Home » Pneumatic Mixer|Mixing & Stirring
Pneumatic Mixer|Mixing & Stirring
Pneumatic Mixers
Details of Pneumatic Mixers
- The pneumatic mixer can be adjusted steplessly.
- The pneumatic mixer can rotate forward and reverse.
- The working environment of the pneumatic mixer is not affected by vibration, high temperature, electromagnetic, radiation, etc.
- The air motor matched with the air mixer has the function of overload protection, and will not fail due to overload.
- The pneumatic mixer has a high starting torque and can be started directly with a load.
- The pneumatic mixer is easy to operate and easy to maintain and repair.
Application: petroleum, chemical, paint, paint, woodworking, food, daily chemical, and other flammable, dusty, heavy-duty, wet, and other industries.
The role of the pneumatic mixer is inseparable from its motor. The motor drives the agitator to rotate at a certain speed after the speed is changed by the reducer. Generally, according to the characteristics and needs of the material, different stirring speeds are selected, and fluids of different speeds are discharged from the impeller, this rotating fluid attracts the surrounding liquid at the same time, making the surrounding static flow or low-speed flow involved, thus synthesizing a complex motion flow. This synthetic motion flow has both horizontal circulation flow and up-and-down circulation flow along the wall surface and the stirring shaft. This circulation flow can involve a large range in the mixing tank and play a role in volume circulation, to realize the desired material flow state.
Features of the Pneumatic mixer
1. There are many types of pneumatic mixers, but they mainly use explosion-proof air motors, which have high safety. Not only that, but the pneumatic mixer also has the characteristics of strong power and stable performance. Users can easily operate and steplessly adjust Fast, safely, and easily.
2. The pneumatic lifting mixer is mainly based on the automatic lifting of the cylinder, and the intermediate stop control is used to stir the liquid material, which saves time and effort and is easy to operate. The pneumatic lift adopts standardized design and manufacture, the frame structure is firm, and the maintenance is convenient and simple.
3. The pneumatic mixer can run at full load. When the machine is overloaded, it will only slow down or stop the speed. Once the load is removed, it will resume operation without mechanical failure.
4. Pneumatic mixers have a wide range of applications, mainly for: paint, ink, floor production lines, coating production lines, chemicals, food, automobiles, motorcycles, electronics, container ships, cosmetics, flavors and fragrances, shoe factories, leather factories, wood Product factories, handicrafts, papermaking, adhesives, tire manufacturing, water treatment, and other places.
How to maintain a Pneumatic mixer
1. After the new machine starts running for 200-300 hours, it is necessary to replace the lubricating oil of the reducer and clean the internal oil. And when working continuously for more than 10 hours a day, the lubricating oil should be replaced every 3 months; if the working time is less than 10 hours a day, the lubricating oil should be replaced every 6 months. Regarding the use and maintenance of reducers and motors, FRANLI provides corresponding instruction manuals, and users can refer to the instruction manuals.
2. When the machine is working normally, there should be a special inspection once or twice per shift. If abnormal conditions are found, such as electric leakage, abnormal noise, loose stirring shaft, shaking of the whole machine, etc., stop the machine in time, find out the cause, and continue to run after troubleshooting.
3. The user should also regularly check the swing of the stirring shaft, and remove the windings on the wheel and shaft in time.
4. Regularly check the rotating parts for abnormal sound and temperature rise.
5. Regularly check whether the current has abnormal changes.
6. After the equipment does not work for a long time, if you want to start it up again, you need to check the insulation of the motor before use, and at the same time prevent the sediment from accumulating for a long time, which will cause difficulty in starting and damage the motor and impeller.
As a professional Pneumatic mixer, FRANLI has provided a complete set of mature equipment for related machines and production lines for more than 60 countries and thousands of industries in the world, and in Russia, Turkey, Spain, Brazil, Malaysia, Indonesia, and other regions, it has provided many An enterprise establishes related production lines.
Welcome to send inquiry to us and let’s make a win win business together !
Guidelines For Pneumatic Mixers
The stirring process of the pneumatic mixer is a single momentum transfer in the fluid field or a process including momentum, heat, mass transfer and chemical reaction. The agitator mainly inputs the energy of the device by making the stirring medium obtain a suitable flow field device.
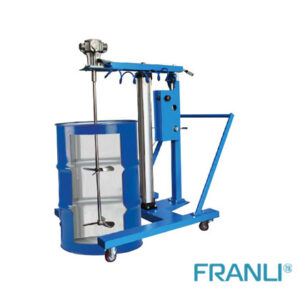
Pneumatic Mixer: Enhancing Efficiency & Productivity in Mixing Processes
A pneumatic mixer, also known as an air-driven mixer or air-powered mixer, is a type of mixer that utilizes compressed air to drive its mixing action.
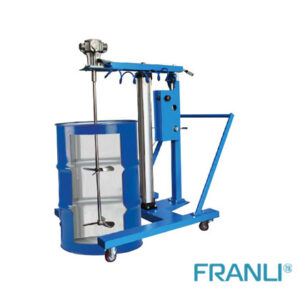
Enhance Efficiency & Quality with Pneumatic Paint Mixers
Pneumatic paint mixers utilize compressed air to generate rotational motion, enabling thorough mixing of paints and coatings. These mixers are equipped with a powerful air-driven motor that connects to a mixing shaft.
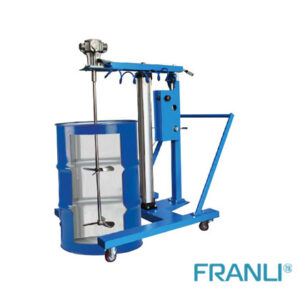
The Application of Pneumatic Mixers in Resins: Enhancing Efficiency & Quality
In the realm of resin manufacturing and processing, pneumatic mixers play a crucial role by simplifying the mixing process, ensuring uniformity, and improving overall quality.
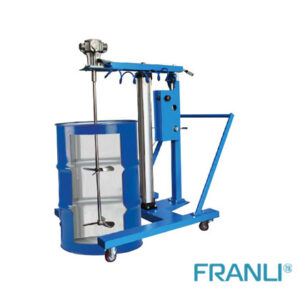
Pneumatic Mixers: Transforming Paint Application in the Coating Industry
Pneumatic mixers are mechanical devices that utilize compressed air to generate rotational motion, effectively blending and homogenizing paint.
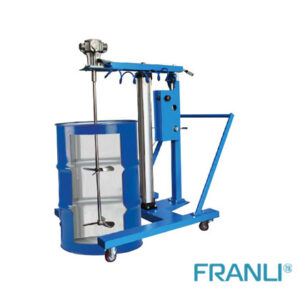
The Application of Pneumatic Mixers in Various Industries
Pneumatic mixers are widely utilized in various industries as a crucial component of the mixing process. These versatile machines utilize compressed air to rotate blades or paddles, enabling efficient and uniform blending of various substances or materials.
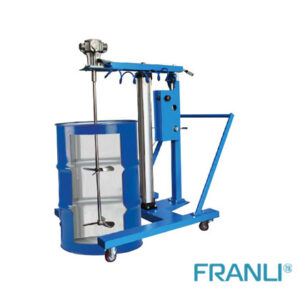
Pneumatic Mixer: Solution for Mixing Applications
A pneumatic mixer is a type of mixing equipment that uses compressed air to drive the mixing mechanism. The mixing mechanism can be a propeller, impeller, or turbine, depending on the application and viscosity of the materials being mixed.