Home » The Application of Pneumatic Mixers in Various Industries
The Application of Pneumatic Mixers in Various Industries
Pneumatic Mixers
Pneumatic mixers are widely utilized in various industries as a crucial component of the mixing process. These versatile machines utilize compressed air to rotate blades or paddles, enabling efficient and uniform blending of various substances or materials.
Details of Pneumatic Mixers
- The pneumatic mixer can be adjusted steplessly.
- The pneumatic mixer can rotate forward and reverse.
- The working environment of the pneumatic mixer is not affected by vibration, high temperature, electromagnetic, radiation, etc.
- The air motor matched with the air mixer has the function of overload protection, and will not fail due to overload.
- The pneumatic mixer has a high starting torque and can be started directly with a load.
- The pneumatic mixer is easy to operate and easy to maintain and repair.
Application: petroleum, chemical, paint, paint, woodworking, food, daily chemical, and other flammable, dusty, heavy-duty, wet, and other industries.
Pneumatic Mixers in the Pharmaceutical Industry
In the pharmaceutical industry, pneumatic mixers play an integral role in the manufacturing process. They are primarily used for liquid-liquid and solid-liquid mixing applications, ensuring homogeneity in drug formulations. Pneumatic mixers provide several advantages, such as high mixing efficiency, low energy consumption, and ease of cleanability, making them an ideal choice for pharmaceutical manufacturers. One key challenge in this industry is the requirement for strict adherence to Good Manufacturing Practices (GMP) and the need for sterile conditions.
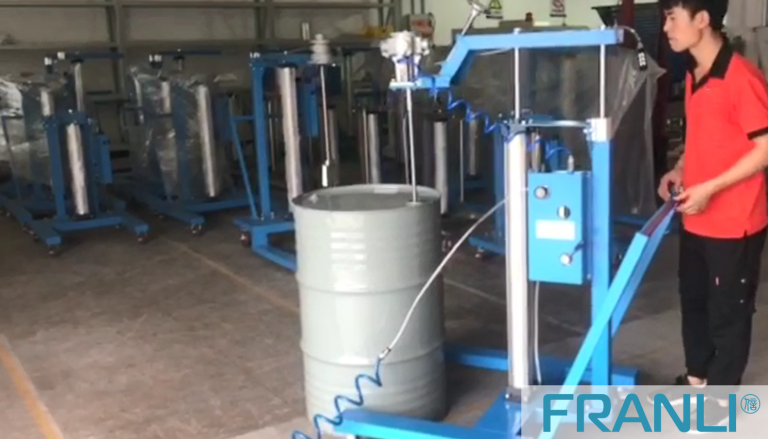
Pneumatic Mixers in the Food Industry
The food industry relies heavily on pneumatic mixers for the preparation of various food products. The uniform blending of ingredients, such as liquids, powders, and emulsions, is crucial to achieve desired taste, texture, and shelf life. Pneumatic mixers are used in processes such as mixing dough, sauces, dressings, and confectionery. Additionally, pneumatic mixers with food-grade stainless steel construction offer hygienic benefits, easy maintenance, and compliance with food safety regulations. However, challenges may arise in achieving the required consistency and minimizing product degradation during mixing.
Pneumatic Mixers in the Chemical Industry
The chemical industry utilizes pneumatic mixers extensively for blending and agitation purposes. Pneumatic mixers are employed in the production of paints, coatings, adhesives, and polymers. These mixers offer high-speed operation, ensuring efficient dispersion and dissolution of chemical compounds. Furthermore, their adjustable blade design makes them suitable for various viscosity levels and different batch sizes. Chemical manufacturers face challenges related to handling corrosive or hazardous substances and ensuring the containment of volatile organic compounds (VOCs) during the mixing process.
Pneumatic Mixers in Wastewater Treatment Plants
Pneumatic mixers play a vital role in wastewater treatment plants by facilitating various mixing processes, including aeration, biological treatment, and solids suspension. These mixers help maintain appropriate oxygen levels in aerobic treatment systems, promoting the growth of microorganisms that degrade organic pollutants. Pneumatic mixers are also employed for blending chemical reagents in flocculation tanks, aiding in the removal of suspended solids and improving sedimentation efficiency. The main challenge in wastewater treatment is ensuring the durability and reliability of pneumatic mixers in harsh operating conditions while minimizing energy consumption.
Future Prospects and Conclusion
As technology continues to advance, pneumatic mixers are likely to undergo further improvements and innovations. Future developments may include enhanced control systems, optimized energy efficiency, and improved mixing capabilities. Additionally, as stricter regulations regarding environmental sustainability are being enforced, pneumatic mixers may adopt greener designs, reducing energy consumption and minimizing waste production. Overall, pneumatic mixers are invaluable tools in numerous industries, enabling efficient and consistent mixing processes while contributing to enhanced product quality and production efficiency.
As a professional Pneumatic mixer, FRANLI has provided a complete set of mature equipment for related machines and production lines for more than 60 countries and thousands of industries in the world, and in Russia, Turkey, Spain, Brazil, Malaysia, Indonesia, and other regions, it has provided many An enterprise establishes related production lines.
Welcome to send inquiry to us and let’s make a win win business together !
Guidelines For Pneumatic Mixers
The stirring process of the pneumatic mixer is a single momentum transfer in the fluid field or a process including momentum, heat, mass transfer and chemical reaction. The agitator mainly inputs the energy of the device by making the stirring medium obtain a suitable flow field device.
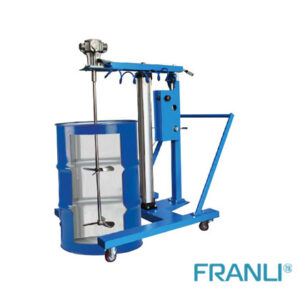
Pneumatic Mixer: Enhancing Efficiency & Productivity in Mixing Processes
A pneumatic mixer, also known as an air-driven mixer or air-powered mixer, is a type of mixer that utilizes compressed air to drive its mixing action.
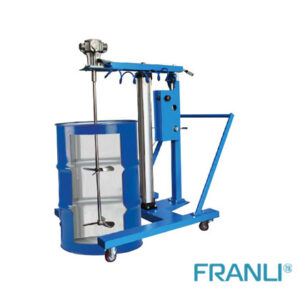
Enhance Efficiency & Quality with Pneumatic Paint Mixers
Pneumatic paint mixers utilize compressed air to generate rotational motion, enabling thorough mixing of paints and coatings. These mixers are equipped with a powerful air-driven motor that connects to a mixing shaft.
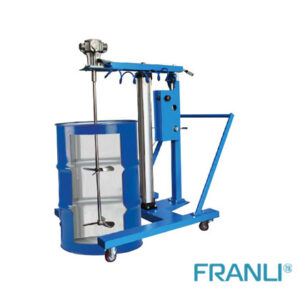
The Application of Pneumatic Mixers in Resins: Enhancing Efficiency & Quality
In the realm of resin manufacturing and processing, pneumatic mixers play a crucial role by simplifying the mixing process, ensuring uniformity, and improving overall quality.
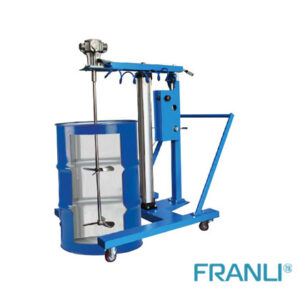
Pneumatic Mixers: Transforming Paint Application in the Coating Industry
Pneumatic mixers are mechanical devices that utilize compressed air to generate rotational motion, effectively blending and homogenizing paint.
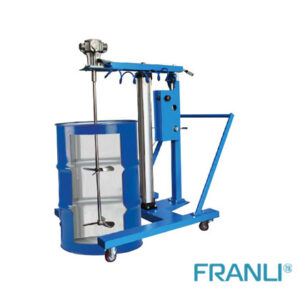
The Application of Pneumatic Mixers in Various Industries
Pneumatic mixers are widely utilized in various industries as a crucial component of the mixing process. These versatile machines utilize compressed air to rotate blades or paddles, enabling efficient and uniform blending of various substances or materials.
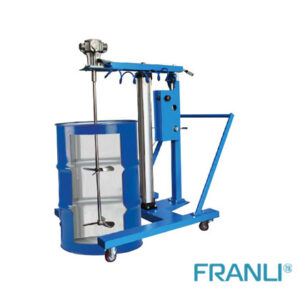
Pneumatic Mixer: Solution for Mixing Applications
A pneumatic mixer is a type of mixing equipment that uses compressed air to drive the mixing mechanism. The mixing mechanism can be a propeller, impeller, or turbine, depending on the application and viscosity of the materials being mixed.