet situated at the bottom of the trough.
B. Blending Efficiency
1. Mixing Mechanism: Ribbon blenders employ the convective mixing principle, where the outer ribbon lifts the materials upwards, while the inner ribbon pushes the materials downward. This action creates a cross-mixing effect, resulting in thoroughly blended materials.
2. Time and Speed: The blending time and speed can be adjusted to accommodate different materials, ensuring optimal processing efficiency without compromising the integrity of the materials.
3. Batch Size and Homogeneity: Ribbon blenders are versatile and capable of handling different batch sizes. Thanks to their efficient mixing mechanisms, they deliver consistent homogeneity within each batch, minimizing variability in the final product.
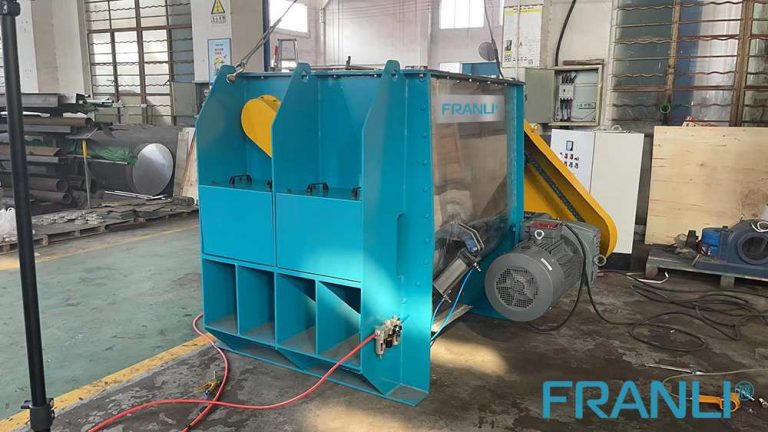
Advantages of Ribbon Blenders in Pesticide Manufacturing
A. Homogeneous Blending: Ribbon blenders excel at homogeneity, eliminating the risk of uneven distribution of active ingredients or additives. This ensures that pesticides are equally effective throughout the entire application process.
B. Efficient Production: By rapidly blending large batches of materials, ribbon blenders enhance productivity in pesticide manufacturing. They reduce processing time and allow for continuous production, resulting in increased output and lower operational costs.
C. Flexibility: Ribbon blenders can process a wide range of raw materials, including powders, granules, and even viscous substances. This versatility allows pesticide manufacturers to adapt to changing formulations and produce different product types efficiently.
D. Minimized Material Losses: The design of ribbon blenders helps minimize material losses during the blending process. The efficient scraping action of the ribbons ensures that all materials are discharged, leaving minimal waste behind.
Considerations for Efficient Ribbon Blender Applications in Pesticide Manufacturing
A. Material Particle Size: The particle size of the raw materials has a significant impact on blending efficiency. Manufacturers must ensure that the particle sizes of the ingredients are within the specified range to achieve optimal homogeneity.
B. Dust Control: Pesticide manufacturing processes often generate fine particles that can be hazardous to operators if inhaled. Implementing appropriate dust control measures such as installing dust-tight covers and connecting ribbon blenders to dust collection systems is crucial for ensuring operator safety.
C. GMP Compliance: In pesticide manufacturing, adherence to Good Manufacturing Practices (GMP) is essential. Ribbon blenders, as integral components of the production process, must be designed, operated, and maintained according to GMP guidelines to ensure the quality and safety of the final pesticide formulation.
D. Dosing Accuracy: Ribbon blenders are typically not equipped with dosing systems. Therefore, accurate measurement of raw materials before loading them into the blender is crucial to ensure the production of effective and consistent pesticide formulations.
Ribbon blenders have revolutionized the pesticide manufacturing industry by providing an efficient, cost-effective, and reliable solution for blending various materials. With their homogeneity, productivity, flexibility, and other advantages, these blending machines have become essential tools in the production of safe and effective pesticide formulations. Adhering to proper design considerations and operational practices can maximize the benefits of ribbon blenders, ensuring consistent quality, and advancing the pesticide manufacturing industry.
Welcome to send inquiry to us and let’s make a win win business together !
Guidelines For Ribbon blender
Ribbon blenders are essential equipment in various industries where the quality and consistency of the final product are critical factors. They are highly efficient, customizable, and reliable mixing solutions that offer unsurpassed performance and versatility. By integrating a ribbon blender into your production line, you can ensure consistent and reliable product quality, increased productivity, and reduced manufacturing costs.
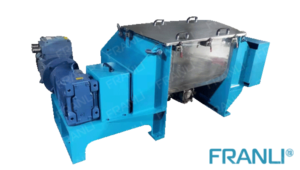
Ribbon Blender Mixer Equipment
A ribbon blender mixer, also known as a ribbon mixer or horizontal ribbon blender, is a powerful industrial machine designed for thorough and efficient blending of various materials.
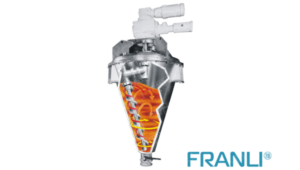
Ribbon Blender Mixer: The Right Choice for a High-Quality Blender
Ribbon blender mixers, also known as ribbon mixers or ribbon blenders, are horizontal mixing devices characterized by their unique ribbon-shaped agitators.
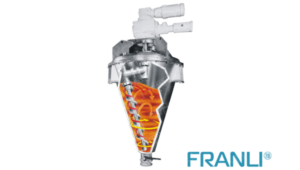
Vertical Ribbon Blender: Efficient mixing equipment for solids and powders
A vertical ribbon blender, also known as a vertical mixer, is a type of mixing machine widely used in various industries for the homogeneous blending of dry, free-flowing solids.
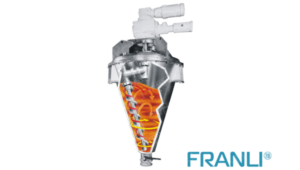
Powder Ribbon Mixer: Whirling Agitator and Horizontal U-shaped Housing
A powder ribbon mixer, also known as a ribbon blender, is a versatile and widely used machine for combining different powders, powder with liquid, powder with granules, and dry solids.
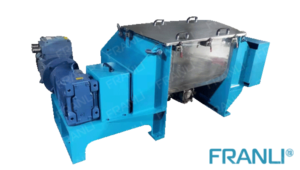
Small Ribbon Blender: A Versatile and Efficient Processing Equipment
The small ribbon blender is a versatile and efficient processing equipment used in the food, pharmaceutical, and cosmetic industries for blending, mixing, and uniformizing various types of materials.
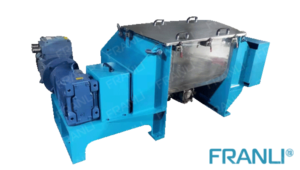
What is A Small Ribbon Blender?
The small ribbon blender is a versatile and efficient machine used for the mixing of various materials such as powders, pastes, and dried granules.