Sand Mill: Wet Ultrafine Grinding Equipment
Sand Mill
A sand mill, also known as a bead mill, is mainly used for the wet grinding of chemical liquid products. According to the performance, the sand mill can be divided into a vertical sand mill, horizontal sand mill, basket sand mill, Rod sand mill, etc.
Application: Paint, Adhesive, Battery, Pharmaceutical industry, Cosmetic
The sand mill is mainly composed of a body, a grinding cylinder, a disperser, a bottom valve, a motor, and a feeding pump. The speed of feeding is controlled by the valve. The grinding media of sand mills are generally divided into glass beads, zirconia glass beads, zirconia beads, etc. The feeding pump generally adopts a gear pump, diaphragm pump, and other thick slurry feeding pump.
Working principle of horizontal sand mill
The horizontal sand mill mainly uses the material pump to input the solid-liquid phase mixture material after the pre-dispersion and wetting treatment of the mixer into the barrel, and the material and the grinding medium in the barrel are stirred by the high-speed rotating disperser so that the material in the material is stirred. The solid particles and the grinding medium produce more intense collision, friction, and shearing effects with each other, to achieve the purpose of accelerating the grinding of fine particles and dispersing aggregates.
After grinding and dispersing, the grinding medium is separated by a dynamic separator and flows out from the discharge pipe. The horizontal sand mill is especially suitable for dispersing and grinding products with high viscosity and fine particle size. Compared with grinding equipment such as ball mills, roller mills, and colloid mills, the sand mill has the advantages of high production efficiency, strong continuity, low cost, and high product fineness. The process conditions vary greatly, and the fineness requirements can be adjusted by adding or subtracting grinding media in an appropriate amount.
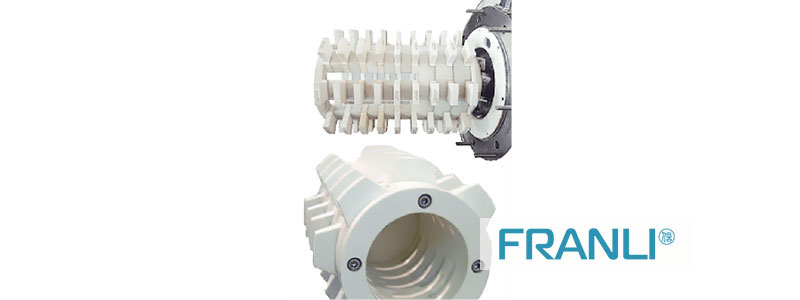
Sand mills belong to wet ultrafine grinding equipment, which is developed from ball mills. Widely used in pigment dispersion and grinding in the ink production process. Sand mills have different classification methods: according to the structure and shape of the stirring shaft, they can be divided into disc type, rod type, and rod disc type (both bump type).
According to the layout of the grinding cylinder, it can be divided into vertical type and horizontal type. According to the volume of the cylinder, it can be divided into the laboratory, small, medium, large, and super large. According to the medium separation method, it can be divided into static and dynamic separation sand mills. According to the energy density (installed power per unit volume), it can be divided into low/high energy density sand mills.
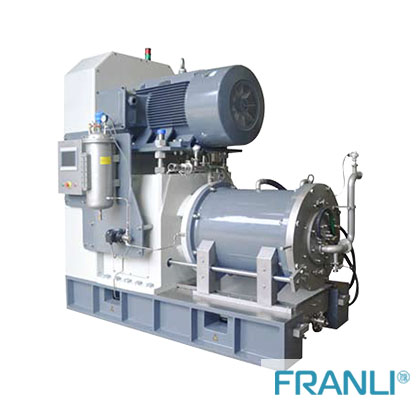
1. During the application process, if the temperature of the nano-sand mill is too high or the working pressure is too high, you should check it to see if the stainless steel screen of the sand mill is blocked. It should be shut down immediately for inspection, and cannot be started forcibly.
2. To ensure the application effect, it is necessary to know the application status of the sand mill in real-time. For example, a grinder should be kept clean to ensure that when there is a problem with the grinder, it can be reflected from under the reflector window of the grinder in time and prevent a series of failures caused by not finding results.
3. As the key application part in the sand mill – zirconium beads, we all require frequent cleaning and replacement. When using new zirconium beads, it is necessary to remove the residue in the toxic zirconium beads and stop cleaning the high column in the sand mill to prevent the sand mill from being blocked due to the residues in the new zirconium beads.
4. If the coupling of the nano sand mill does not move, use the pump to pump the solvent. Start after dissolving. The breakage prevention of the friction plate cannot be forcibly activated.
Welcome to send inquiry to us and let’s make a win win business together !
Guidelines For Sand Mill
The sand mill mainly uses friction, shearing, and collision as effective grinding methods. It is one of the grinding equipment currently applicable to a wide range of material particle sizes and has high grinding efficiency. The energy density per unit volume is large. The control system can complete the continuous grinding and continuous discharging of the slurry, which greatly improves the production efficiency of the sand mill. It has the advantages of high energy density, fine product granularity, small environmental pollution, simple equipment structure, and convenient maintenance.
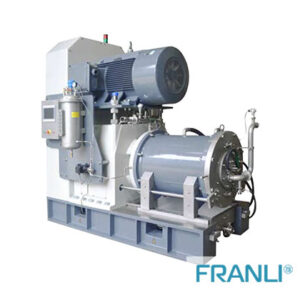
Sand Mill: Enhancing the Efficiency of Grinding & Dispersion
Sand mills, also known as bead mills or media mills, are mechanical devices used in the field of grinding and dispersion.
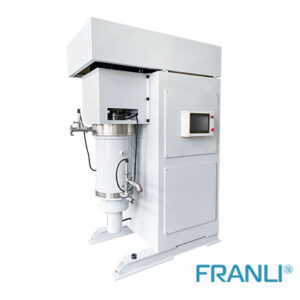
Instructions for use of vertical sand mill
The vertical sand mill is a nano-sand mill whose grinding cylinder adopts a suspended structure, raw materials enter from the bottom and discharge from the top.
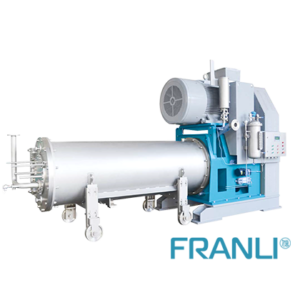
How to choose the right vertical sand mill & horizontal sand mill?
Vertical sand mills and horizontal sand mills are commonly used equipment for grinding in paint, coating, ink, and other industries. They all rely on the high-speed rotation between the grinding medium and the material for grinding work.
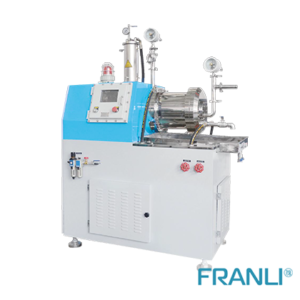
How to deal with the problem of sand mill?
The sand grinding machine, also known as the pearl grinding machine, is used to grind the paint of the pigment with hard wear -resistant beads, glass balls, etc. in a closed cavity.
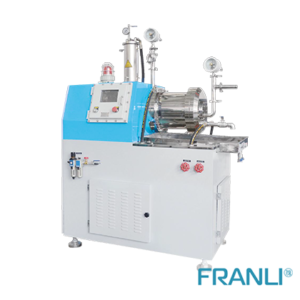
How to choose a sand mill for paint?
Sand mills are mainly used in industrial fields such as paint coatings, cosmetics, food, daily chemicals, dyes, inks, pharmaceuticals, magnetic recording materials, ferrites, photosensitive films, oxide ceramics, and new energy.
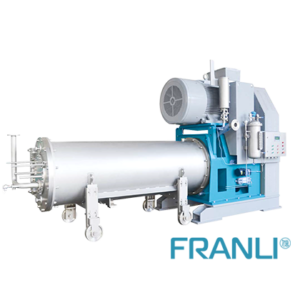
Grinding media for sand mills
Sand mill is a kind of high-efficiency grinding equipment, which is mainly used for grinding materials, and the particle size of the final grinding can reach the nanometer level.