Home » How to choose a bead mill for ink ?
How to choose a bead mill for ink ?
Bead mill
The common bead mills in chemical grinding equipment are horizontal bead mills, vertical bead mills, basket bead mills, double cone bead mills, nano-level horizontal bead mills, and vertical bead mills.
Details of Bead Mill
- The frame of Bead Mill
- Grinding system of bead mill
- Double mechanical seal of bead mill
- The transmission system of the bead mill
- Grinding cylinder of bead mill
Application: Paint, Adhesive, Battery, Pharmaceutical industry, Cosmetic
Model | Volume(L) | Power(KW) | Beads(mm) |
---|---|---|---|
SMD-0.5 | 0.5 | 4 | 0.3-2.0 |
SMD-30 | 30 | 22-30 | 0.3-2.0 |
SMD-50 | 50 | 30-37 | 0.3-2.0 |
SMD-100 | 100 | 45-55 | 0.4-2.0 |
SMD-300 | 300 | 90-132 | 0.6-2.0 |
SMD-1200 | 1200 | 350 | 0.6-2.0 |
SMD-3000 | 3500 | 560 | 0.6-2.0 |
The bead mill uses ordinary 2-3/3-4mm glass beads, and other equipment uses 0.8-2.4mm zirconia beads. The bead mill is a wet ultrafine grinding equipment, which is developed from the ball mill.
Bead mills are classified in different ways:
1. According to the structure and shape of the stirring shaft, it can be divided into disc type, rod type, and rod type (both bump types).
2. According to the layout of the grinding cylinder, it can be divided into vertical type and horizontal type.
3. According to the volume of the cylinder, it can be divided into laboratory, small, medium, large, and super large.
4. According to the medium separation method, it can be divided into static and dynamic separation bead mills.
5. According to the energy density (installed power per unit volume), it can be divided into low/high energy density bead mills.
To produce different kinds of ink, the structure of the bead mill is also different. The following rules are roughly adhered to:
Gravure ink production generally uses pin rods (5-50 liters) or disc bead mills (10-100 liters).
Rotary offset inks generally use the vertical rod (5-130 liters) or horizontal disc bead mills (60-500 liters), while ultra-high viscosity sheetfed inks are often produced using high energy density conical bead mills or three-stage bead mills. Roller machine.
Inkjet inks (ink and pigment solvent-based) generally use high energy density pin-and-stick (horizontal or vertical) and centrifugal turbine rotors (new patented products).
Compared with grinding equipment such as ball mill, roller mill, and colloid mill, bead mill has the advantages of high production efficiency, strong continuity, low cost, and high product fineness. The process conditions vary greatly, and the fineness requirements can be adjusted and classified by adding or subtracting grinding media in an appropriate amount. Widely used in pigment dispersion and grinding in the ink production process.
The key to the grinding movement of the horizontal bead mill is to realize the cutting movement of the abrasive. Therefore, its movement status will directly affect the processing accuracy and production efficiency of the nano-bead mill. To this end, it is an extremely important step to reasonably select the movement mode and track.
Experience research shows that horizontal bead mill grinding should meet 6 points:
1. The grinding movement of the horizontal bead mill should ensure that the accessories evenly contact the entire surface of the material. In this way, the surface of the nano bead mill can be uniformly loaded and worn evenly, so that the surface accuracy of the horizontal bead mill itself can be maintained for a long time.
2. The grinding movement should ensure that the parts are ground evenly, that is, every point on the surface of the parts being ground is equal. This requires the grinding movement to perform the plane parallel movement, and this movement can make the connection between any two points on the surface of the workpiece remain parallel throughout the grinding movement, which is essential for ensuring the geometric accuracy and dimensional uniformity of the workpiece. for important.
3. The grinding movement should make the movement track change direction regularly and avoid premature repetition. In this way, many cutting streaks on the surface of the workpiece can be regularly intertwined and offset with each other, that is, the more they grind, the smoother they are, and then the purpose of improving the surface accuracy of the workpiece is achieved.
4. The grinding motion should be based on different grinding process requirements, and the best motion speed should be selected specifically. For example, when grinding large-scale workpieces with fineness, low-speed grinding needs to be selected, and when grinding small-scale or low-precision workpieces, medium or high speeds need to be selected.
5. The grinding operation of the entire horizontal bead mill should be stable from beginning to end. Especially for workpieces with a small and slender grinding area, it is necessary to pay attention to making the movement direction change slowly, avoid small bends, and the movement direction should be as close to the long side of the workpiece as possible, and the movement speed should be slowed down. Otherwise, it will cause unevenness of the surface to be researched due to the uneven movement, or the quality defects will be solved by falling edges and corners.
6. During the grinding movement, the relationship between the nano-bead mill and the workpiece should be in an elastic floating state, not a forced limit state. In this way, the workpiece can be in better contact with the surface of the nano-bead mill, and the geometric shape of the surface of the nano-bead mill can be accurately transferred to the workpiece, and then it is not affected by the precision of the grinding machine.
Welcome to send inquiry to us and let’s make a win win business together !
Guidelines For Bead Mill
Bead Mill(sand mill) helps many factories to improve production. Grinding for low viscosity, well-flowing material. Self-cycling cooling system. Don’t need the cooling pump. Franli produces Disc Bead Mill, Pin Bead mill, Turbine Nano Bead mill, etc. Optional material of inner chamber and disc: hardness Alloy, Zirconia, PU.
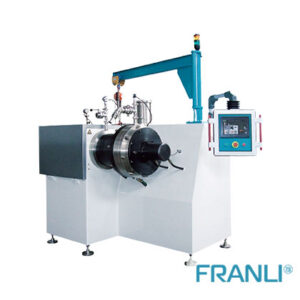
DYNO MILL – A DYNAMIC WAY TO GRIND EASIER
Dyno mill is nothing but an agitator bead mill. It is widely used in the production of paints, coatings, agrochemistry, and pharmaceutical products.
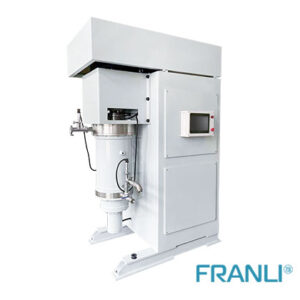
Role of Pearl Mill in the Nano Industry
Pearl Mill can handle both high and low viscosity materials. One is for Nano grinding materials, while the other is for high viscosity materials like offset ink. The operation of the Pearl Mill is straightforward, and all maintenance; may be handled quickly and efficiently. Adding grinding media from the feeding hole is simple.
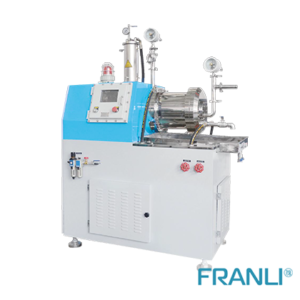
Guide to Bead Mills
The Bead mill is one of the main grindings and dispersing equipment in paint production. Bead mills for coatings are mainly divided into four categories: vertical, horizontal, basket, and special-shaped bead mills.
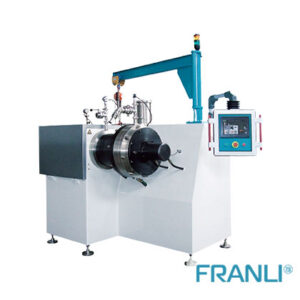
Dyno Mill|Coating & Inks
Dyno mill is a type of bead mill machine which is used in the coating industry specifically, in the manufacturing of inks products.
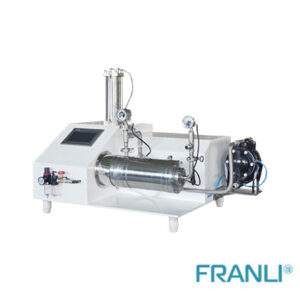
The structure and type of laboratory bead mill
The laboratory bead mill in the chemical experimental equipment, also known as the lab sand mill, is a kind of grinding equipment compared with the bead mill for industrial production.
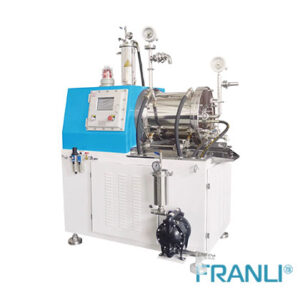
High Viscosity Material Grinding – Bar Pin Bead Mill
The bar pin bead mill is a machine suitable for ultra-fine dispersion and nano-scale grinding of water-based and solvent-based materials. The bar pin bead mill is one of the most widely used production types of equipment. With its very stable performance and sophisticated technology, it has been recognized by a wide range of users. The key thing to know is the characteristics of the bar pin bead mill, which is also the key to people’s favor of it.