Home » Reasons for the popularity of high shear mixers
Reasons for the popularity of high shear mixers
Mixing the various components that can help to achieve the suitable foods, topical creams, lotions, cosmetics, etc., can all be achieved with the use of high shear mixer and technology as primitive as the mortar and pestle to note this technically. High shear mixers offer the kind of mixing that can only be achieved with the use of this for the highly homogenized and often emulsified products here. The high shear mixer is capable of dispersing the powdered solids into their highly viscous liquids, thereby emulsifying the other immiscible liquid and other disparate substances.
Over the specific set of competing mixing technologies, the best of the high shear disperser offers the most distinctive set of advantages here that would be ranging over the specific competing mixing technologies present.
The technology of high shear mixing is sure to offer a wide range of benefits for numerous products across a massive range of industries here. Without this kind of technology, which would be facilitating the main tasks including efficient powder dispersion, emulsification, submicron homogenization, deagglomeration, wet milling, etc. are sure would make the manufacture of the products here is extremely difficult.
Benefits you can derive through the high shear mixer.
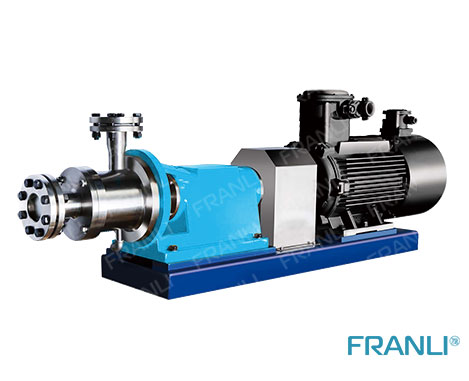
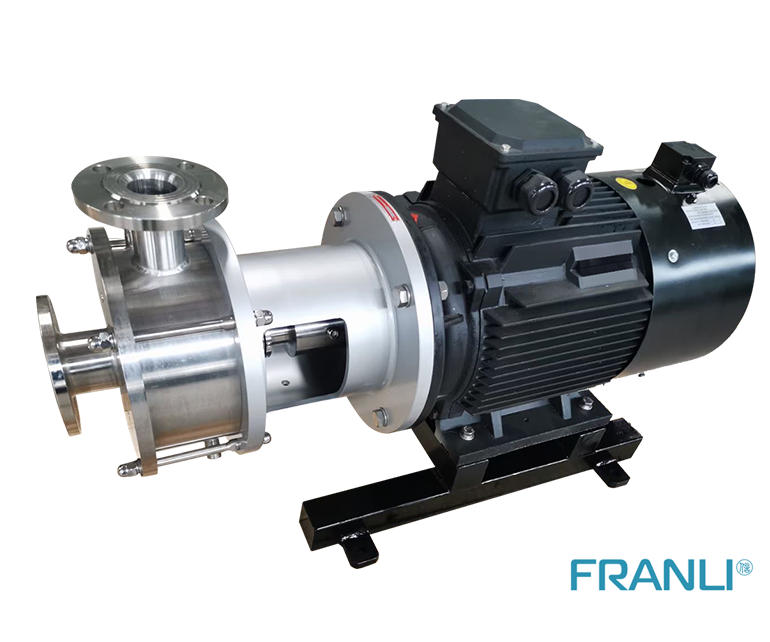
Inline Saves Time and Money
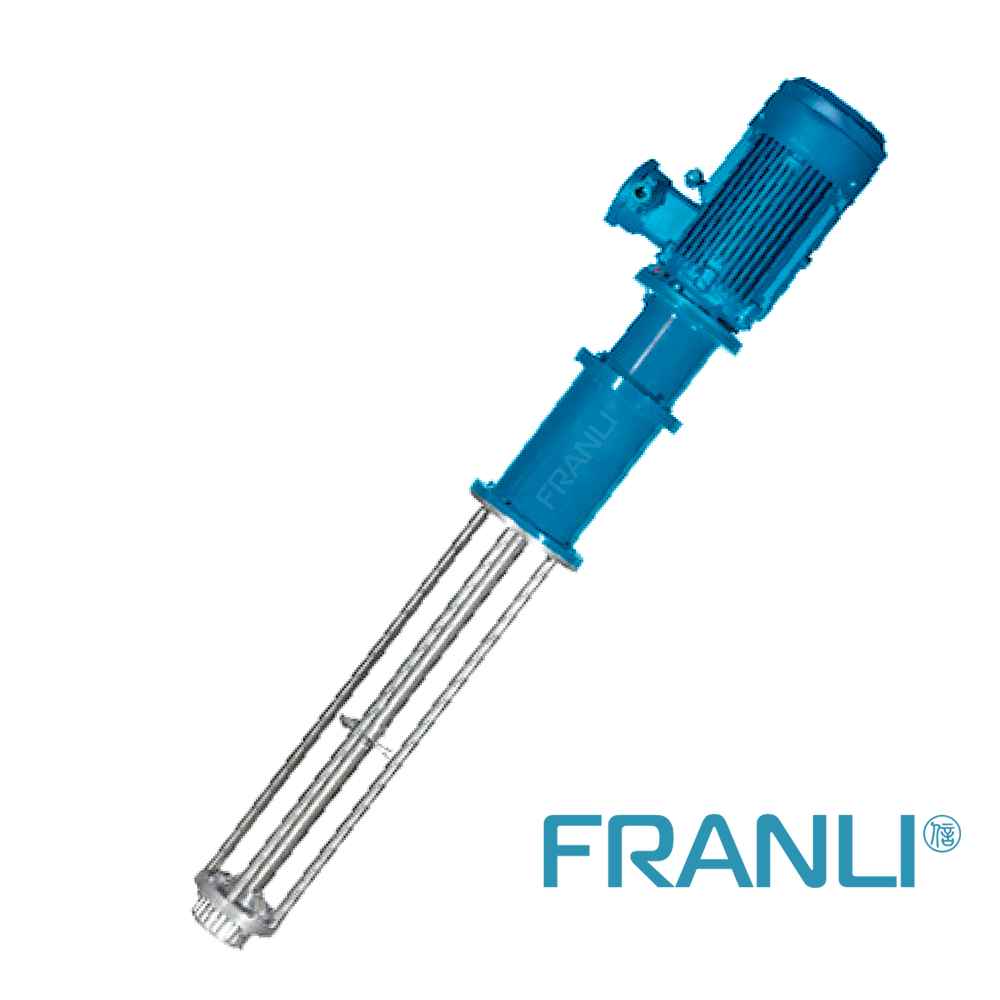
The Difference between High Shear and Low Shear Mixing
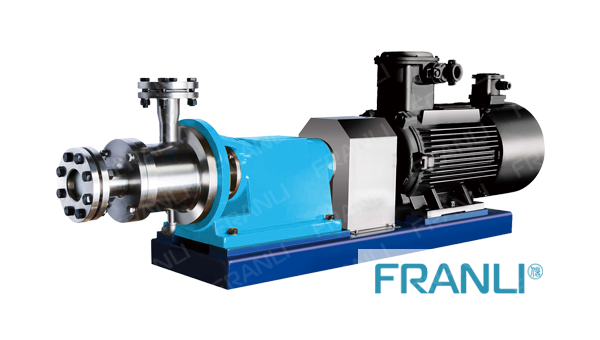
Offering agitation
Related Products
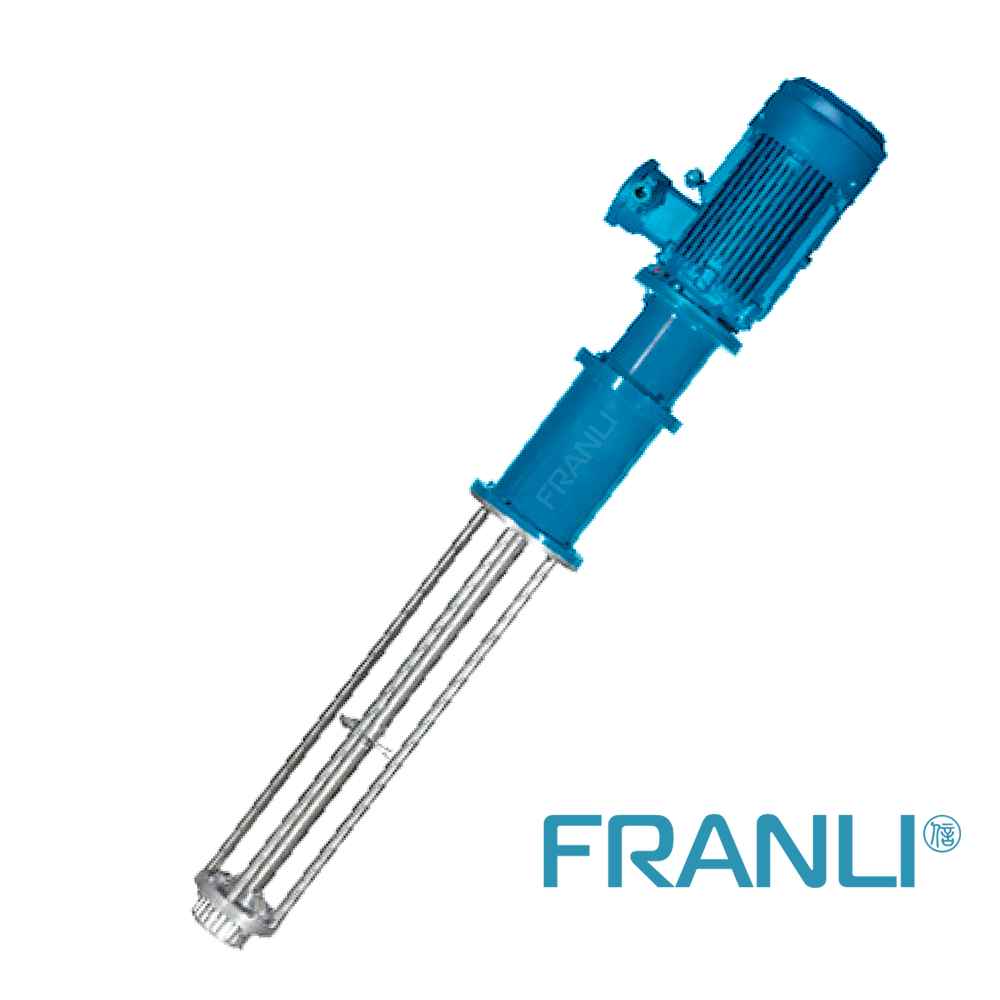
High Shear Emulsifier
The high shear Emulsifier is widely used in the experimental fields of liquid mixing, emulsification, liquid/solid powder dispersion, and slurrying in biology, physics, chemistry, cosmetics, health care products, food, paint, coatings, and chemicals.
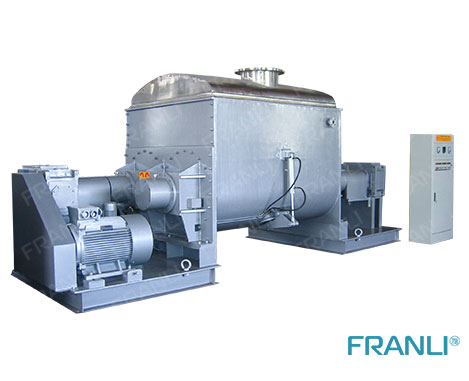
Sigma Mixer Machine
The sigma mixer machine is a device that produces a strong shearing action by a pair of cooperating and rotating blades, so that semi-dry or rubbery viscous plastic materials can be uniformly mixed and stirred.
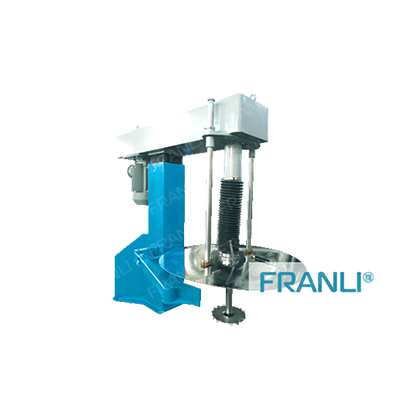
Hydraulic Lifting High Speed Disperser
The hydraulic lift high speed disperser has the characteristics of simple operation and high flexibility. The hydraulic lifting high speed disperser is suitable for the production of paints, inks, coatings, dyes, papermaking, etc.