Home » Pneumatic Mixers: Transforming Paint Application in the Coating Industry
Pneumatic Mixers: Transforming Paint Application in the Coating Industry
Pneumatic Mixers
Pneumatic mixers are mechanical devices that utilize compressed air to generate rotational motion, effectively blending and homogenizing paint. These mixers consist of an air motor, impeller, and mixing shaft with blades. By creating a vortex motion within the paint container, pneumatic mixers ensure thorough mixing, eliminating any sedimentation or separation.
Details of Pneumatic Mixers
- The pneumatic mixer can be adjusted steplessly.
- The pneumatic mixer can rotate forward and reverse.
- The working environment of the pneumatic mixer is not affected by vibration, high temperature, electromagnetic, radiation, etc.
- The air motor matched with the air mixer has the function of overload protection, and will not fail due to overload.
- The pneumatic mixer has a high starting torque and can be started directly with a load.
- The pneumatic mixer is easy to operate and easy to maintain and repair.
Application: petroleum, chemical, paint, paint, woodworking, food, daily chemical, and other flammable, dusty, heavy-duty, wet, and other industries.
Paint is an essential component of modern society, used in various applications such as architecture, automotive, and industrial settings. Achieving the desired consistency and homogeneity of paint is crucial for its performance and appearance. Traditional mixing methods often fall short in delivering consistent results, resulting in issues such as lumps, streaks, and uneven color distribution. However, the advent of pneumatic mixers has revolutionized the paint industry by providing efficient and effective solutions for achieving optimal paint blending.
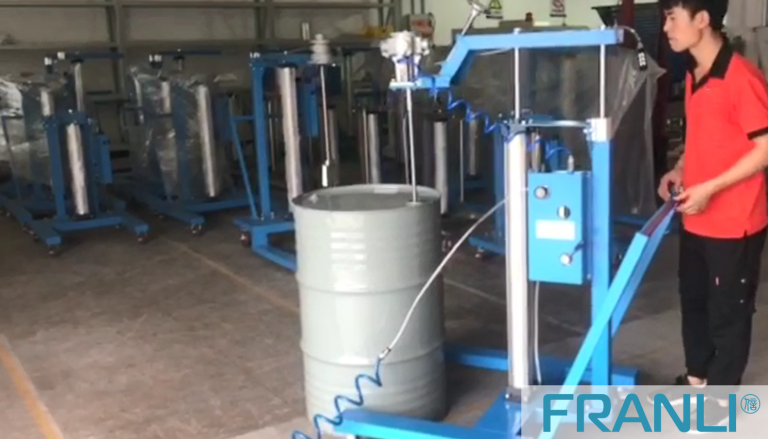
Types of Pneumatic Mixers
There are two primary types of pneumatic mixers used in the paint industry: direct drive and gear-drive mixers. Direct drive mixers rely on the force of compressed air to rotate the mixing shaft directly. On the other hand, gear-drive mixers use gears to transmit rotational force from the air motor to the mixing shaft, providing additional torque for more demanding applications.
Operating Principles of Pneumatic Mixers
Pneumatic mixers work on the principle of converting compressed air pressure into rotational motion. The compressed air is supplied to the air motor, which drives the impeller attached to the mixing shaft. As the impeller rotates, it creates a powerful vortex within the paint, ensuring efficient blending of all components.
Advantages of Pneumatic Mixers in Paint Application
1. Improved Efficiency:
Pneumatic mixers significantly enhance the efficiency of paint blending compared to traditional mixing methods. The strong vortex generated by pneumatic mixers ensures rapid and uniform dispersion of pigments, binders, and additives. This eliminates the need for excessive mixing time, reducing production time and enhancing overall productivity.
2. Homogeneity and Consistency:
Achieving a consistent paint blend with uniform color distribution is critical in the coating industry. Pneumatic mixers excel in this aspect by thoroughly dispersing all components in the paint, removing any lumps or streaks. The homogeneous paint mixture obtained through pneumatic mixing ensures a uniform application, resulting in a high-quality coat.
3. Better Paint Quality:
The efficient blending provided by pneumatic mixers allows for better incorporation of additives and agents, improving overall paint quality. In applications where specialized coatings are required, such as high-gloss or corrosion-resistant paints, pneumatic mixers ensure an even distribution of additives, enhancing paint performance and durability.
4. Time and Cost Savings:
Pneumatic mixers accelerate the paint mixing process, leading to significant time savings in both small-scale and large-scale manufacturing operations. Additionally, by eliminating the need for excessive mixing time and reducing material waste due to uneven blending, pneumatic mixers contribute to cost savings for paint manufacturers.
5. Versatility and Adaptability:
Pneumatic mixers are highly versatile and can be used for various paint compositions, including water-based, solvent-based, and high-viscosity paints. Furthermore, the mixing speed and power of pneumatic mixers can be adjusted to suit different paint types and viscosities, allowing for greater flexibility in paint production processes.
Impact on the Coating Industry
1. Enhanced Productivity and Innovation:
The introduction of pneumatic mixers in the coating industry has significantly enhanced productivity by minimizing paint mixing times and achieving consistent results. This increased efficiency allows manufacturers to allocate resources to other critical areas of production, fostering innovation in paint formulations and development.
2. Quality Control and Compliance:
Pneumatic mixers have also played a vital role in improving quality control measures within the coating industry. By ensuring uniform paint blending, these mixers prevent inconsistencies in paint application, reducing the need for rework and minimizing defects. This, in turn, leads to better compliance with regulatory standards and customer expectations.
3. Reduced Environmental Impact:
Efficient paint mixing with pneumatic mixers minimizes material waste and decreases the release of volatile organic compounds (VOCs) into the environment. By facilitating better material utilization and decreasing the need for excessive mixing, pneumatic mixers contribute to sustainable manufacturing practices within the coating industry.
Pneumatic mixers have revolutionized the paint industry by providing efficient and effective solutions for achieving optimal paint blending. Their ability to create a powerful vortex within the paint container ensures thorough mixing and homogenization, resulting in consistent paint quality and application. With advantages such as improved efficiency, homogeneity, and time/cost savings, pneumatic mixers have become a go-to solution for paint manufacturers across various sectors of the industry. Furthermore, their impact on productivity, quality control, and environmental sustainability cannot be overlooked. As the coating industry continues to evolve, pneumatic mixers will undoubtedly play a pivotal role in shaping the future of paint production and application.
As a professional Pneumatic mixer, FRANLI has provided a complete set of mature equipment for related machines and production lines for more than 60 countries and thousands of industries in the world, and in Russia, Turkey, Spain, Brazil, Malaysia, Indonesia, and other regions, it has provided many An enterprise establishes related production lines.
Welcome to send inquiry to us and let’s make a win win business together !
Guidelines For Pneumatic Mixers
The stirring process of the pneumatic mixer is a single momentum transfer in the fluid field or a process including momentum, heat, mass transfer and chemical reaction. The agitator mainly inputs the energy of the device by making the stirring medium obtain a suitable flow field device.
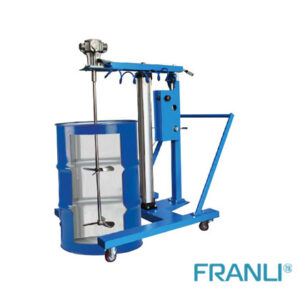
Pneumatic Mixer: Enhancing Efficiency & Productivity in Mixing Processes
A pneumatic mixer, also known as an air-driven mixer or air-powered mixer, is a type of mixer that utilizes compressed air to drive its mixing action.
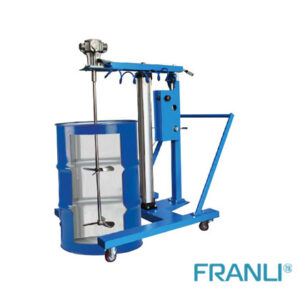
Enhance Efficiency & Quality with Pneumatic Paint Mixers
Pneumatic paint mixers utilize compressed air to generate rotational motion, enabling thorough mixing of paints and coatings. These mixers are equipped with a powerful air-driven motor that connects to a mixing shaft.
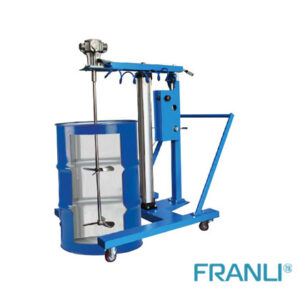
The Application of Pneumatic Mixers in Resins: Enhancing Efficiency & Quality
In the realm of resin manufacturing and processing, pneumatic mixers play a crucial role by simplifying the mixing process, ensuring uniformity, and improving overall quality.
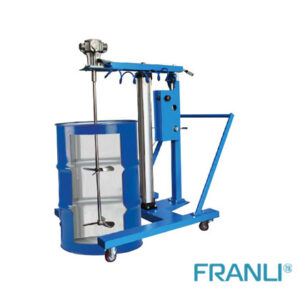
Pneumatic Mixers: Transforming Paint Application in the Coating Industry
Pneumatic mixers are mechanical devices that utilize compressed air to generate rotational motion, effectively blending and homogenizing paint.
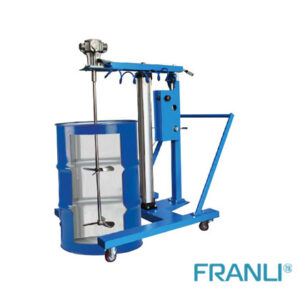
The Application of Pneumatic Mixers in Various Industries
Pneumatic mixers are widely utilized in various industries as a crucial component of the mixing process. These versatile machines utilize compressed air to rotate blades or paddles, enabling efficient and uniform blending of various substances or materials.
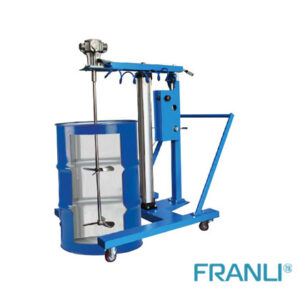
Pneumatic Mixer: Solution for Mixing Applications
A pneumatic mixer is a type of mixing equipment that uses compressed air to drive the mixing mechanism. The mixing mechanism can be a propeller, impeller, or turbine, depending on the application and viscosity of the materials being mixed.