Home » Instructions For Use Of the Kneader
Instructions For Use Of the Kneader
Kneader
Details of Kneader
- The machine comprises a motor, cover press, main body, mixing chamber and rotor mechanism, gearbox, air control system, tilting machine, heating/cooling system, rubber belt transmission and base, etc.
- The kneader can be made into vacuum, pressure, atmospheric, Normal temperature, high temperature, low temperature, etc.
- The temperature adjustment method of a kneader can be the jacket, halfpipe, far-infrared tile, steam, hot water, heat transfer oil, electric heating, cooling water, chilled water, and other methods.
Application: Paint, Adhesive, Battery, Pharmaceutical industry, Cosmetic
The kneader can be designed in the form of heating and non-heating according to the needs. The heating methods usually include electric heating, steam heating, circulating hot oil heating, and electric heating. Cooling methods include circulating water cooling, circulating oil cooling, etc.
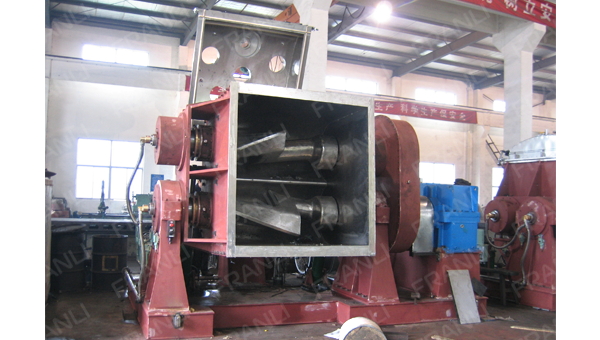
The composition of the kneader
1. The kneader has two Z-shaped blades. The speeds of the two blades are different. Different speeds can be set according to different processes. The common speed is 42/28 rpm. turn or reverse.
2. The machine base and support part; in terms of material, the cylinder block and the contact part between the paddle and the material are made of SUS304 stainless steel to ensure product quality.
3. Hydraulic system: The hydraulic system uses a hydraulic station to operate the large oil cylinder to complete functions such as turning the cylinder and opening the cover. The detailed parameters can be arbitrarily selected and required by the user, and the operation is convenient and reliable.
4. The transmission system consists of a motor, a reducer, and a gear, and the motor is matched according to the model of the kneader. The transmission part of the kneader is synchronously rotated by the motor. After the elastic coupling reaches the reducer, the fast pulp is driven by the output device to make it reach the specified speed, and the speed can also be adjusted by the frequency converter.
5. Electric control system: Usually, the kneader is equipped with a common control cabinet. If the customer’s material has special requirements and needs to work under explosion-proof conditions, the control cabinet can be used in isolation. If the viscosity of the material is too high, an auto-decompression starter can be used.
Common sense of use and maintenance of kneader
1. Installation and debugging of the kneader
The foundation should be poured before the kneader is installed, the pre-embedded holes should be poured according to the requirements of the installation foundation diagram, and the equipment should be poured together after the equipment is in place. The machine is an integral structure, the level must be corrected, and the anchor bolts must be tightened after adjustment is appropriate. The steam pipeline, electrical pipeline, and working space shall be arranged by the user as a whole.
2. Commissioning of the kneader and preparation before operation
(1) After the machine is installed, first clean, decontaminate and wipe the anti-rust grease. Check each lubrication point and inject lubricating oil (grease).
(2) Check the tension of the V-belt before driving, and move the motor to the proper position by adjusting the bolt.
(3) Check whether the fasteners are loose, whether the steam pipeline leaks, and whether the circuit and electrical equipment are safe. The electric heating type kneader must have a grounding device.
(4) Clean up the kneading chamber before the test run, run it for 10-15 minutes, and then put it into production after confirming that the machine is running normally. Usually, the noise of the new gear (including the reducer) is relatively loud in the initial use, and will naturally decrease after a period of running-in.
(5) When using steam for heating, a safety valve and a pressure gauge should be installed at the inlet pipe, and the steam pressure should not exceed the operating pressure requirements of the mixing tank according to the knowledge of the sign.
(6) The use of inversion should be reduced when mixing and kneading.
3. Repair and maintenance
(1) All lubricating parts should be filled with oil frequently.
(2) There should be no leakage of raw materials in the sealing part of the wall panel.
(3) The tightness of the belt is appropriate, and it should be checked, adjusted, or replaced regularly.
(4) The steam pipeline is not allowed to leak, the valve should be closed when the machine is stopped, and the reliability of the pressure gauge of the safety valve should be checked.
(5) The machine should be overhauled after six months of operation, check the degree of damage, and make release adjustments and replacements.
Welcome to send inquiry to us and let’s make a win win business together !
Guidelines For Kneader
The dispersion kneader is suited for rubber and plastic mastication, as well as the blending of different rubber and plastic components. Small and medium-sized rubber and plastics manufacturers with a wide range of product types and colours, as well as food, dyes, pharmaceuticals, and ceramics, can benefit from the internal mixer.
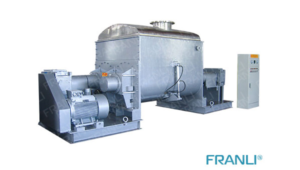
Sigma Kneader: The Solution for Mixing and Kneading
Sigma kneader is a versatile machine that can be used for mixing, kneading, and homogenizing a wide range of materials, including high-viscosity products.
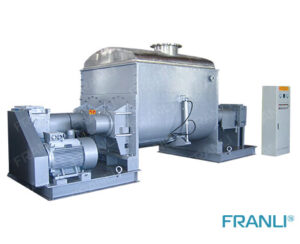
Sigma Mixer: Indispensable Equipment For Manufacturing
Sigma Mixer is a type of mixer that uses a unique mixing principle to achieve an efficient blending of materials. The mixer consists of two blades that rotate in opposite directions, creating a kneading and folding action that ensures thorough mixing. The blades are shaped like the Greek letter Sigma, hence the name Sigma Mixer.
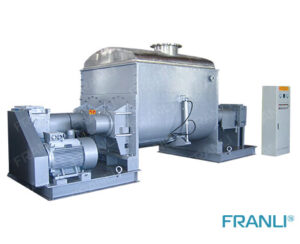
Sigma Blade Mixer: The Mixing Solution
The Sigma Blade Mixer is a robust and reliable mixing machine that uses a unique mixing principle to achieve superior results. It is a type of double-arm kneading mixer that features two blades that rotate in opposite directions.
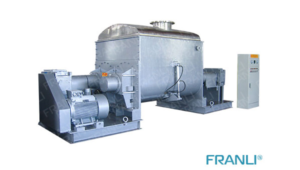
Vacuum Kneader: A Machine for Your Mixing Needs
The Vacuum Kneader is a type of mixer that utilizes a vacuum chamber to create a homogeneous mix of ingredients. It is designed to knead, mix, and disperse high-viscosity materials under vacuum conditions, resulting in a superior product.
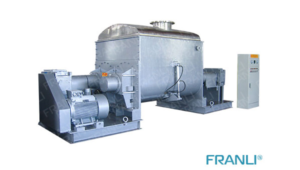
Efficiency and Effectiveness of Dispersion Kneader
The dispersion kneader has complete control over the mixing and blending of the raw materials to create an even mix that allows for better distribution. This device contains a mixing chamber with rotating blades made of high-quality steel.
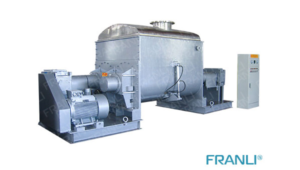
Vacuum kneader: high efficiency and environmental protection
A vacuum kneader is mainly used for stirring, mixing, and kneading high-viscosity and elastic-plastic materials. The most common fields include high-viscosity sealant, silicone rubber, neutral acid glass glue, chewing gum, bubble gum, aluminum silver paste, silica gel, paper pulp, cellulose, and other materials. It covers food, agrochemical, pharmaceutical, cosmetics, electronic paste, and other industries, and has been sought after by the industry.