Home » Ointment Mill: The Most Complete User Guide
Ointment Mill: The Most Complete User Guide
Ointment Mill
Ointment mill intends to utilize a shear force, which has the potential of reducing the particle sizes, homogenize the viscous materials and disperse agglomerates. The potential of shear force is brought into action with the help of three rollers that are positioned within this mill, preferably rotating within opposite directions. These rollers rotate at varying speeds that are relatively measured to one another.
Details of Ointment Mill
- Two types: handwheel and digital control gap
- Safe scraper socket, Emergency-stop
- Space-saving desktop models
- Drip tray for easy cleaning
Application: Paint, Adhesive, Battery, Pharmaceutical industry, Cosmetic
Ointment Mill pulls the entire product through the gap in between those rollers. As a result, you get the precise, narrow, and controllable size distribution of the particle. The gap widths of those rollers are adjustable and can be increased or decreased in order to precisely control the size of particles. The name of these three rolls handling the major application of the ointment mill process is feed roll, center roll, and apron roll.
Process of Using the Ointment Mill
To help you better understand the functionality of Ointment mill within the ointment industry, here are the steps to execute the process. The steps are as follows:
Firstly, the premixed product is placed in a systematic manner within the hopper.
The product is then drawn between the center roller and the feed roller. The product is then finely grounded while it passed through these two rollers.
While the product reaches the bottom section of the center roller, the product then gets transported to the next gap between the center roller and apron roller.
And this is the area or gap where the product is homogenized and is grounded for one more time.
Now, the final product is then removed from the end of apron roll. There is a scraper system within the ointment mill that is important for the final product to come out of the system.
The substance that is processed from the ointment mill has a regular & fine consistency. It is not the same with any other conventional mixing process, as the crystalline substances will still be visible in the final product.
Remedy to the Cream Splashing Problem with Ointment Mills
The ointment mill is one of the best machinery for processing a substance. But at times, inappropriate settings will result in the cream splashing out through the apron roller. And it is not any malfunction, but simple setting disorientation. This problem is easy to prevent by adapting the right considerations and remedies. Here are the things that you need to keep in mind in order to avoid splashing the cream within Ointment mills:
1. The Gap Sizes Should be Suitable
The apron or the front roller has a faster spinning speed than that of the rear or feed roller. Therefore, the balance between the input and output roller is not in proportion. To seek an ideal balance between them, it is recommended to go along with setting a bit larger gap for the feed and center roller.
This gap should not be too big than that of the center and apron roller. It is because a large gap size at the rear will increase the speed of feed roller and will slow down the apron or output roller. And the result will be spilling or splashing of the cream from the feeding roller sides. For instance, you should set the rear roller gap as ‘3’, whereas, for the output or front roller, it should be ‘1’. It will prevent splashing of the cream!
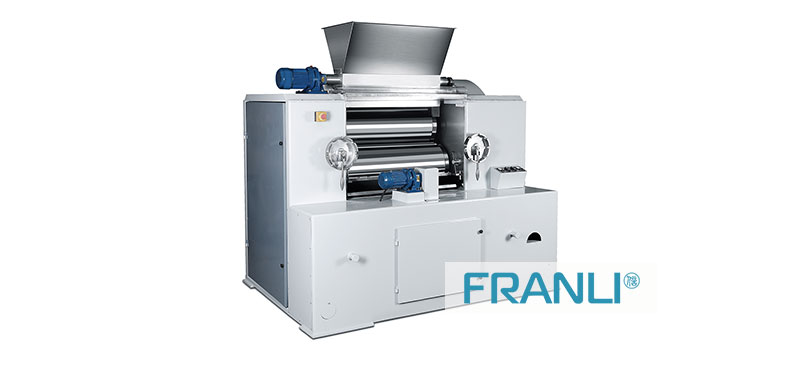
2. Inspect the Condition of Scraper and Plastic Guides
The plastic guides should be set properly upon the top portion of the rollers. It is because inappropriate settings will leave some gaps within the rollers and guides. And there is a possibility that the cream will leak through those small gaps.
Similarly, if there is any sort of big gap in between the scraper and apron or front roller, then the cream collection by the roller won’t be sufficient. Hence, it will become a leader to larger input than that of the output. As a result, the cream will splash out again to create a mess.
Therefore, it is advised for the ointment mill technicians to check the setting of scraper and plastic guides before starting the process.
3. Maintain a Low Speed (If Necessary)
One of the most evident reasons for the ointment mill to splash the cream out is high-speed running. The technicians, in order to speed up the mixing process, run the mill at maximum speed. It helps generate high productivity with more products in a short span of time. But, when the rollers operate at their maximum speed, the creams will become thinner.
Hence, the thinner creams have a high potential of easily splashing around. It is because they cannot just stick anymore with the rollers due to their speed of motion. Therefore, it is better to keep the rollers at optimal speed to maintain the thickness of cream. Thick creams adhere to rollers and have fewer chances of splashing around.
The Efficacy of Ointment Mill
There is a plethora of features and benefits associated with ointment mills. You just have to get an insight into it before you can get yours right away. To help you state the efficacy of ointment mill, here is the list of some features associated with it:
You can preferably get options to pick either hand wheel gap control mechanism or digital gap control mechanism.
The best ointment mill has a safe scraper socket and emergency stop mechanism to avoid splashes and other faults.
The latest versions of ointment mill come with drip trays to support easy cleaning attributes.
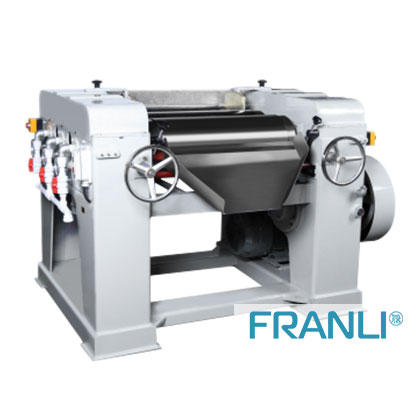
The roller materials are often ceramic, which is highly durable and efficient in terms of output.
The modern-day ointment mill offers a super-quiet operation.
Ointment mills within the ointment industry are booming, and many companies are willing to get the best version of these mills to produce creams, gels, pastes, and ointments for their customers. So, if you are convinced about the true potential of Ointment mill, and have paused the search for buying the best one, then Franli is here for your rescue. Put an end to your search for best ointment mill, and head to the website of Franli to find the product you need. They have a traditional lab three roll mill, smallest size three roll mill, PLC Lab three roll mill, and other such options for you to buy.
Welcome to send inquiry to us and let’s make a win win business together !
Guidelines For Three Roll Mill
Three roll mills are widely used in a variety of chemical industries, from medium to high viscosity productions. FRANLI machine can break open all kinds of pigment, UV ink, offset ink, decorative paints, and Lubricants, it also can catch the greatest fineness in cosmetics/ lipstick and electronics industries.
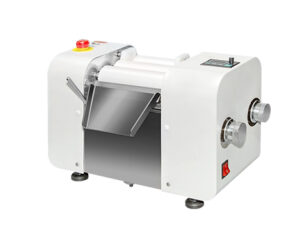
Three Roll Mill For Carbon Black|High Grinding & Dispersion
Three roll mill is the main equipment for grinding colored carbon black, as it is used extensively in rubber, plastics, paints, and inks, and some carbon black is added.
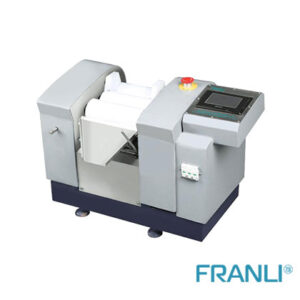
Laboratory Three Roll Mill|PLC Control System & Experimental
The laboratory three roll mill is equipped with the most advanced PLC functions to continuously improve the operability of the most primitive production equipment.
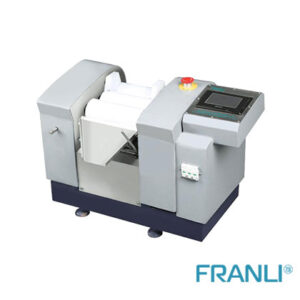
Three Roll Mill For Grease
The three roll mill plays a vital role in the grinding of grease. Grease is essentially a kind of lubricating oil, which is a solid or semi-solid product formed by one or more thickeners through the grinding and dispersing action of a three roll mill.
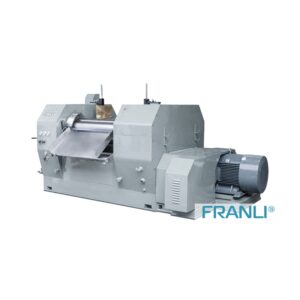
Three Roll Mill For Attapulgite
Three roll mill is the main equipment for grinding attapulgite. The attapulgite is ground and dispersed mainly because it is a natural colloid. Even if the size of the attapulgite reaches 0.1mm, it cannot be easily dispersed by the machine, so the final state of attapulgite formation has been greatly developed.
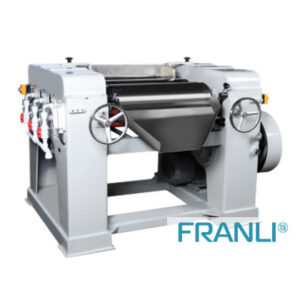
Rolls of a three-roll mill
The three-roll mill is mainly used for grinding materials of various viscosities and is one of the best wet grinding equipment. The dispersing and emulsification effect of the three-roll mill is excellent, especially for ink, paint, colloid, chocolate, plastic, cosmetics, etc., whether it is liquid slurry or paste material, the three-roll mill can work easily.
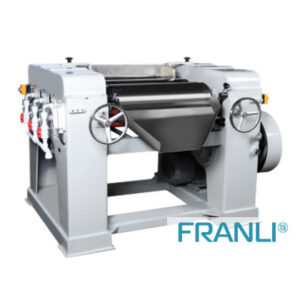
3 roll mill|Failure of the roll shaft & pulley
The 3 roll mill is a grinding and dispersing equipment, which plays an irreplaceable role in improving the quality of coating products.