Home » High speed disperser|First choice for laboratories
High speed disperser|First choice for laboratories
High Speed Disperser
High speed dispersers have been designed to disperse products at high speeds and high shear. They are excellent for viscous dispersions. High speed dispersers are available in various sizes, including small-scale benchtop units to larger industrial production models that can disperse thousands upon thousands of gallons. High speed disperser is mainly used in paints, inks, coatings, and chemical industries.
Details of High Speed Disperser
- Height limit switch
- Container clamping device
- Speed Automatic
- Vacuum equipment
- Scraper
- Swiveling device
Application: Paint, Adhesive, Battery, Pharmaceutical industry, Cosmetic
High speed disperser is used in many different applications due to its ability to apply high shear and shorten mixing times that require mixing fluids to form emulsions or agglomerated dust to be dispersed into a liquid medium. There is minimal air entertainment. Modern technology has enabled dispersers to generate strong vacuums that allow high powder induction, wetting, and discharge.
The lab managers are always on the lookout for ways to make their lab more efficient. Low funds, a shortage of space and limited time are common complaints of lab managers. A piece of equipment that can do all the work of many is valuable. It is not easy to find the best equipment to produce quality products with the most resourceful and refined process. The high speed disperser has been the most effective machine for mixing modern products for years. There are several problems with the HSD. It traps air and can cause the foam to crack. This makes it more difficult to mix and requires many more additives to remove excess foam. Other properties like stability, agglomerate sizes, color development, droplet size and stability can be problematic. These problems can be alleviated by switching to a rear vortex mixer.
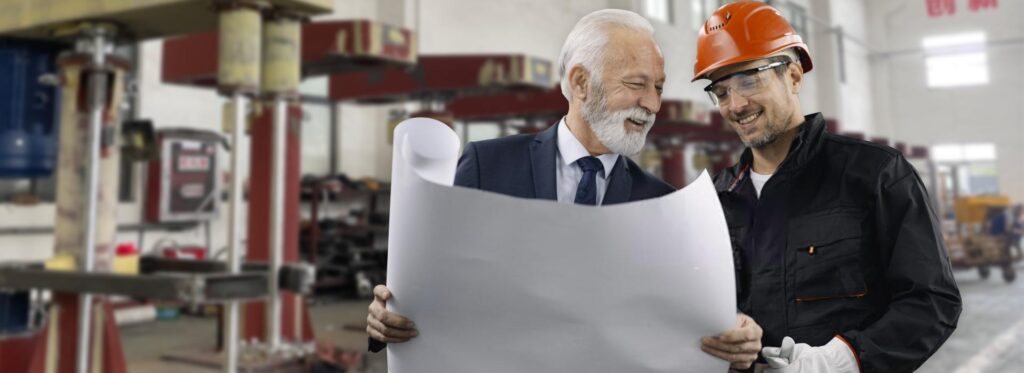
The inverted vortex greatly reduces the surface violence and thus eliminates most of the air entrainment. Manufacturers have discovered that the rotor/stator mixer performs better than the HSD. This allows for lab time and man-hours to be saved while still producing a high-quality product. Mixers with new designs can reduce time and increase productivity. These two key features are the basis of this new design. Agitators are simple to replace. You don’t need any special tools that could complicate the process. Interchangeability is a major advantage. It reduces the risk of damage to bearings shafts seals. Production time is greatly reduced by the quick interchange.
A push-button high-speed disperser is another development that saves time. You can change speeds faster and safer. Digital readouts improve the accuracy of the machine and allow lab technicians to fine-tune the process.
A lab must carefully examine several factors when considering upscaling. It would help if you considered both the shaft speed and the speed at which the agitator is moving. It would help if you considered the size and volume of the vessel, as well its ability to handle partial batches, as well as its capacity to do full batches. It would help if you also planned for the volume and turnover of each batch. Before changing from the high speed disperser mixers to newer models, managers must consider the available horsepower, heat sensitivity and viscosity. Many people have found that they can be used alongside the HSD to increase production and not replace them.
Industries will reap the benefits of high-speed dispersers. high speed disperser can produce in-line concentrations as high as 40% by weight in a single process. Powder incorporation is possible, and batch time can be saved. Concentrated single-pass powder dispersions can be dispersed at high speeds, reducing dispersion times by as much as 90%. You can see a significant improvement in inconsistency in the processed product. The reproducible dispersion characteristics are consistent from batch to batch. High-speed dispersers with innovative high tech ‘ZC’s’ powder-dispersion tooling/reactor head allow for intense shearing of powders in one pass before they are hydrated. This allows for uniform dispersions without lumps. A perfect vacuum is created to allow powder dispersion to be achieved in one pass. It can achieve in-line concentrations as high as 25% by weight with minimal air entrainment. The powder is completely hydrated, which results in a higher product yield.
Key benefits of high-speed dispersers:
❖ Dramatic Powder Incorporation & Batch Time Savings
❖ Eliminate over-processing by conventional dispersing technologies
❖ Protect the rheological characteristics of the shear sensitive products, which can also result in powder ingredient savings
Companies need to develop faster technologies to keep up with the current-day mass production of industrial, pharmaceutical and consumer goods. The mixing process is both an art form and science to the processing industry. This requires both innovative technological approaches and extensive experience in the “art” of mixing. Companies that need to dispense drugs, paints, chemicals, inks, adhesives, or other products, use high speed dispersion as their main tool. A product with the correct particle size give you excellent product performance. This is also a benefit for overall process optimization. It is a smart business move to make use of the most recent innovations in dispersers.
Every aspect of processing is under constant scrutiny. Engineers, scientists and technicians all work together to improve the mixing process. The aim is to reduce processing costs and speed up the process.
Mixing surfactants requires a scientific approach. The final product must serve its purpose. To achieve a functional surfactant, you need to have the right balance between absorption and particles. These mixing methods are widely used by the petroleum industry as well as the pharmaceutical and food industries. To achieve the best result, it takes much experimentation. The ratio of stability to droplet size is generally proportional. This can only happen after many tests and trials have been conducted. It takes effort and dedication to run batch after batch of samples through many types of mixers to find the right one. There are many high speed dispersion and tips for rotators. Also, there are different water pressures. This allows you to get the perfect combination for particle size distributions.
The use of a high speed dispersion mixer yielded consistent results. The principle of high shear mixers is to create hydraulic and mechanical shear. The franli use continuous motion to pull product pieces into the rotor, while circular motion moves them out through a stator.
Welcome to send inquiry to us and let’s make a win win business together !
Guidelines For High Speed DIsperser
We produce a high-speed disperser according to the industrial standard, Franli HSD’s frame is bigger than the marketing machine, the blade is double layers, hydraulic part is an engineering oil tank, which is more stable lifting up and down. The operation box for Water-based material is stainless steel, which also has ex-proof operation for solvent based material.
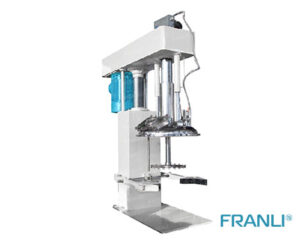
A High Speed Disperser & Efficient Mixing and Dispersion
A high speed disperser is a type of industrial equipment used for mixing and dispersing materials that are used to disperse, emulsify, and blend different types of materials.
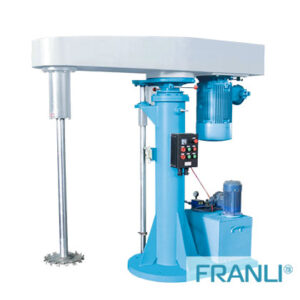
High Speed Disperser: An Essential Tool in the Manufacturing Industry
A high speed disperser is a machine used for dispersing, mixing, emulsifying, and homogenizing materials in the manufacturing process.It is also called a high-speed mixer or agitator, and its versatility makes it a valuable tool in various industries, including coatings, paints, inks, adhesives, pharmaceuticals, food, and cosmetics.
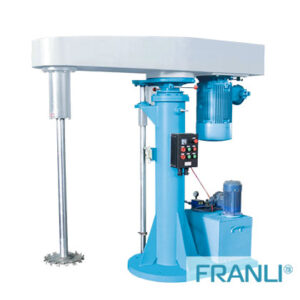
The high speed disperser chosen by the chemical industry
The high speed disperser is the indispensable equipment in the production and dispersion process of chemical products. Because of its high speed, it can not only effectively improve the dispersion efficiency of materials, but also make the materials more fully dispersed, to meet the final requirements of the materials.
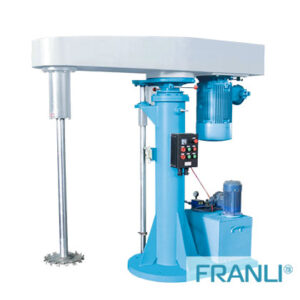
How to choose a suitable high-speed disperser for coatings?
A high speed paint disperser is one of the chemical equipment for stirring, dispersing, and dissolving paint raw materials, slurry, and paint mixture.
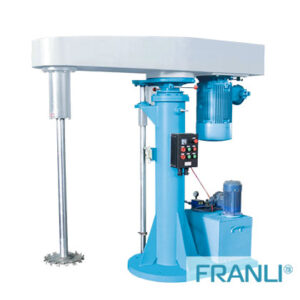
How to use the high speed disperser (new machine)?
The high speed disperser is composed of a frame, a bearing seat, a dispersing shaft, a dispersing wheel, an oil cylinder, a hydraulic station, and a control cabinet. The lifting of the frame adopts hydraulic transmission, and the lifting is stable and reliable.
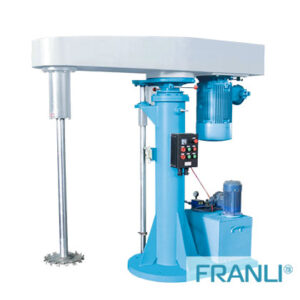
High speed disperser: dispersing, stirring, grinding, dissolving
High speed disperser is common mechanical equipment in chemical production. It is widely used in architectural coatings, chemicals, water-based coatings, oil-soluble architectural coatings, inks, inks, adhesives, etc.