Home » The Importance of Bead Mill and its Manufacturers
The Importance of Bead Mill and its Manufacturers
Benefits of Bead Mill
❖ Ultrafine dispersion of liquids with low to medium viscosity and nano-particles Grinding
❖ Catering industries like inks, paints, agrochemicals, pharmaceuticals
❖ Production of nano emulsion and dispersion.
Bead mill machines are used in industries.
What You Need to Know About Bead Mill?
The different discharging materials can lead to cement ball mills being divided into two types: main discharging type or circuit discharging type. The discharging portion’s hollow shaft neck is larger than the overflow ball mill. This is because it reduces the bead mill machine speed through the pulp and speeds up the slurry level. The cement pressure and the grinding force are used to grind the ore and rock. The cement is first broken down into thick beads and then ground to smaller particles. Concrete and cement are the lines between contact and ball and goal. During this time, the inner is lifted along the rotation. This is similar to the article cement screen effect, which makes fine-grain pass through cement seam. It also helps break down a thick bead, which allows the coarse grain to concentrate in areas where the grinding medium blows. This grinding machine is very selective and produces a uniform granularity. The over-grinded products, however, are rare.
Disc Type Bead Mill
Next Level business growth
These are the applications: Synthetic enamels. Red oxide primers. Water-based primers. Artist colors. Flexography inks. Industrial Finishes. Designs have horizontal and Vertical bead mill working principle that can be used for the wet Grinding of many materials, including Pigments, Dyes, Pigments, Paints, Minerals, and other types of chemicals. This machine is used primarily for the reduction of material size. These Bead Mills can be used for continuous dispersion or fine wet Grinding of high- and low-viscosity pumpable fluids.
Rotating the beads with the help of the discs attached to the agitator provides the energy required for grinding. Grinding beads transfer energy to the material. High shear and high peripheral speeds reduce the size of the material being ground.
Machine Bead Mill- The Basics
Copyright Notice :
This article only represents the author’s point of view.
This article is published under the authorization of the author.
Source: Franli
This article address : The Importance of Bead Mill and its Manufacturers
Related Products
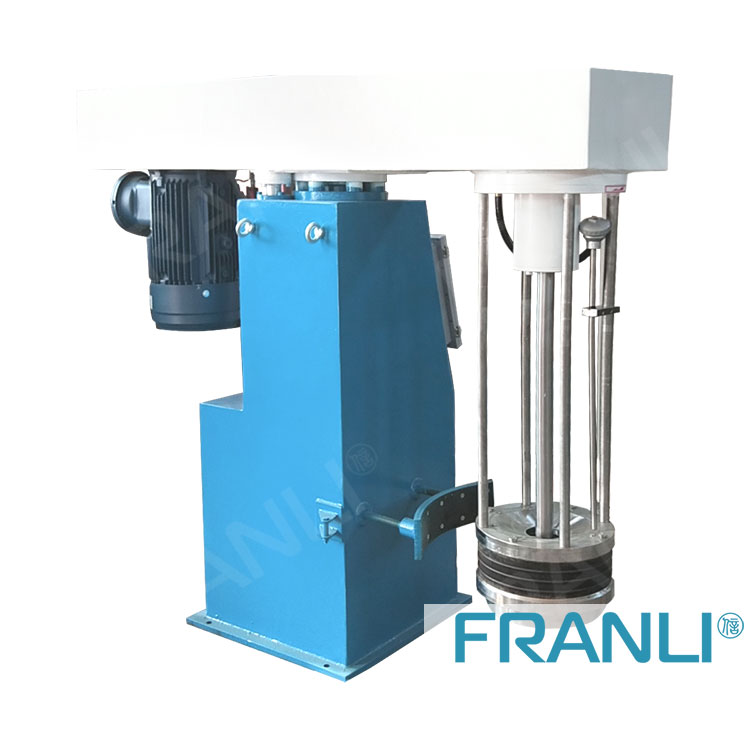
Basket Mill
Franli Basket Mill focuses on low energy, no hot spots, controlling constant temperature, higher production, the flexibility of batch size, and a wide range of product viscosities that can be processed well.
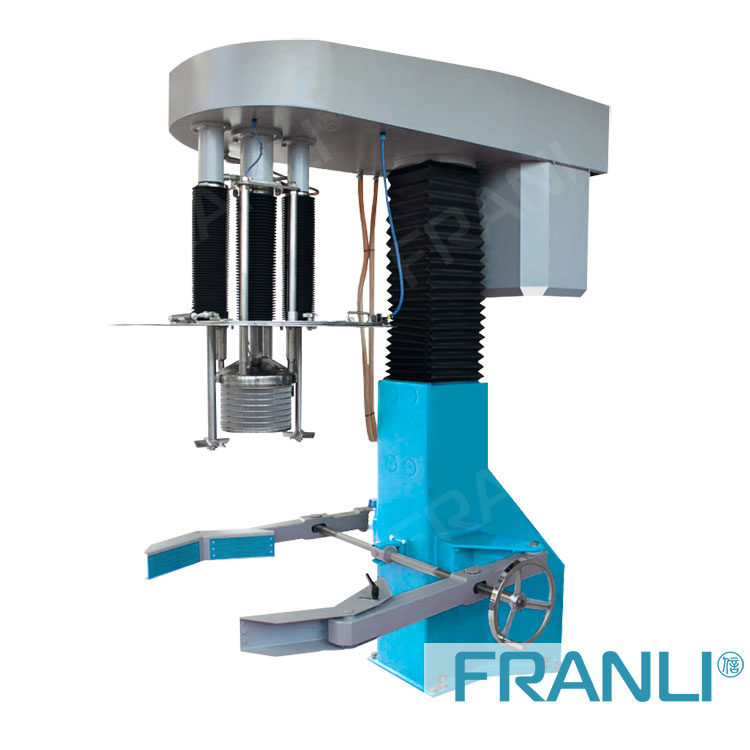
Basket Mill With Mixer
Basket mill with mixer is an indispensable equipment in coatings, ink, cosmetics, and other industries. Its main function is to provide multi-functional dispersion.
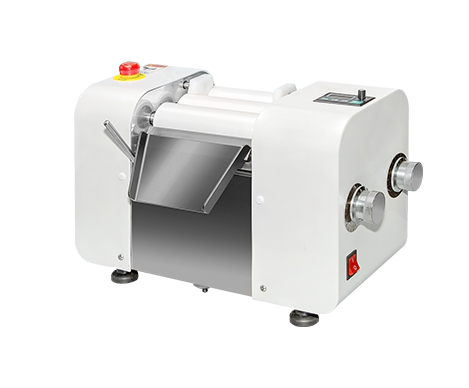
Ceramic Three Roll Mill
The ceramic three roller mill mainly uses the surface of three rollers to grind and disperse at different speeds to make the ground material reach the required grinding fineness. The three roller mill is suitable for the grinding of ink, paint, paint, lipstick, chocolate, soap, and other materials, and it is mainly composed of a roller, a machine base, a guide cover, a discharge knife plate, a feeding copper knife, a cooling system, etc. The fineness of the material grinding can be adjusted by the screw on the base.
News
Laboratory Reactor: Guide to Stirring System
The laboratory reactor is composed of a pot body, a pot cover, an agitator, a jacket, a support and transmission device, a shaft seal device, etc.
Grinding Media for Bead Mill | Zirconia Beads & Zirconium Silicate Beads
Bead mills mainly use grinding balls as media, and use impact, extrusion, and friction to achieve the final grinding effect, which mainly depends on the size and hardness of the grinding beads, the filling rate of the grinding beads, and the collision frequency adjustment between the grinding beads and the particles.
Overview of Laboratory Reactor
Laboratory reactors, also known as lab reactors, are essential tools in scientific research, product development, and process optimization. These reactors provide a controlled environment for conducting chemical reactions, mixing, dispersing, and homogenizing processes.
Bead mills | Manufacturing technology in various industries
Bead mills, also known as sand mills or grinding mills, are versatile machines widely used across various industries for the wet grinding and dispersion of solid particles in liquid media.
Ribbon Blender Mixer Equipment
A ribbon blender mixer, also known as a ribbon mixer or horizontal ribbon blender, is a powerful industrial machine designed for thorough and efficient blending of various materials.
What is A Stainless Steel Reactor?
Stainless steel reactors are essential equipment in various industries, including chemical, pharmaceutical, biotechnology, and food processing.