High Shear Mixers in Acrylic Manufacturing: Enhancing Efficiency & Quality
High Shear Mixer
High shear mixers significantly impact the processing of acrylic due to the intense mechanical forces they impart. These mixers consist of a rotor-stator system, where a rapidly rotating rotor creates a powerful suction that draws the material into the headspace between the rotor and stator. The fluid is then subjected to intense shearing forces due to the confined space, resulting in efficient emulsification, dispersion, and blending of the acrylic components.
Details of High Shear Mixer
- Suitable for the material before the process
- Small energy consumption
- Large capacity
- Certain self-suction and low lift transport function
Application: Paint, Adhesive, Battery, Pharmaceutical industry, Cosmetic
Acrylic, also known as acrylic resin, is a versatile and widely used material in various industries, including automotive, construction, and signage. To seamlessly incorporate acrylic into manufacturing processes, it is essential to achieve a homogenous and high-quality end product. This is where high shear mixers play a vital role.
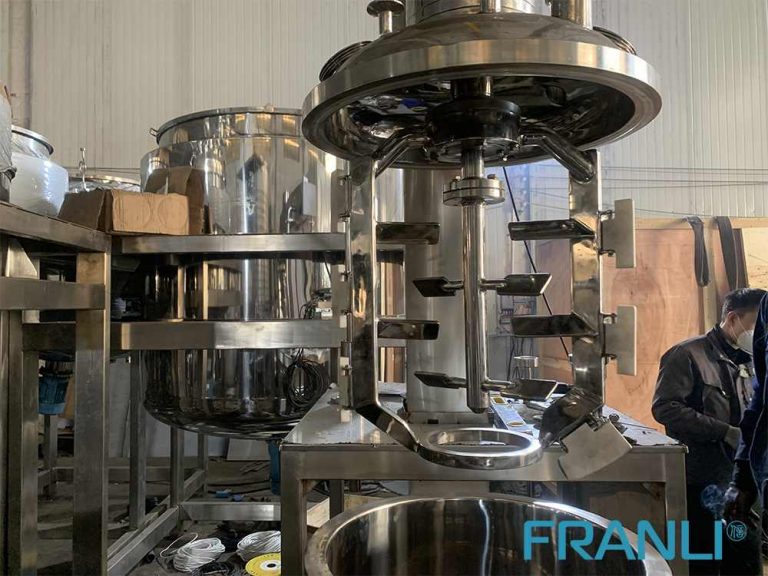
Advantages of High Shear Mixers in Acrylic Manufacturing:
(1)Efficient Blending and Homogeneity:
High shear mixers are highly effective in achieving a uniform distribution of particles in the acrylic matrix. The intense mixing action ensures that all ingredients are fully dispersed and blended, eliminating the formation of agglomerates and minimizing uneven distribution. This results in an acrylic product with consistent properties and desirable characteristics.
(2)Shorter Processing Time:
High shear mixers enable rapid and efficient processing, reducing the overall production time required for acrylic manufacturing. Compared to traditional mixing methods, high shear mixers can significantly reduce the time needed for wetting, dissolving, and dispersing acrylic components, thus improving efficiency and productivity.
(3)Flexibility in Formulation:
High shear mixers offer versatility in acrylic manufacturing as they can handle a wide range of viscosities, allowing for greater flexibility in formulation. By adjusting the mixing speed and shear rates, manufacturers can customize the process parameters to meet specific product requirements. This flexibility facilitates the production of various acrylic-based products with different characteristics, such as viscosity, clarity, and color.
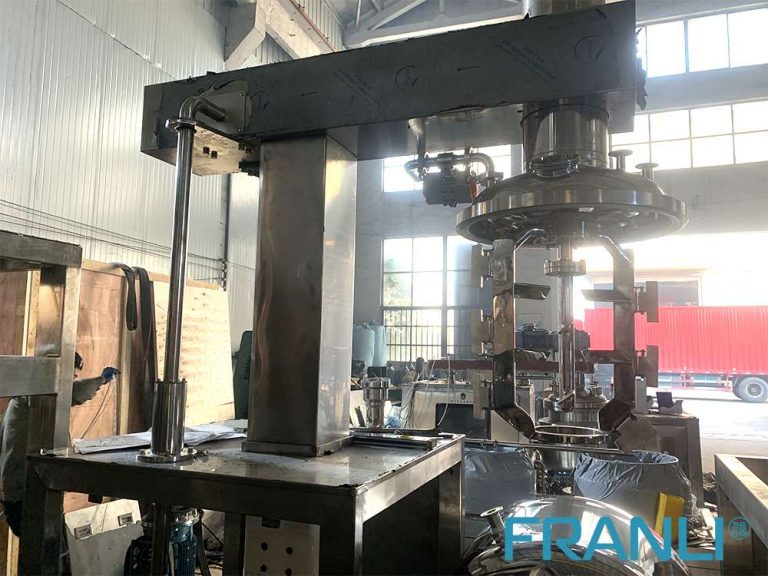
Impact on Product Quality
(1)Enhanced Material Performance:
The high shear forces exerted by these mixers promote better dispersion of fillers, pigments, and additives, resulting in improved material performance. This leads to an acrylic product with enhanced strength, durability, and stability, making it suitable for demanding applications. Additionally, the efficient particle dispersion minimizes the likelihood of particle settling during storage, ensuring product integrity over time.
(2) Improved Optical Clarity:
In applications where optical clarity is crucial, such as in acrylic sheets used for display purposes, high shear mixers play a vital role. By achieving thorough particle dispersion, these mixers help eliminate visible particulates and blemishes, resulting in a visually appealing, transparent acrylic product. Furthermore, the efficient blending reduces light scattering, enhancing the overall optical clarity of the material.
(3)Consistent Color Reproduction:
High shear mixers ensure a uniform dispersion of pigments throughout the acrylic matrix, enhancing color consistency across the entire product. This is particularly important in industries where color matching is critical, such as signage and automotive manufacturing. The efficient dispersion achieved by high shear mixers minimizes color variations and ensures accurate reproduction, meeting customer expectations and improving overall product quality.
Industrial Applications
High shear mixers find widespread applications in the acrylic manufacturing industry, including but not limited to the following areas:
(1)Acrylic Adhesives:
High shear mixing efficiently disperses adhesives’ constituents, ensuring consistent bonding performance for applications where adhesive strength and durability are essential.
(2) Acrylic Emulsions:
For the production of acrylic emulsions, high shear mixers aid in the complete dissolution of monomers and simultaneous emulsification to create stable, uniform emulsions. This enables the production of various acrylic-based coatings and paints that exhibit excellent adhesion, water resistance, and film-forming properties.
(3)Acrylic Resin Manufacturing:
In the production of acrylic resins, high shear mixers facilitate the efficient blending of monomers and initiators, resulting in high-quality resins with desired molecular weight and properties. These resins find applications in various industries, including automotive, construction, and medical.
High shear mixers play a crucial role in acrylic manufacturing, ensuring efficient blending, homogeneity, and material performance. The versatility and flexibility offered by these mixers enable manufacturers to customize formulations, reduce processing time, and enhance end product quality. The use of high shear mixers in the acrylic industry is a testament to the continuous efforts to optimize manufacturing processes and meet the evolving demands of various industries that rely on acrylic-based products.
Welcome to send inquiry to us and let’s make a win win business together !
Guidelines For High Shear Mixer
The mixing device of the high shear mixer is a rotor with four blades, which rotates at a high speed in a stationary stator to complete the entire stirring and mixing process.
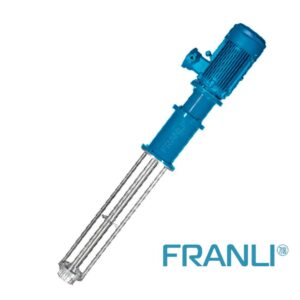
High Shear Mixers: A Guide to Applications in the Cosmetics Industry
A high shear mixer is one of the most versatile pieces of equipment used in the cosmetic industry. It is designed to mix, emulsify, disperse, and homogenize a wide range of cosmetic products.
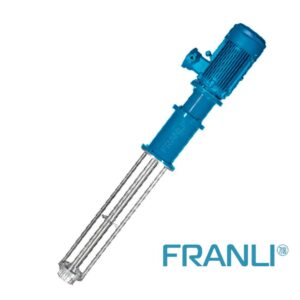
What is a High Shear Emulsifier?
High shear emulsifiers are innovative and efficient machines that are used in various industries for the purpose of emulsification, homogenization, and particle size reduction.
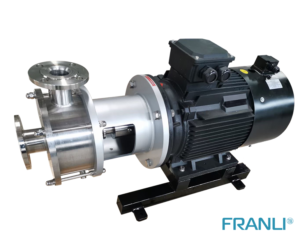
What is an Inline Homogenizer?
An inline homogenizer is a machine that is used to mix and blend different substances together to create a uniform mixture. It is an essential tool in the manufacturing industry, particularly in the production of food, pharmaceuticals, and cosmetics.
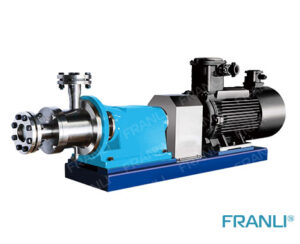
What is an Inline Emulsifier?
An inline emulsifier is a type of high shear mixer that is designed to create a stable emulsion by breaking down the droplets of one liquid into smaller droplets and dispersing them throughout the other liquid.
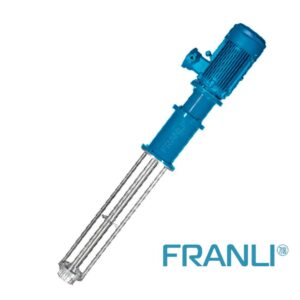
High Shear Mixer: An Essential Tool for Efficient Mixing
A high shear mixer is a device that is used to mix, emulsify, disperse, and homogenize materials. It is a versatile tool that can be used in a variety of industries such as food, pharmaceuticals, cosmetics, and chemical manufacturing.
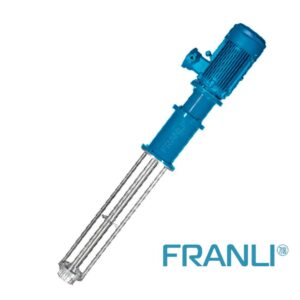
High Shear Mixers: Experimental & Production
High-shear mixers are primarily used in industry to produce standard mixtures of ingredients that do not mix naturally. When the total fluid of the material is composed of two or more liquids, after the work of the high-shear mixer, an emulsion is finally formed.