Home » Reasons for the popularity of high shear mixers
Reasons for the popularity of high shear mixers
Mixing the various components that can help to achieve the suitable foods, topical creams, lotions, cosmetics, etc., can all be achieved with the use of high shear mixer and technology as primitive as the mortar and pestle to note this technically. High shear mixers offer the kind of mixing that can only be achieved with the use of this for the highly homogenized and often emulsified products here. The high shear mixer is capable of dispersing the powdered solids into their highly viscous liquids, thereby emulsifying the other immiscible liquid and other disparate substances.
Over the specific set of competing mixing technologies, the best of the high shear disperser offers the most distinctive set of advantages here that would be ranging over the specific competing mixing technologies present.
The technology of high shear mixing is sure to offer a wide range of benefits for numerous products across a massive range of industries here. Without this kind of technology, which would be facilitating the main tasks including efficient powder dispersion, emulsification, submicron homogenization, deagglomeration, wet milling, etc. are sure would make the manufacture of the products here is extremely difficult.
Benefits you can derive through the high shear mixer.
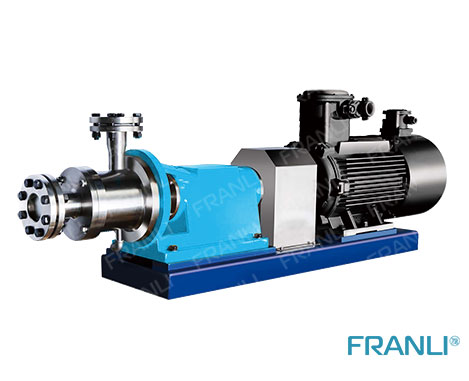
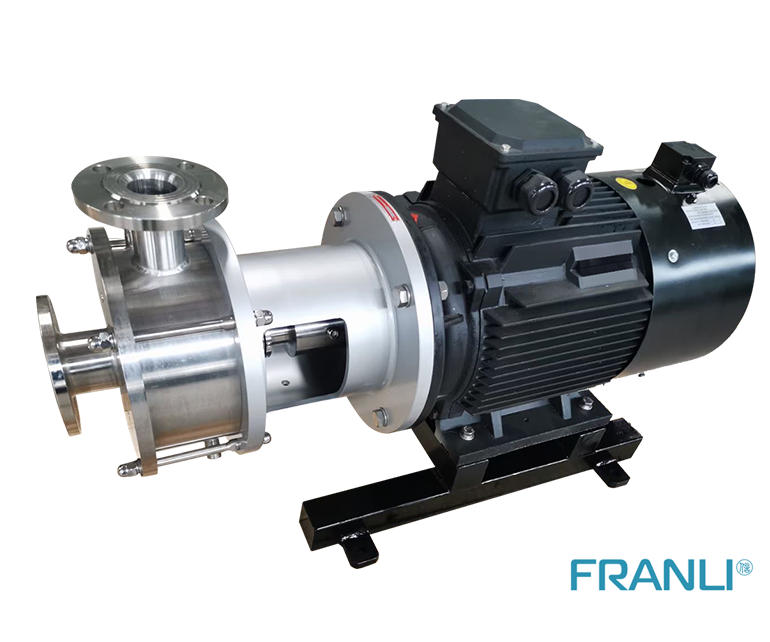
Inline Saves Time and Money
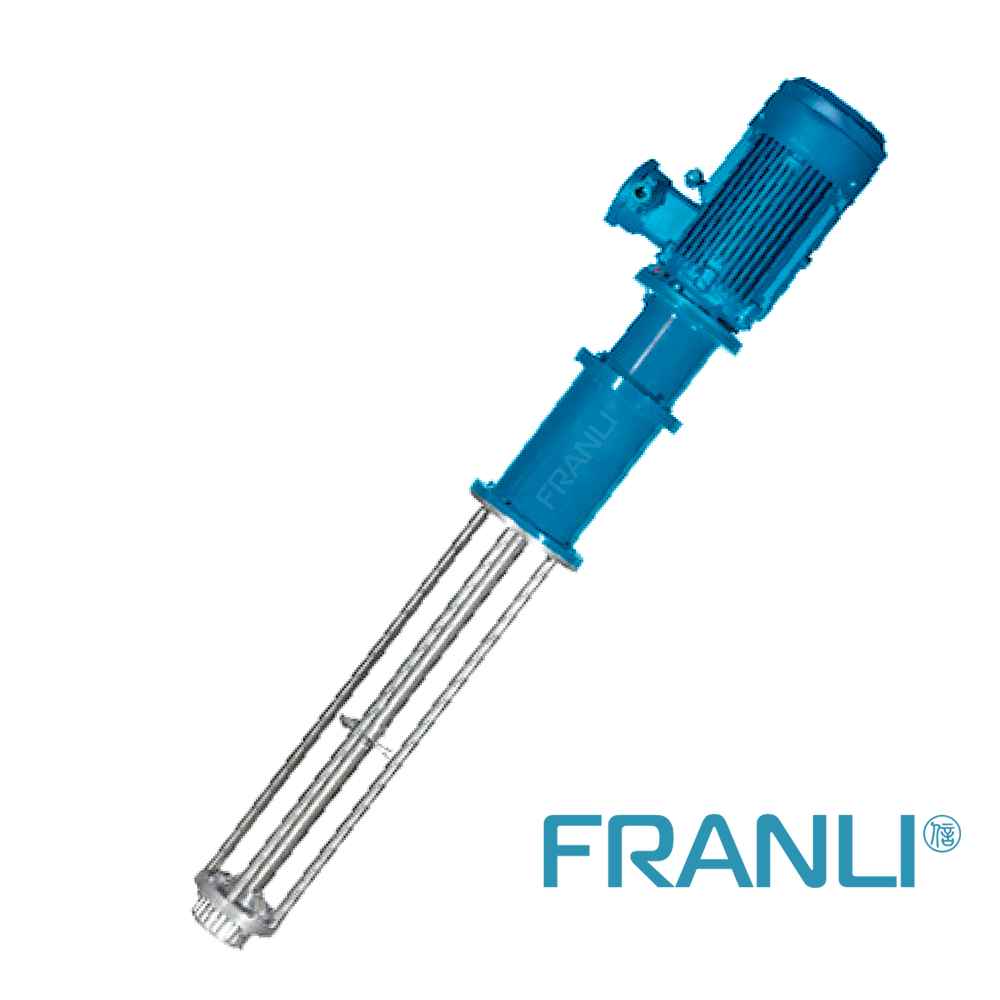
The Difference between High Shear and Low Shear Mixing
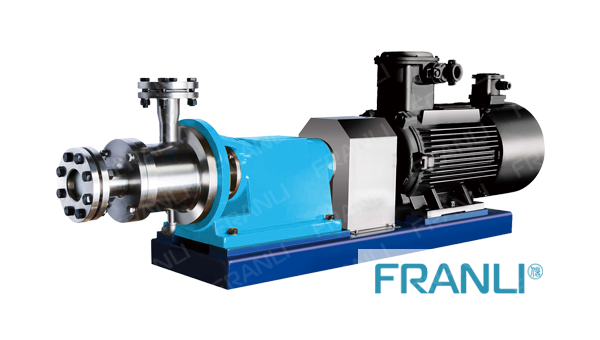
Offering agitation
Related Products
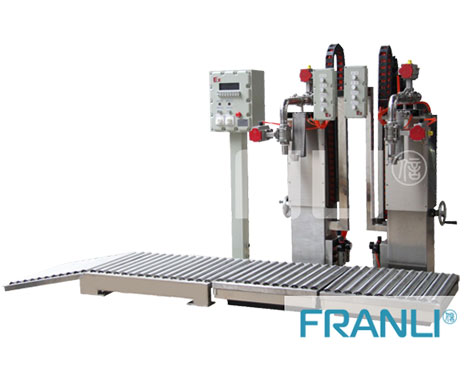
Drum Filling Machine
Drum filling machine is widely used in paint and ink industries. The drum has two kinds of material, plastic or metal. And there are many types of drums
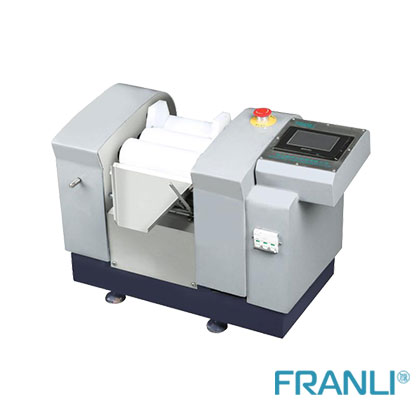
Three roll mill
Three roll mills are widely used in a variety of chemical industries, from medium to high viscosity productions. FRANLI machine can break open all kinds of pigment, UV ink, offset ink, decorative paints, and Lubricants, it also can catch the greatest fine
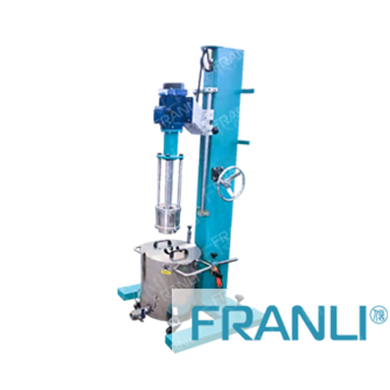
Lab Basket Mill
The lab basket mill is a common equipment for small-scale experiments and scientific research. Suitable for wet grinding of medium and low viscosity materials. It integrates dispersion, grinding, and integration.