Home » What is a Vacuum Disperser?
What is a Vacuum Disperser?
Vacuum Disperser
The high-speed impeller, driven by the motorized system, generates a streamlined fluid flow, ensuring efficient mixing and dispersion. Simultaneously, the vacuum chamber helps eliminate air bubbles, promote degassing, and enhance product stability. With the combination of vacuum and high-speed mixing, vacuum dispersers offer exciting possibilities and advancements in the field of manufacturing.
Details of Vacuum Disperser
- Height limit switch
- Container clamping device
- Speed Automatic
- Vacuum equipment
- Scraper
- Swiveling device
Application: Paint, Adhesive, Battery, Pharmaceutical industry, Cosmetic
In the realm of chemical, pharmaceutical, and food manufacturing, ensuring the perfect mix and homogenization of ingredients is of utmost importance. Achieving uniform dispersion and breakdown of particles can greatly influence the quality, stability, and effectiveness of a final product. One innovative tool that has gained prominence for its exceptional mixing capabilities is the vacuum disperser.
To comprehend the significance of vacuum dispersers, it is crucial to understand the basic principle behind them. A vacuum disperser operates under the principle of utilizing pressure differentials to facilitate effective mixing and dispersion. At its core, the apparatus consists of a mixing vessel, a high-speed impeller, a vacuum chamber, and a robust drive system.
Applications of Vacuum Dispersers
1. Chemical Industry: Vacuum dispersers have a significant impact on the chemical industry, revolutionizing the mixing and dispersion processes for various chemical compounds. Their application ranges from dispersing pigments, dyes, and nanoparticles to achieving uniform particle size reduction, even in high-viscosity mixtures. This technology greatly aids in producing high-quality paints, coatings, inks, and adhesives.
2. Pharmaceuticals: The pharmaceutical industry relies on precision and uniformity in drug manufacturing to ensure safety and efficacy. Vacuum dispersers prove invaluable in creating stable emulsions, suspensions, and solutions. They enable the homogenization of active pharmaceutical ingredients (APIs), allowing for even distribution within the final product, leading to increased bioavailability and consistent dosages.
3. Food Manufacturing: Vacuum dispersers play a significant role in the food industry, aiding in the production of various food products such as sauces, dressings, mayonnaise, and beverages. Whether it’s dispersing powders or achieving emulsions, vacuum dispersers help obtain a smooth texture, consistent viscosity, and improved taste while maintaining product stability.
4. Cosmetics and Personal Care: Vacuum dispersers have found their place in the cosmetic industry for their ability to disperse powders, pigments, and oils uniformly. They facilitate the production of high-quality creams, lotions, and make-up products, ensuring the desired consistency, color, and texture while enhancing product performance.
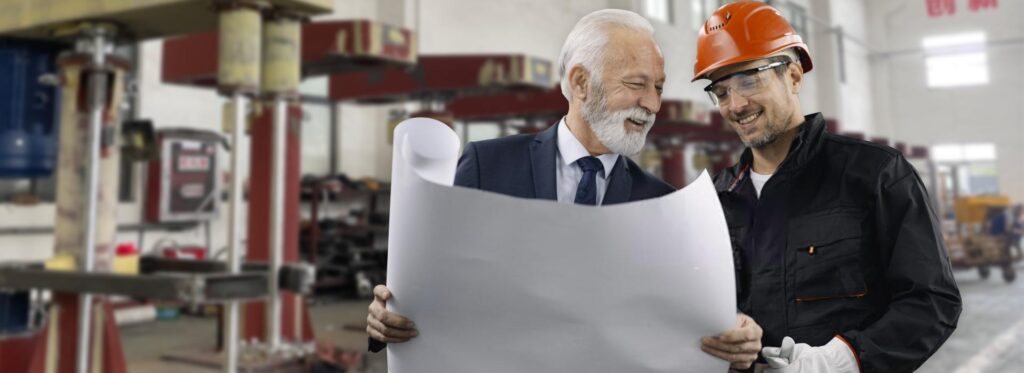
Benefits of vacuum disperser
1. Enhanced Mixing Efficiency: Vacuum dispersers offer superior mixing efficiency, thanks to high-speed impellers and vacuum degassing capabilities. They result in faster mixing times, reduced process steps, and improved dispersion of particles.
2. Improved Product Quality: The uniform dispersion achieved by vacuum dispersers leads to improved product quality, stability, and shelf life. They eliminate the risk of clumping, settling, or inconsistent concentrations, ensuring a homogeneous end product.
3. Increased Productivity: By streamlining the mixing process, vacuum dispersers contribute to increased productivity, reducing batch times and minimizing manual intervention.
4. Versatility: Vacuum dispersers are versatile in accommodating various viscosities and ingredient combinations. They can handle both small and large-scale productions while allowing precise control over mixing parameters.
5. Automated Operation: Many vacuum dispersers are equipped with automated control systems, enabling precise monitoring and adjustment of mixing parameters, saving time, and ensuring consistency.
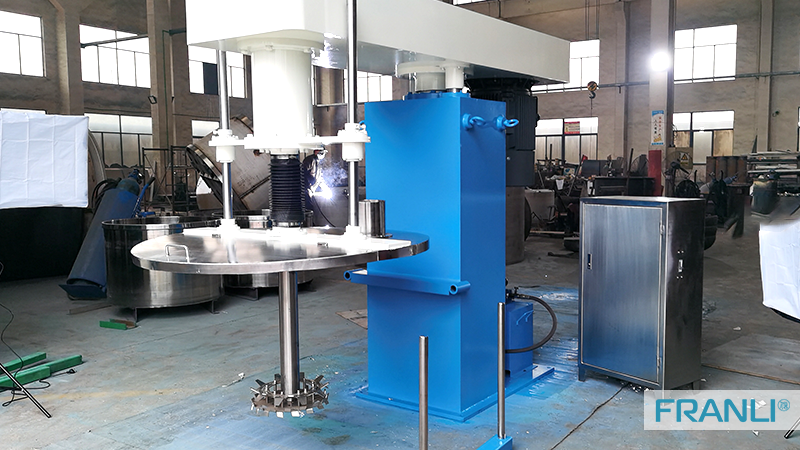
Limitations of vacuum disperser
1. Cost: Vacuum dispersers, depending on their size and complexity, can be expensive investments. However, their long-term benefits often surpass the initial costs for industries that frequently require precise mixing and dispersion.
2. Maintenance: Like any mechanical equipment, vacuum dispersers require regular maintenance to ensure optimal performance. Maintenance schedules and costs should be considered when incorporating these systems into production lines.
3. Specific Application Requirements: Certain applications, such as working with highly hazardous or reactive materials, may require advanced engineering and additional safety measures to ensure operator and product safety.
Vacuum dispersers have transformed the manufacturing landscape, offering enhanced mixing capabilities, improved product quality, and increased productivity across multiple industries. These versatile tools have become indispensable in chemical, pharmaceutical, food manufacturing, and cosmetic industries, where uniformity and quality are paramount.
The consistent dispersion achieved by vacuum dispersers ensures optimal performance, stability, and bioavailability of final products. Despite their initial costs and maintenance requirements, vacuum dispersers are cost-effective solutions that streamline production processes and deliver outstanding results.
As technology continues to advance, vacuum dispersers are likely to evolve further, catering to the ever-increasing demands of mixing and homogenization. With innovations in automation and control systems, these devices will continue to be at the forefront of facilitating efficient manufacturing processes in various industries.
Welcome to send inquiry to us and let’s make a win win business together !
Guidelines For High Speed DIsperser
We produce a high-speed disperser according to the industrial standard, Franli HSD’s frame is bigger than the marketing machine, the blade is double layers, hydraulic part is an engineering oil tank, which is more stable lifting up and down. The operation box for Water-based material is stainless steel, which also has ex-proof operation for solvent based material.
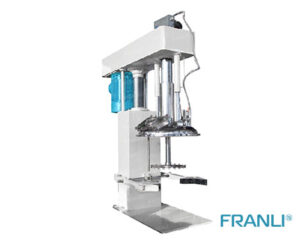
A High Speed Disperser & Efficient Mixing and Dispersion
A high speed disperser is a type of industrial equipment used for mixing and dispersing materials that are used to disperse, emulsify, and blend different types of materials.
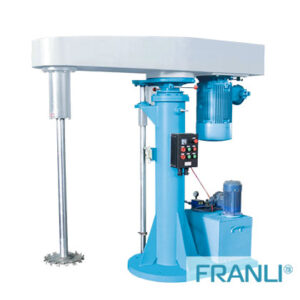
High Speed Disperser: An Essential Tool in the Manufacturing Industry
A high speed disperser is a machine used for dispersing, mixing, emulsifying, and homogenizing materials in the manufacturing process.It is also called a high-speed mixer or agitator, and its versatility makes it a valuable tool in various industries, including coatings, paints, inks, adhesives, pharmaceuticals, food, and cosmetics.
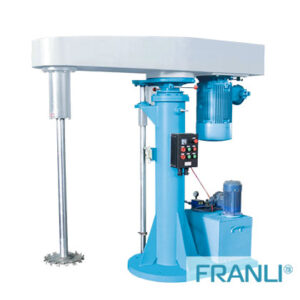
The high speed disperser chosen by the chemical industry
The high speed disperser is the indispensable equipment in the production and dispersion process of chemical products. Because of its high speed, it can not only effectively improve the dispersion efficiency of materials, but also make the materials more fully dispersed, to meet the final requirements of the materials.
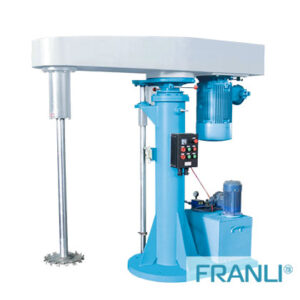
How to choose a suitable high-speed disperser for coatings?
A high speed paint disperser is one of the chemical equipment for stirring, dispersing, and dissolving paint raw materials, slurry, and paint mixture.
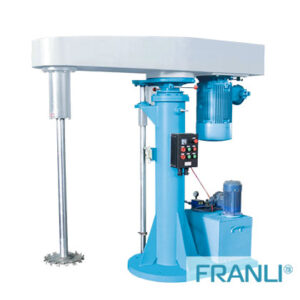
How to use the high speed disperser (new machine)?
The high speed disperser is composed of a frame, a bearing seat, a dispersing shaft, a dispersing wheel, an oil cylinder, a hydraulic station, and a control cabinet. The lifting of the frame adopts hydraulic transmission, and the lifting is stable and reliable.
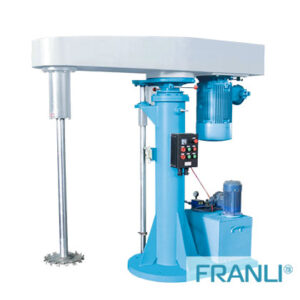
High speed disperser: dispersing, stirring, grinding, dissolving
High speed disperser is common mechanical equipment in chemical production. It is widely used in architectural coatings, chemicals, water-based coatings, oil-soluble architectural coatings, inks, inks, adhesives, etc.