Home » Kneader: How to deal with high temperature and insufficient pressure
Kneader: How to deal with high temperature and insufficient pressure
Kneader
Details of Kneader
- The machine comprises a motor, cover press, main body, mixing chamber and rotor mechanism, gearbox, air control system, tilting machine, heating/cooling system, rubber belt transmission and base, etc.
- The kneader can be made into vacuum, pressure, atmospheric, Normal temperature, high temperature, low temperature, etc.
- The temperature adjustment method of a kneader can be the jacket, halfpipe, far-infrared tile, steam, hot water, heat transfer oil, electric heating, cooling water, chilled water, and other methods.
Application: Paint, Adhesive, Battery, Pharmaceutical industry, Cosmetic
The kneader can be used for mixing, kneading, crushing, dispersing, and re-aggregating materials into various chemical products, and it has complete functions, a wide variety of specifications, and a wider range of uses. The kneader has many advantages such as uniform mixing, no dead angle in stirring, and very high mixing efficiency.
Since the kneader is generally directly welded on the fixed base, the user can directly put the equipment on the ground without installation, and the whole use process is very convenient. Generally speaking, the kneader also needs a certain pressure during the reaction process, and the kneader has very high-pressure requirements. If the pressure is insufficient or too large, it will affect the normal working state of the kneader.
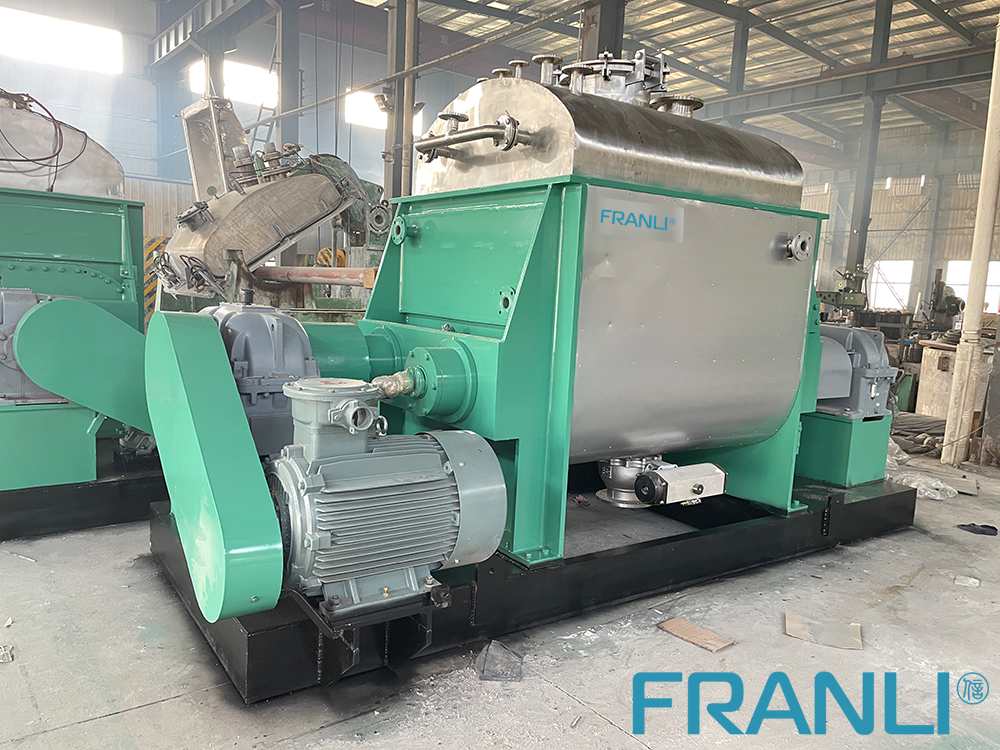
The main hazards of insufficient pressure in the kneader
1. When the steering of the hydraulic pump or motor of the equipment is incorrect, the user needs to check and deal with it in time.
2. When the motor coupling is worn out, the user needs to check regularly and replace the coupling in time.
3. If there is a problem with the anti-vibration device, it needs to be checked and fastened or replaced with a new shock-absorbing device.
4. When the key on the drive shaft of the motor or hydraulic pump is cut, the user needs to check it in time and deal with it properly.
Kneader operating environment requirements
The environment used by the kneader is relatively strict. Generally, the environment of the working workshop will have a certain impact on the vacuum kneader, such as humidity, temperature, power supply, voltage, vibration, frequency, interference, etc., so the vacuum kneader has certain requirements for the on-site environment.
Ambient temperature: -5℃~40℃
Relative temperature: 45%~95%
Atmospheric pressure: 86~106kPa
The power supply voltage is 380V±19V.
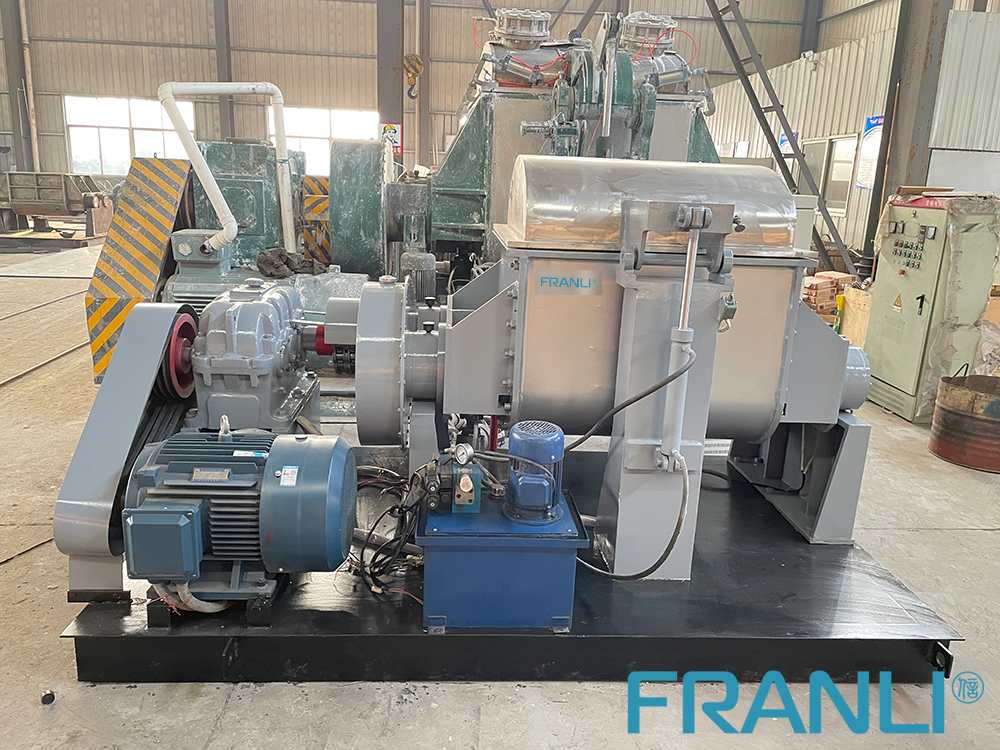
In addition to the above requirements, moisture, moisture or severe dust should be avoided around the vacuum kneader, and there should be no high-frequency equipment, electric welding machines, and other equipment that interfere with the work near the kneader. It is necessary to install protective, moisture-proof, anti-corrosion, dust-proof, anti-vibration, and cooling devices and overload protection devices to create a good working environment for the normal operation of the vacuum kneader.
During the use of the kneader, some problems occasionally occur, the most common of which is the increase in the oil temperature and the surface temperature of the components in the hydraulic system of the kneader. So how do we cool down when encountering high temperatures?
1. The temperature caused by use is too high. High ambient temperature, poor water cooling conditions, too high or too low oil viscosity, too high adjustment power, foreign matter clogging in the hydraulic system, etc. will also cause the oil temperature to rise. Due to oil pollution and other reasons, the oil caused by plane friction cannot be sucked into the hydraulic pump, and high temperature will be generated in the pump and transmitted to the surface of the hydraulic pump. The solenoid valve is not sucked in place to increase the current, causing severe solenoid heating and burning the solenoid.
2. The temperature rise caused by improper design is too high. The volume of the fuel tank is too small, and the heat dissipation area is not enough; there is no unloading circuit in the system, and the hydraulic pump is still in a high-pressure overflow state when the hydraulic pump stops working; the oil pipe is too long, too thin, and has too many bends; or the selection of hydraulic components is improper, so the pressure loss is too large. Some of them belong to manufacturing problems, such as low part processing and assembly accuracy, excessive friction and heat between moving parts or serious leakage, volume loss, etc.
3. High-temperature rise caused by hydraulic component wear or system leakage. When the hydraulic pump is worn, a large amount of leakage oil flows back from the drain chamber to the suction chamber, causing throttling and heating. The situation with the components is similar, if there is an accidental leak in the hydraulic system of the kneader, throttling, and heating will also cause the oil temperature to rise sharply.
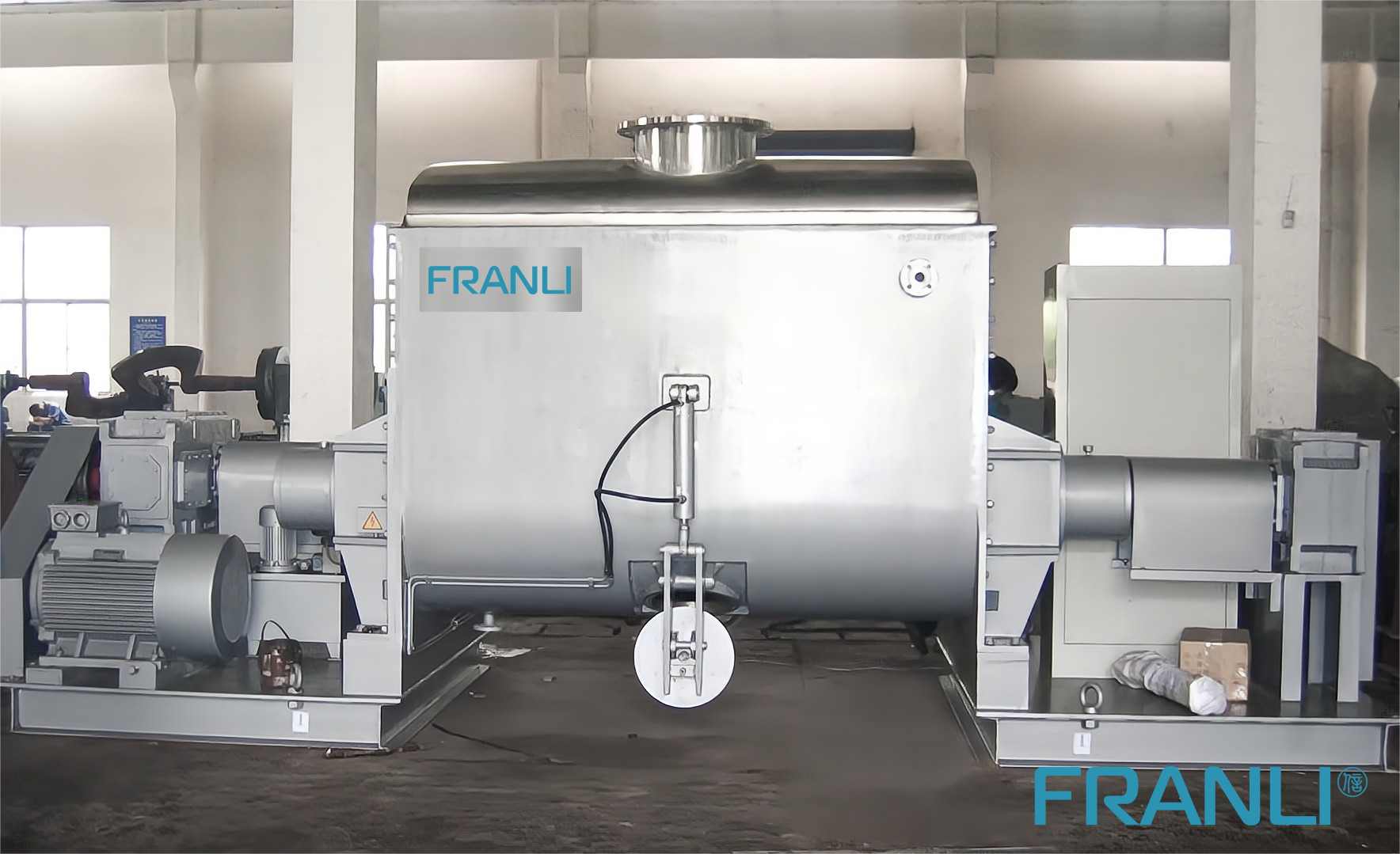
Abnormal high temperature is harmful to the kneader, so we must pay more attention to avoid damage to important parts of the kneader and delay production and processing due to abnormally high temperature.
During the whole operation process, due to the uneven force on the shaft caused by the beating of the mixing slurry, it is easy to cause the static ring to break, especially the static ring of the mechanical seal on the opposite side of the gearbox, because it is far away from the transmission power point, it is easier Fracture occurs.
As a professional kneader manufacturer, FRANLI has provided a complete set of mature equipment for related machines and production lines for more than 60 countries and thousands of industries in the world, and in Russia, Turkey, Spain, Brazil, Malaysia, Indonesia, and other regions, it has provided many An enterprise establishes related production lines.
Welcome to send inquiry to us and let’s make a win win business together !
Guidelines For Kneader
The dispersion kneader is suited for rubber and plastic mastication, as well as the blending of different rubber and plastic components. Small and medium-sized rubber and plastics manufacturers with a wide range of product types and colours, as well as food, dyes, pharmaceuticals, and ceramics, can benefit from the internal mixer.
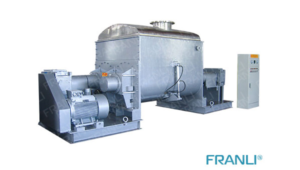
Sigma Kneader: The Solution for Mixing and Kneading
Sigma kneader is a versatile machine that can be used for mixing, kneading, and homogenizing a wide range of materials, including high-viscosity products.
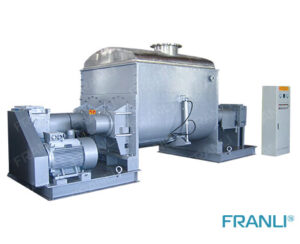
Sigma Mixer: Indispensable Equipment For Manufacturing
Sigma Mixer is a type of mixer that uses a unique mixing principle to achieve an efficient blending of materials. The mixer consists of two blades that rotate in opposite directions, creating a kneading and folding action that ensures thorough mixing. The blades are shaped like the Greek letter Sigma, hence the name Sigma Mixer.
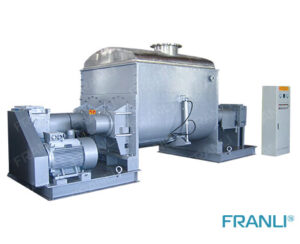
Sigma Blade Mixer: The Mixing Solution
The Sigma Blade Mixer is a robust and reliable mixing machine that uses a unique mixing principle to achieve superior results. It is a type of double-arm kneading mixer that features two blades that rotate in opposite directions.
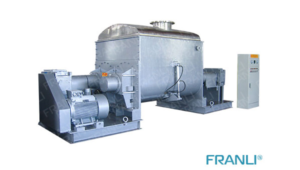
Vacuum Kneader: A Machine for Your Mixing Needs
The Vacuum Kneader is a type of mixer that utilizes a vacuum chamber to create a homogeneous mix of ingredients. It is designed to knead, mix, and disperse high-viscosity materials under vacuum conditions, resulting in a superior product.
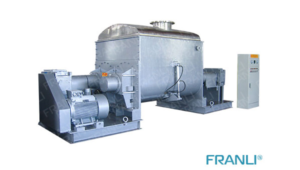
Efficiency and Effectiveness of Dispersion Kneader
The dispersion kneader has complete control over the mixing and blending of the raw materials to create an even mix that allows for better distribution. This device contains a mixing chamber with rotating blades made of high-quality steel.
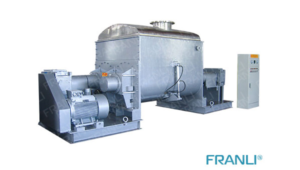
Vacuum kneader: high efficiency and environmental protection
A vacuum kneader is mainly used for stirring, mixing, and kneading high-viscosity and elastic-plastic materials. The most common fields include high-viscosity sealant, silicone rubber, neutral acid glass glue, chewing gum, bubble gum, aluminum silver paste, silica gel, paper pulp, cellulose, and other materials. It covers food, agrochemical, pharmaceutical, cosmetics, electronic paste, and other industries, and has been sought after by the industry.