Home » Three Roll Mills|Lab Style & Production Style
Three Roll Mills|Lab Style & Production Style
Three Roll Mill
Details of Three Roll Mill
- Two types: handwheel and digital control gap
- Safe scraper socket, Emergency-stop
- Space-saving desktop models
- Drip tray for easy cleaning
Application: Paint, Adhesive, Battery, Pharmaceutical industry, Cosmetic
- The working principle of the three roll mill
- Uses and Features of Three Roll Mill
- Introduction to the working rules of the three roll mill
- Working procedure of three roll mill
- After the three roll mill stops working
- Instructions for use of three roll mill
- How does a three roll mill work?
- The operation process of the three roll mill
Three roll mill can be divided into two types: experimental three roll mill and production three roll mill. The three roll mill is the most effective grinding and dispersing equipment for high-viscosity materials.
The working principle of the three roll mill
The three roll mill has three rollers installed on the frame, and the center is on the same plane. The three roll mill achieves the grinding effect by squeezing the surfaces of the three horizontal rollers with each other and friction shearing at different speeds.
The three roll mill has the following characteristics:
① With one cycle, it is possible to completely realize the homogenization and dispersion of the material, reduce the particle size, and break the agglomerated particles. The result is a homogeneous slurry that provides the perfect basis for further processing of the material.
② The distance between each roller can be adjusted by the touch screen to ensure perfect parallelism of the rollers. The elastically tensioned blade socket ensures constant blade pressure and does not require readjustment during operation.
③ Rollers of different materials can be used, the choice of roller and scraper material – from stainless steel to alumina, silicon carbide, and zirconia – to meet various needs.
④ The safety device on the three roller mill ensures the maximum safety of the operator, and the machine can be cleaned easily and quickly.
Uses and Features of Three Roll Mill
1. The precision seamless tube ensures the stability of the system;
2. German Siemens PLC system makes product control more accurate (option);
3. The roller pressure and roller gap can be controlled to achieve stable and reproducible product quality;
4. Products produced by manual gap adjustment can be processed within the range of low roller pressure without artificial influence.
The three roll mill is an efficient grinding and dispersing equipment, which plays an irreplaceable role in improving the quality of coating products. The precise design and strict requirements of parts enable the equipment to continuously and stably perform micron-level grinding and dispersion. Unique online gap correction And formula menu function make the equipment operation more flexible and adopt many safety protection measures to ensure the operation safety in the whole production process.
At the same time, modern three-roll machines have realized the networking function of the equipment, which can make data collection and analysis on the computer side feasible.
Introduction to the working rules of the three roll mill
Under normal circumstances, the material of the roller of the grinding machine is the centrifugal casting of chilled cast iron, and the surface hardness is above HS70°; the diameter of the roller is high-precision grinding, which is precise and fine, and the grinding fineness of the material can reach about 15μm. As a result, uniform and delicate high-quality products can be produced.
Models 405, 315, and 260 are used for mass production, and models 160, 120, and 65 are used for small batches or laboratory use. The grinder has three drums mounted on an iron frame with the center in a straight line.
Can be installed horizontally, or slightly inclined. The grinding effect is achieved by the mutual extrusion of the surfaces of the three horizontal rollers and friction at different speeds. The steel drum can be hollow and cooled by water. The material is added between the middle roll and the rear roll.
Because the rotation directions of the three drums are different (the rotation speed increases sequentially from the back to the front), a good grinding effect is produced. After the material is ground, it is scraped off by a scraper installed in front of the front roller.
Working procedure of three roll mill
After starting the operation, adjust the gap between the middle and rear rollers to 0.3 mm, press the baffle plate, add the slurry appropriately, visually inspect the coloring depth, fine-tune the rear rollers so that the coloring is evenly distributed over the rollers, and then lock the fixing nut.
Adjust the hand wheel of the front roller with both hands at the same time, so that the front roller slowly touches the middle roller. After the surface of the front roller is evenly colored, lock the fixing nut, and then adjust the angle of the material plate so that it is properly and lightly pressed on the roller surface, and the slurry can be discharged evenly. Check the uniformity of the discharge and the particle size of the finished product, and continue to fine-tune the front and rear rollers until the particle size of the finished product reaches the predetermined requirements. Back and forth should return the blade knife in time.
After the three roll mill stops working
Remove the paint and clean it in time, wipe the roller and related parts, loosen the knife and the baffle, apply a small amount of oil, and then cover with wax paper for protection.
Instructions for use of three roll mill
Preparation:
1. Check whether the position and locking of each component are normal, inject lubricating oil according to the point shown in the figure, and turn on the power;
2. Adjust the front, rear, left, and right handwheels to observe whether the roller linkage is normal;
3. Remove the dirt on the roller surface: wipe with soft paper or clean cotton yarn, release the knob of the baffle plate;
4. Adjust the gap between the front and rear rollers and the middle roller to 0.5 mm, and then start the power supply to idle for 1-2 minutes.
Work schedule:
1. After starting the operation, adjust the gap between the middle and rear rollers to 0.3 mm, press the baffle plate, add the slurry appropriately, visually inspect the coloring depth, fine-tune the rear rollers so that the coloring is evenly distributed over the rollers, and then lock the fixing nut.
2. Adjust the hand wheel of the front roller with both hands at the same time, so that the front roller slowly touches the middle roller. After the surface of the front roller is evenly colored, lock the fixing nut, and then adjust the angle of the material plate so that it is properly and lightly pressed on the roller surface, and the slurry can be discharged evenly. Check the uniformity of the discharge and the particle size of the finished product, and continue to fine-tune the front and rear rollers until the particle size of the finished product reaches the predetermined requirements. Back and forth should return the blade knife in time.
After work stops:
Remove the paint and clean it in time, wipe the roller and related parts, loosen the knife and the baffle, apply a small amount of oil, and then cover with wax paper for protection.
How does a three roll mill work?
The three roller mill makes the shearing force act on the agglomerated material through the mutual extrusion of the surfaces of the three horizontal rollers and friction at different speeds, to realize the grinding effect of the material from agglomeration to dispersion. Three roll mill is a special machine to realize the above process, commonly known as a “three roll machine”.
Three roll mill is a very effective grinding and dispersing equipment for high viscosity materials.
The operation process of the three roll mill
1. Before use, it is necessary to check whether the position and locking of each part are normal, observe whether the linkage of the rollers is normal, and remove the dirt on the roller surface at the same time.
2. After starting the operation, adjust the gap between the middle and rear rollers to 0.3 mm, press the baffle plate, add slurry appropriately, visually inspect the coloring depth, fine-tune the rear roller to make the coloring evenly spread over the roller, and then lock the fixing nut.
3. Adjust the hand wheel of the front roller with both hands at the same time, so that the front roller slowly touches the middle roller and the surface of the front roller is evenly colored, then lock the fixing nut, and then adjust the angle of the material plate, so that it is properly pressed on the roller surface, and the slurry can be Discharge evenly.
Check the uniformity of the discharge and the particle size of the finished product, and continue to fine-tune the front and rear rollers until the particle size of the finished product reaches the predetermined requirements. The scraper should be returned in time before and after.
4. After the work is stopped, remove the paint and clean it in time, wipe the roller and related parts, loosen the scraper and the baffle, apply a small amount of oil, and then cover it with wax paper for protection.
Welcome to send inquiry to us and let’s make a win win business together !
Guidelines For Three Roll Mill
Three roll mills are widely used in a variety of chemical industries, from medium to high viscosity productions. FRANLI machine can break open all kinds of pigment, UV ink, offset ink, decorative paints, and Lubricants, it also can catch the greatest fineness in cosmetics/ lipstick and electronics industries.
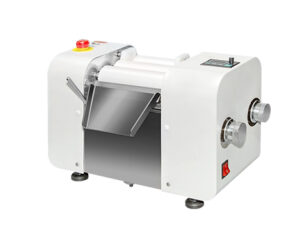
Three Roll Mill For Carbon Black|High Grinding & Dispersion
Three roll mill is the main equipment for grinding colored carbon black, as it is used extensively in rubber, plastics, paints, and inks, and some carbon black is added.
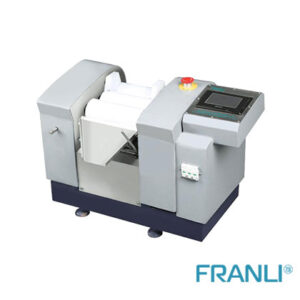
Laboratory Three Roll Mill|PLC Control System & Experimental
The laboratory three roll mill is equipped with the most advanced PLC functions to continuously improve the operability of the most primitive production equipment.
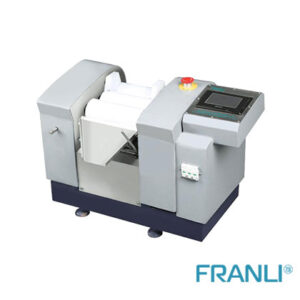
Three Roll Mill For Grease
The three roll mill plays a vital role in the grinding of grease. Grease is essentially a kind of lubricating oil, which is a solid or semi-solid product formed by one or more thickeners through the grinding and dispersing action of a three roll mill.
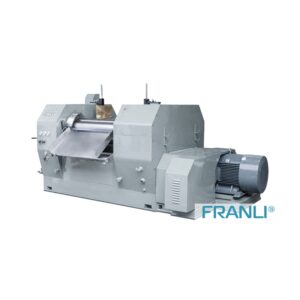
Three Roll Mill For Attapulgite
Three roll mill is the main equipment for grinding attapulgite. The attapulgite is ground and dispersed mainly because it is a natural colloid. Even if the size of the attapulgite reaches 0.1mm, it cannot be easily dispersed by the machine, so the final state of attapulgite formation has been greatly developed.
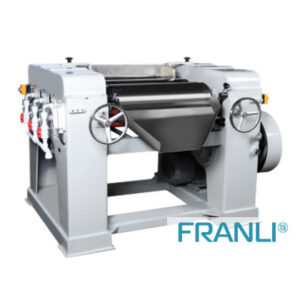
Rolls of a three-roll mill
The three-roll mill is mainly used for grinding materials of various viscosities and is one of the best wet grinding equipment. The dispersing and emulsification effect of the three-roll mill is excellent, especially for ink, paint, colloid, chocolate, plastic, cosmetics, etc., whether it is liquid slurry or paste material, the three-roll mill can work easily.
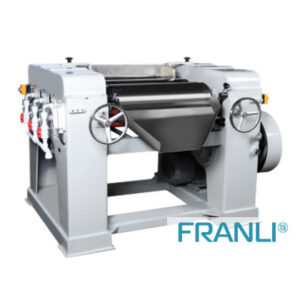
3 roll mill|Failure of the roll shaft & pulley
The 3 roll mill is a grinding and dispersing equipment, which plays an irreplaceable role in improving the quality of coating products.