Home » Pneumatic Mixer: Solution for Mixing Applications
Pneumatic Mixer: Solution for Mixing Applications
Pneumatic Mixers
A pneumatic mixer is a type of mixing equipment that uses compressed air to drive the mixing mechanism. The mixing mechanism can be a propeller, impeller, or turbine, depending on the application and viscosity of the materials being mixed. The compressed air is supplied to the mixer through a hose or pipe, which is connected to an air compressor or a compressed air line. The intensity and speed of the mixing action can be adjusted by controlling the air pressure and flow rate.
Details of Pneumatic Mixers
- The pneumatic mixer can be adjusted steplessly.
- The pneumatic mixer can rotate forward and reverse.
- The working environment of the pneumatic mixer is not affected by vibration, high temperature, electromagnetic, radiation, etc.
- The air motor matched with the air mixer has the function of overload protection, and will not fail due to overload.
- The pneumatic mixer has a high starting torque and can be started directly with a load.
- The pneumatic mixer is easy to operate and easy to maintain and repair.
Application: petroleum, chemical, paint, paint, woodworking, food, daily chemical, and other flammable, dusty, heavy-duty, wet, and other industries.
Mixing is an essential process in various industries, including chemical, food and beverage, pharmaceutical, and cosmetics. It involves combining two or more substances to create a homogeneous mixture. The quality and consistency of the mixture depending on the mixing method, equipment, and parameters used. One of the most popular mixing solutions is the pneumatic mixer, which uses compressed air to power the mixing mechanism.
What is a Pneumatic Mixer?
Pneumatic mixers are available in different sizes, shapes, and configurations, depending on the application and the container or vessel that needs to be mixed. Some pneumatic mixers are designed for open tanks, while others are suitable for closed vessels or reactors. The mixing mechanism can be mounted on a stand, a clamp, or a bracket, depending on the accessibility and stability of the mixing location. Most pneumatic mixers are made of stainless steel or other corrosion-resistant materials, which are easy to clean, sanitize, and maintain.
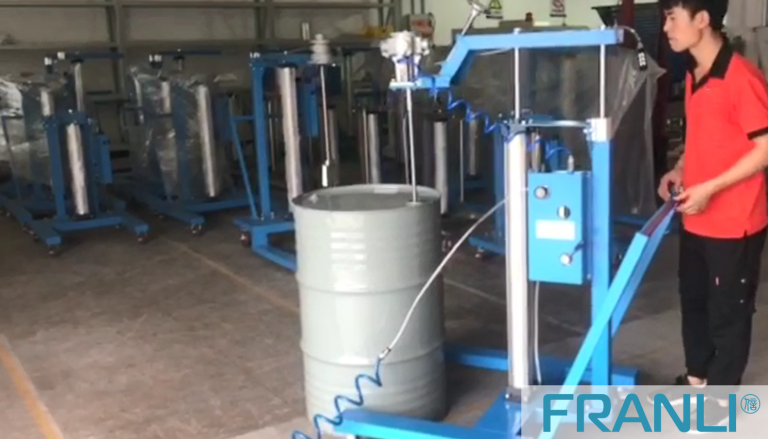
Features of Pneumatic Mixers
Pneumatic mixers have several features that make them a popular choice for mixing applications. Some of the key features are:
Versatility: Pneumatic mixers can be used for a wide range of mixing applications, including blending, emulsifying, dispersing, suspending, and dissolving. They can handle different types of materials, such as liquids, powders, pastes, and slurries, with varying viscosities and densities. They can also mix materials that are sensitive to heat, shear, or other mechanical stresses, without compromising their quality or integrity.
Efficiency: Pneumatic mixers are efficient in terms of energy consumption, mixing time, and labor cost. They require minimal power input, as the compressed air is used to drive the mixing mechanism. They can mix materials quickly and uniformly, without the need for manual intervention or supervision. They can also reduce the risk of contamination, as they can be operated remotely or in a closed system.
Safety: Pneumatic mixers are safe to operate, as they do not generate sparks, heat, or electrical hazards. They are also less likely to cause mechanical damage to the mixing vessel or the materials being mixed, as they do not have direct contact with them. They can also be equipped with safety features, such as overload protection, speed control, and automatic shut-off, to prevent accidents or damage.
Benefits of Pneumatic Mixers
Pneumatic mixers offer several benefits over other types of mixing equipment, such as mechanical mixers, electric mixers, and manual mixers. Some of the main benefits are:
Cost-effectiveness: Pneumatic mixers are cost-effective in terms of initial investment, maintenance, and operation. They are generally less expensive than other types of mixers, as they do not require complex motors, gears, or controllers. They are also easy to install, operate, and maintain, as they have fewer moving parts and require less lubrication or replacement. They can also reduce labor costs, as they can be operated remotely or with minimal supervision.
Flexibility: Pneumatic mixers are flexible in terms of application, location, and configuration. They can be used in various industries, such as chemical, food and beverage, pharmaceutical, and cosmetics, for different types of mixing tasks. They can be installed in different types of vessels, such as tanks, drums, IBCs, and reactors, with various capacities and shapes. They can also be customized to meet specific requirements, such as explosion-proof, sanitary, or high-speed mixing.
Reliability: Pneumatic mixers are reliable in terms of performance, durability, and safety. They can operate continuously or intermittently, without overheating or wearing out. They can also withstand harsh environments, such as corrosive, abrasive, or high-temperature conditions, without deteriorating or contaminating the materials being mixed. They can also ensure operator safety, as they do not pose electrical, thermal, or mechanical hazards.
Applications of Pneumatic Mixers
Pneumatic mixers have a wide range of applications in various industries and processes. Some of the common applications are:
Chemical mixing: Pneumatic mixers are used in chemical mixing processes, such as polymerization, blending, and reaction. They can mix different types of chemicals, such as acids, bases, solvents, and catalysts, with high efficiency and consistency. They can also handle hazardous or toxic chemicals, such as flammable or corrosive substances, without risking operator safety or environmental contamination.
Food and beverage mixing: Pneumatic mixers are used in food and beverage mixing processes, such as mixing powders, liquids, and emulsions. They can mix ingredients, such as flour, sugar, milk, and flavors, to create various food products, such as dough, batter, sauce, and beverages. They can also ensure food safety and hygiene, as they can be easily cleaned and sanitized.
Pharmaceutical mixing: Pneumatic mixers are used in pharmaceutical mixing processes, such as blending, granulation, and coating. They can mix different types of drugs, excipients, and additives, with high accuracy and uniformity. They can also prevent cross-contamination, as they can be operated in a closed system or in a sterile environment.
Cosmetics mixing: Pneumatic mixers are used in cosmetics mixing processes, such as emulsifying, dispersing, and homogenizing. They can mix different types of cosmetic ingredients, such as oils, waxes, surfactants, and pigments, to create various cosmetic products, such as creams, lotions, and gels. They can also ensure product quality and consistency, as they can mix materials with high shear and turbulence.
Pneumatic mixers are a versatile and efficient solution for mixing applications in various industries. They offer several features and benefits, such as versatility, efficiency, and safety, that make them a cost-effective and reliable choice for your mixing needs. They can handle different types of materials, such as liquids, powders, pastes, and slurries, with varying viscosities and densities. They can also mix materials quickly and uniformly, without the need for manual intervention or supervision. They can be used in different industries, such as chemical, food and beverage, pharmaceutical, and cosmetics, for different types of mixing tasks. They can also be customized to meet specific requirements, such as explosion-proof, sanitary, or high-speed mixing. If you are looking for a mixing solution that can improve your productivity, quality, and safety, consider using a pneumatic mixer.
As a professional Pneumatic mixer, FRANLI has provided a complete set of mature equipment for related machines and production lines for more than 60 countries and thousands of industries in the world, and in Russia, Turkey, Spain, Brazil, Malaysia, Indonesia, and other regions, it has provided many An enterprise establishes related production lines.
Welcome to send inquiry to us and let’s make a win win business together !
Guidelines For Pneumatic Mixers
The stirring process of the pneumatic mixer is a single momentum transfer in the fluid field or a process including momentum, heat, mass transfer and chemical reaction. The agitator mainly inputs the energy of the device by making the stirring medium obtain a suitable flow field device.
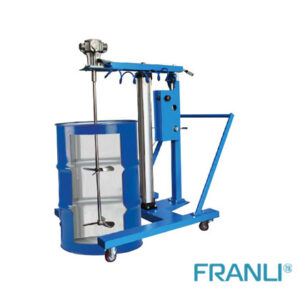
Pneumatic Mixer: Enhancing Efficiency & Productivity in Mixing Processes
A pneumatic mixer, also known as an air-driven mixer or air-powered mixer, is a type of mixer that utilizes compressed air to drive its mixing action.
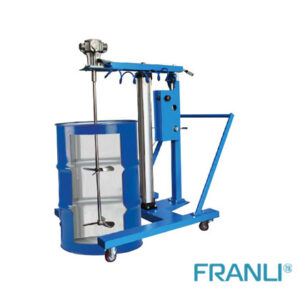
Enhance Efficiency & Quality with Pneumatic Paint Mixers
Pneumatic paint mixers utilize compressed air to generate rotational motion, enabling thorough mixing of paints and coatings. These mixers are equipped with a powerful air-driven motor that connects to a mixing shaft.
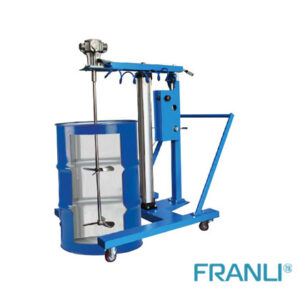
The Application of Pneumatic Mixers in Resins: Enhancing Efficiency & Quality
In the realm of resin manufacturing and processing, pneumatic mixers play a crucial role by simplifying the mixing process, ensuring uniformity, and improving overall quality.
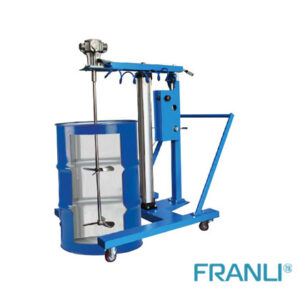
Pneumatic Mixers: Transforming Paint Application in the Coating Industry
Pneumatic mixers are mechanical devices that utilize compressed air to generate rotational motion, effectively blending and homogenizing paint.
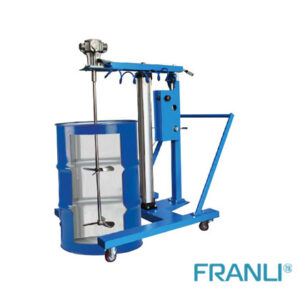
The Application of Pneumatic Mixers in Various Industries
Pneumatic mixers are widely utilized in various industries as a crucial component of the mixing process. These versatile machines utilize compressed air to rotate blades or paddles, enabling efficient and uniform blending of various substances or materials.
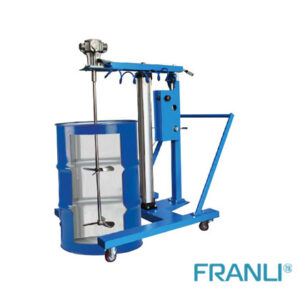
Pneumatic Mixer: Solution for Mixing Applications
A pneumatic mixer is a type of mixing equipment that uses compressed air to drive the mixing mechanism. The mixing mechanism can be a propeller, impeller, or turbine, depending on the application and viscosity of the materials being mixed.