Home » High Speed Dispersers: A Powerful Tool
High Speed Dispersers: A Powerful Tool
High Speed Disperser
A high-speed disperser, also known as a high-shear mixer or dissolver, is a specialized piece of equipment designed to introduce intense shear forces into a mixture, effectively breaking down agglomerates and dispersing particles uniformly throughout the medium. These machines are characterized by their ability to operate at high rotational speeds, typically ranging from several thousand to tens of thousands of revolutions per minute (RPM).
Details of High Speed Disperser
- Height limit switch
- Container clamping device
- Speed Automatic
- Vacuum equipment
- Scraper
- Swiveling device
Application: Paint, Adhesive, Battery, Pharmaceutical industry, Cosmetic
Enter the high-speed disperser, a versatile and powerful tool that has revolutionized the way we approach mixing and dispersion challenges. From the production of paints and coatings to the formulation of pharmaceuticals and cosmetics, achieving a homogeneous blend of ingredients is crucial for ensuring consistent product quality and performance.
At the heart of a high-speed disperser lies a robust shaft with a specially designed blade or rotor attached to its end. As the shaft rotates at high speeds, the blade generates powerful shear forces that tear apart agglomerates and disperse particles, ensuring a homogeneous and stable mixture.
Principles of Operation
The operating principle of a high-speed disperser revolves around the generation of intense shear forces through the rapid rotation of the dispersing blade or rotor. These shear forces are responsible for breaking down agglomerates and dispersing particles within the mixing medium. The key mechanisms involved in this process include:
1. Mechanical Shear: The high-speed rotation of the dispersing blade creates mechanical shear forces that physically break apart agglomerates and disperse particles. This shearing action is particularly effective for solid-liquid and solid-solid dispersions.
2. Hydraulic Shear: As the dispersing blade rotates, it creates turbulence and high-velocity flow patterns within the mixing medium. This hydraulic shear contributes to the dispersion of particles by subjecting them to intense shear stresses and collisions.
3. Cavitation: In certain cases, the high-speed rotation of the dispersing blade can induce cavitation, which involves the formation and subsequent collapse of microscopic bubbles within the liquid medium. The implosion of these bubbles generates localized high-pressure zones that further aid in the dispersion process.
4. Centrifugal Force: The rapid rotation of the dispersing blade also generates centrifugal forces that drive the mixture towards the walls of the mixing vessel, promoting efficient circulation and ensuring thorough mixing and dispersion.
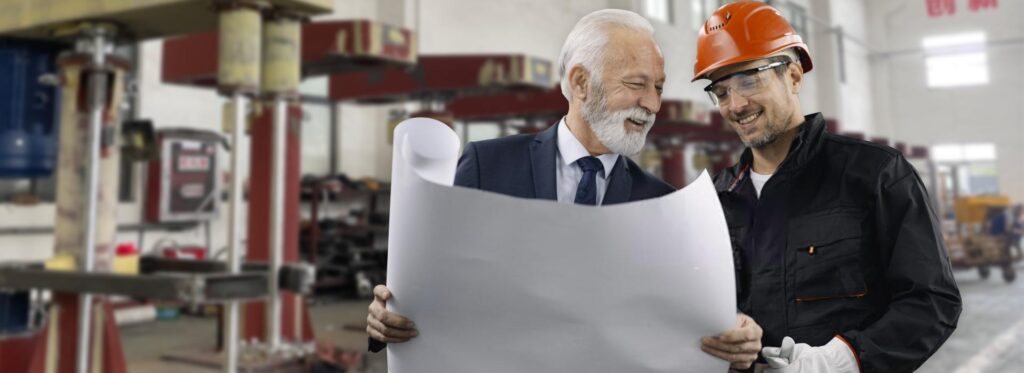
Applications and Industries
High-speed dispersers find applications across a wide range of industries, where efficient mixing and dispersion are critical for product quality and performance. Some of the key applications and industries that rely on high-speed dispersers include:
1. Paints and Coatings: High-speed dispersers are essential in the production of paints, coatings, and inks, where they are used to disperse pigments, resins, and other additives into the liquid medium, ensuring uniform color and consistent performance.
2. Pharmaceuticals: In the pharmaceutical industry, high-speed dispersers are employed in the formulation of various drug products, including suspensions, emulsions, and ointments, ensuring uniform distribution of active ingredients and excipients.
3. Cosmetics and Personal Care: The cosmetics and personal care industry relies on high-speed dispersers for the production of creams, lotions, and other personal care products, ensuring consistent texture, appearance, and performance.
4. Food and Beverage: High-speed dispersers are used in the food and beverage industry for the production of emulsions, suspensions, and other dispersed systems, such as salad dressings, sauces, and flavored beverages.
5. Adhesives and Sealants: The adhesives and sealants industry utilizes high-speed dispersers for the dispersion of fillers, pigments, and other additives, ensuring consistent performance and adhesion properties.
6. Ceramics and Composites: In the ceramics and composites industry, high-speed dispersers are employed for the dispersion of ceramic powders, fibers, and other reinforcing materials, enabling the production of high-performance composite materials.
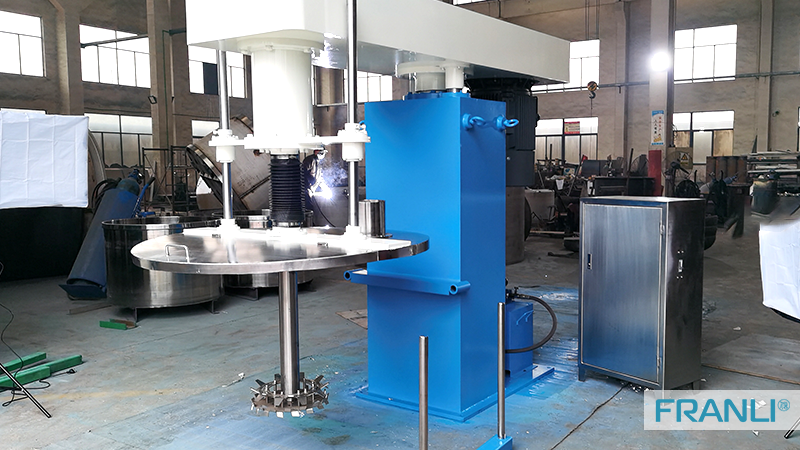
Key Features and Considerations
When selecting and operating a high-speed disperser, several key features and considerations must be taken into account to ensure optimal performance and efficiency:
1. Speed and Shear Rate: The speed of the dispersing blade is a critical factor that determines the shear rate and intensity of the dispersion process. Higher speeds generally result in greater shear forces and more efficient dispersion, but excessive speeds can also lead to overheating and potential product degradation.
2. Blade Design: The design of the dispersing blade plays a crucial role in the effectiveness of the dispersion process. Different blade geometries and configurations are available to cater to specific applications and material properties, such as viscosity, particle size, and desired dispersion level.
3. Batch Size and Vessel Geometry: The batch size and geometry of the mixing vessel can significantly impact the efficiency of the dispersion process. Proper sizing and selection of the disperser and vessel are essential to ensure optimal mixing and dispersion.
4. Temperature Control: Many high-speed dispersers are equipped with temperature control systems, such as jacketed vessels or cooling coils, to manage the heat generated during the dispersion process. Temperature control is crucial for temperature-sensitive materials and to prevent product degradation.
5. Automation and Process Control: Modern high-speed dispersers often feature advanced automation and process control capabilities, allowing for precise control of parameters such as speed, temperature, and mixing time. This ensures consistent and repeatable results across production batches.
6. Safety Considerations: High-speed dispersers operate at high rotational speeds, which can pose safety risks if not properly handled. Appropriate safety measures, such as guarding, interlocks, and operator training, are essential to ensure safe operation and prevent accidents.
The field of high-speed dispersers is continuously evolving, driven by technological advancements and the ever-increasing demand for efficient and effective mixing and dispersion solutions. Some of the emerging trends and future developments in this area include:
1. Intelligent Process Control: The integration of advanced sensors, data analytics, and machine learning algorithms is enabling more intelligent process control and optimization of high-speed dispersers. These technologies can help monitor and adjust process parameters in real time, ensuring consistent product quality and maximizing efficiency.
2. Scalable and Modular Designs: Manufacturers are developing scalable and modular high-speed disperser designs that can be easily adapted to different production scales and batch sizes, providing flexibility and cost-effectiveness for various applications.
3. Specialized Blade Designs: Ongoing research and development efforts are focused on designing specialized blade geometries and configurations tailored to specific applications and material properties, further enhancing the efficiency and effectiveness of the dispersion process.
4. Sustainable and Energy-Efficient Solutions: With increasing emphasis on sustainability and energy efficiency, manufacturers are exploring ways to optimize the energy consumption of high-speed dispersers while maintaining or improving their performance.
5. Integration with Automation and Industry 4.0: The integration of high-speed dispersers with advanced automation systems and Industry 4.0 technologies, such as the Internet of Things (IoT) and cloud computing, enables remote monitoring, predictive maintenance, and seamless integration with other manufacturing processes.
Welcome to send inquiry to us and let’s make a win win business together !
Guidelines For High Speed DIsperser
We produce a high-speed disperser according to the industrial standard, Franli HSD’s frame is bigger than the marketing machine, the blade is double layers, hydraulic part is an engineering oil tank, which is more stable lifting up and down. The operation box for Water-based material is stainless steel, which also has ex-proof operation for solvent based material.
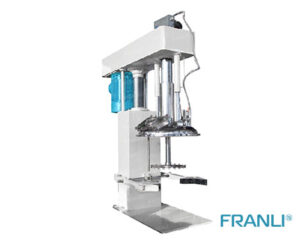
A High Speed Disperser & Efficient Mixing and Dispersion
A high speed disperser is a type of industrial equipment used for mixing and dispersing materials that are used to disperse, emulsify, and blend different types of materials.
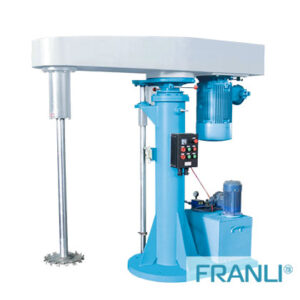
High Speed Disperser: An Essential Tool in the Manufacturing Industry
A high speed disperser is a machine used for dispersing, mixing, emulsifying, and homogenizing materials in the manufacturing process.It is also called a high-speed mixer or agitator, and its versatility makes it a valuable tool in various industries, including coatings, paints, inks, adhesives, pharmaceuticals, food, and cosmetics.
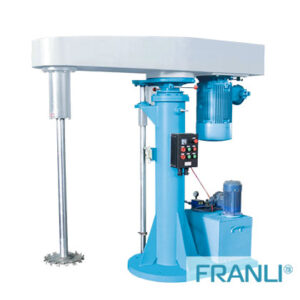
The high speed disperser chosen by the chemical industry
The high speed disperser is the indispensable equipment in the production and dispersion process of chemical products. Because of its high speed, it can not only effectively improve the dispersion efficiency of materials, but also make the materials more fully dispersed, to meet the final requirements of the materials.
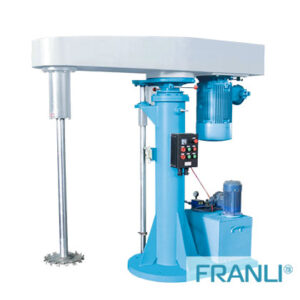
How to choose a suitable high-speed disperser for coatings?
A high speed paint disperser is one of the chemical equipment for stirring, dispersing, and dissolving paint raw materials, slurry, and paint mixture.
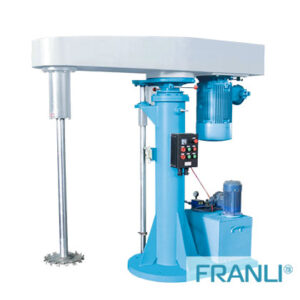
How to use the high speed disperser (new machine)?
The high speed disperser is composed of a frame, a bearing seat, a dispersing shaft, a dispersing wheel, an oil cylinder, a hydraulic station, and a control cabinet. The lifting of the frame adopts hydraulic transmission, and the lifting is stable and reliable.
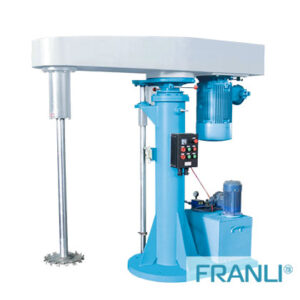
High speed disperser: dispersing, stirring, grinding, dissolving
High speed disperser is common mechanical equipment in chemical production. It is widely used in architectural coatings, chemicals, water-based coatings, oil-soluble architectural coatings, inks, inks, adhesives, etc.