High Shear Emulsifiers in Asphalt Manufacturing: Enhancing Blend Quality and Performance
High Shear Mixer
The use of high-shear emulsifiers in asphalt manufacturing offers numerous benefits, resulting in improved blend quality and enhanced pavement performance. Their ability to generate stable emulsions with uniformly dispersed droplets, reduced mixing time, tailored properties, and cost savings make them an attractive choice for the asphalt industry. As technology advances further, it is likely that high-shear emulsifiers will become even more efficient, providing manufacturers with the tools to create superior asphalt products.
Details of High Shear Mixer
- Suitable for the material before the process
- Small energy consumption
- Large capacity
- Certain self-suction and low lift transport function
Application: Paint, Adhesive, Battery, Pharmaceutical industry, Cosmetic
Asphalt, a widely utilized material in road construction, must meet specific performance criteria to ensure durability and longevity. One crucial aspect of producing high-quality asphalt is the emulsification process, which involves the dispersion of bitumen into water. High-shear emulsifiers have gained popularity in recent years as they offer several advantages in terms of effectiveness, efficiency, and material properties.
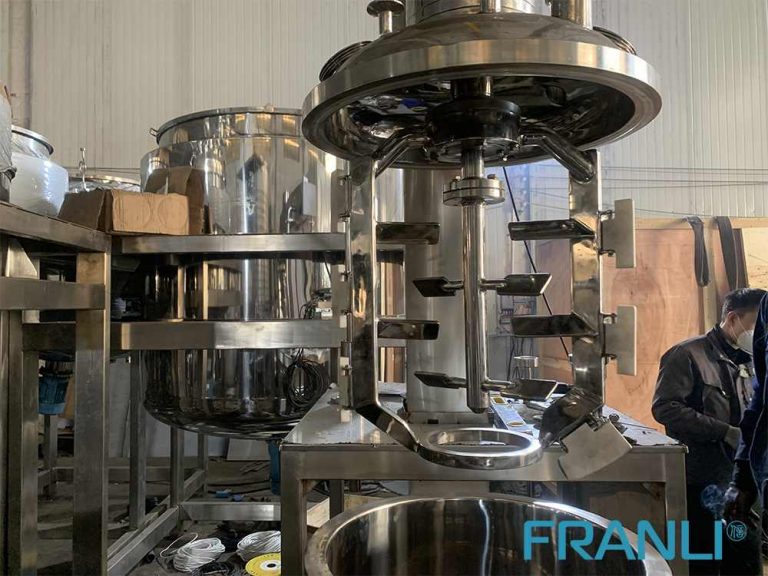
Understanding Asphalt Emulsions
Asphalt emulsions consist of bitumen, which is a semi-solid hydrocarbon, dispersed in water using an emulsifying agent. It is a versatile material that allows for easy application in a broader range of temperatures and weather conditions compared to traditionally used hot mix asphalt. Emulsions are used for various applications, including road paving, chip sealing, micro-surfacing, and tack coats.
The Role of High-Shear Emulsifiers
High-Shear Emulsifiers play a critical role in asphalt manufacturing as they stabilize and facilitate the blending of bitumen and water. They reduce the surface tension between the two immiscible components, preventing separation and ensuring the formation of a stable emulsion. High-Shear Emulsifiers can be categorized into two types: conventional and high-shear.
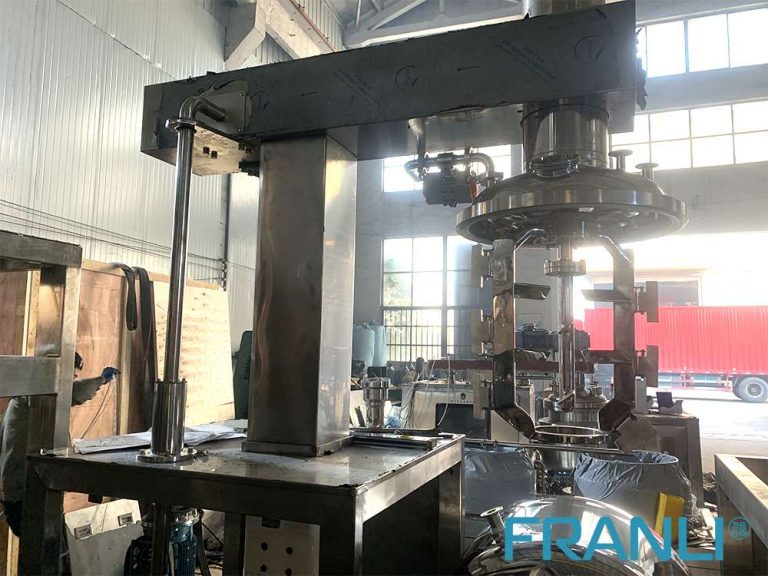
Conventional Emulsifiers vs. High-Shear Emulsifiers
Conventional emulsifiers use mechanical agitation to break down the bitumen into small particles and disperse them in water. This method, while effective, often requires longer mixing times, additional energy input, and may be susceptible to uneven distribution and potential degradation of bitumen properties.
High-shear emulsifiers, on the other hand, employ mechanical devices capable of imparting intense shear forces on the bitumen-water mixture. These devices may include colloid mills, ultrasonic homogenizers, and rotor-stator mixers. By subjecting the emulsion to high shear, the emulsification process is accelerated, resulting in stable and highly uniform asphalt emulsions.
Advantages of High-Shear Emulsifiers:
1. Improved Emulsion Stability: High-shear emulsifiers generate smaller and more uniformly dispersed droplets, leading to enhanced emulsion stability. This stability translates into improved coating and adhesion to aggregates, minimizing the tendency for water stripping and ensuring long-lasting pavement performance.
2. Enhanced Mixing Efficiency: High-shear devices significantly reduce the mixing time required for asphalt emulsion production. The rapid breakdown of bitumen droplets under intense shear facilitates faster emulsion formation, optimizing production throughput and reducing energy consumption.
3. Consistent and Controlled Particle Size: High-shear emulsifiers contribute to consistent and controlled particle size distribution in asphalt emulsions. This uniformity helps regulate the application rate, promote desirable coating thickness, and improve overall mix performance.
4. Tailored Emulsion Performance: The intense shearing action of high-shear emulsifiers allows for precise control over the emulsion’s properties. Manufacturers can alter the binder content, particle size distribution, and rheology to tailor the emulsion to specific application requirements. This flexibility lends itself to customized solutions for various climate conditions and pavement maintenance needs.
5. Cost Savings: High-shear emulsifiers enable a more efficient utilization of resources and improved production scalability. The reduced processing time and enhanced emulsion stability mitigate product loss, resulting in cost savings during manufacturing, transportation, and application.
Welcome to send inquiry to us and let’s make a win win business together !
Guidelines For High Shear Mixer
The mixing device of the high shear mixer is a rotor with four blades, which rotates at a high speed in a stationary stator to complete the entire stirring and mixing process.
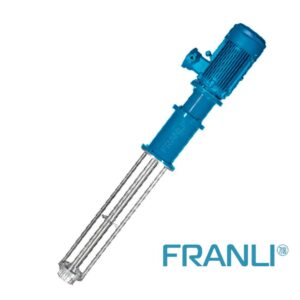
High Shear Mixers: A Guide to Applications in the Cosmetics Industry
A high shear mixer is one of the most versatile pieces of equipment used in the cosmetic industry. It is designed to mix, emulsify, disperse, and homogenize a wide range of cosmetic products.
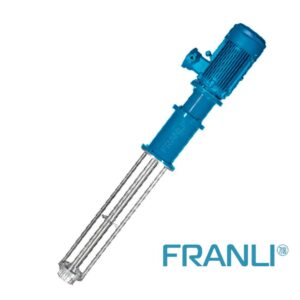
What is a High Shear Emulsifier?
High shear emulsifiers are innovative and efficient machines that are used in various industries for the purpose of emulsification, homogenization, and particle size reduction.
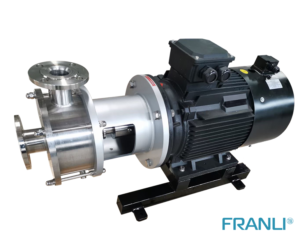
What is an Inline Homogenizer?
An inline homogenizer is a machine that is used to mix and blend different substances together to create a uniform mixture. It is an essential tool in the manufacturing industry, particularly in the production of food, pharmaceuticals, and cosmetics.
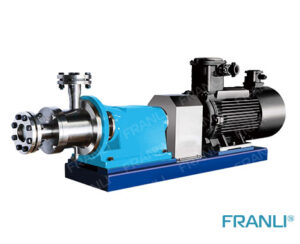
What is an Inline Emulsifier?
An inline emulsifier is a type of high shear mixer that is designed to create a stable emulsion by breaking down the droplets of one liquid into smaller droplets and dispersing them throughout the other liquid.
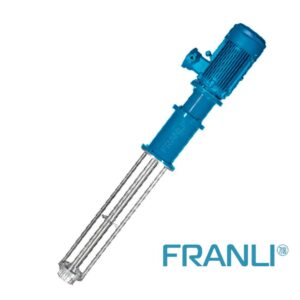
High Shear Mixer: An Essential Tool for Efficient Mixing
A high shear mixer is a device that is used to mix, emulsify, disperse, and homogenize materials. It is a versatile tool that can be used in a variety of industries such as food, pharmaceuticals, cosmetics, and chemical manufacturing.
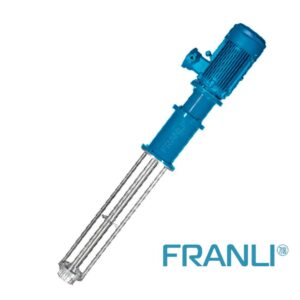
High Shear Mixers: Experimental & Production
High-shear mixers are primarily used in industry to produce standard mixtures of ingredients that do not mix naturally. When the total fluid of the material is composed of two or more liquids, after the work of the high-shear mixer, an emulsion is finally formed.