Home » Horizontal & Vertical Ribbon Blender: Industrial Blending Equipment
Horizontal & Vertical Ribbon Blender: Industrial Blending Equipment
Ribbon Blender
Advantages of Ribbon Blender
- fast and efficient
- safe and stable
Application: chemical, pesticide, dye, medicine, feed, fertilizer, metallurgy, mining, food, plastic, additives, and other industries.
A ribbon blender is a versatile industrial mixing machine that has been used in various industries for decades. It is a mixing device that is designed to blend dry powders, granules, and other solid materials. The ribbon blender is a popular choice for manufacturers in the food, chemical, and pharmaceutical industries.
Horizontal ribbon mixer
The horizontal ribbon mixer has changed the mixing state of powder and powder, powder and liquid, solid materials, and granular materials in the traditional process, and has changed the mixing of these types of materials, and has high speed, high efficiency, easy operation, and convenient cleaning. , No pollution, and so on. Horizontal Ribbon Mixer is widely used in medicine, food (such as milk tea, instant tea powder, food additives, flavors and fragrances, condiments, soy protein isolate, spraying lecithin, etc. mixing process), veterinary medicine, starch, papermaking, chemical industry, feed, CPE plastic particles, and other industries.
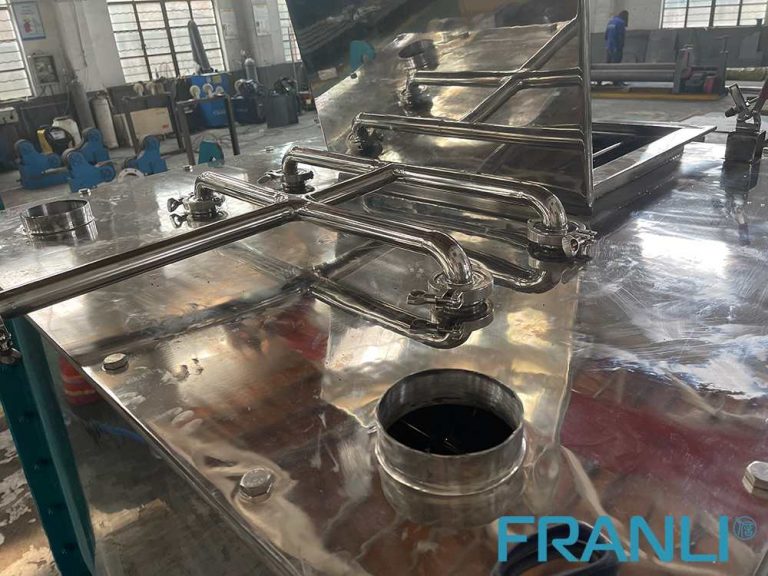
Features of Horizontal Ribbon Mixer
1. The whole machine is easy to clean: it meets the needs of each batch and each shift in the factory, and the user can clean the inside of the equipment without leaving any dead ends.
2. The uniformity of material mixing is high: it can realize uniform mixing of materials with a ratio of 1:10000, especially for the mixing of materials with large specific gravity, which shows the advantages of mixing. Engineers from FRANLI have done a field test. Within 10 minutes, they mixed 1000 kg of materials and about 5 kg of red powder. After sampling and testing at each corner, the mixing uniformity is very high.
3. Fast mixing speed and high efficiency: Usually, each batch of materials is fully mixed within 1-10 minutes, and the efficiency is 6-10 times or higher than that of other mixers.
4. Fast and convenient discharge: usually 1 to 2 minutes to complete a batch of materials. During the user’s on-site test, the discharging time of 1000 kg flour was 47 seconds.
5. Large loading capacity: the equipment usually has a loading capacity (loading factor) of more than 70%.
6. Less residue: users always think that the residue of horizontal equipment is large, but this is not the case, because the gap between the outer spiral belt and the U-shaped cylinder wall is very small in the process of processing, and the spiral belt is always When it is running, the material moves towards the discharge valve, and all the light is emitted. In the user’s field test, 1000 kg of flour remained at 5 kg.
7. Satisfy vacuum feeding and dust-free discharging, avoiding dust flying during the whole feeding, mixing, and discharging process.
8. The mixing process is mild, and the original state of the material is not damaged.
9. No pollution to materials: The mixing mechanism of the equipment is integral, safe, and reliable, and all corner welds are smoothly transitioned and easy to clean; the lubricating parts are all in the
Outside the barrel, no dripping oil and abrasive debris penetrate the material, and the operation can be sealed to prevent dust in the air from entering the material.
10. Low requirements for the factory building: the equipment is horizontal, and various forms of driving devices and discharge positions can be selected arbitrarily, without being restricted by the height of the factory building and the occupied area.
11. The equipment runs smoothly and reliably, with few wearing parts, long service life, convenient maintenance, and simple operation.
Vertical ribbon mixer
The Horizontal Ribbon Mixer design is specifically engineered to handle materials that are highly cohesive, sticky, or bulky, such as powders, pastes, and other solid forms. The double ribbon agitator displaces the product continuously, ensuring that the material is mixed uniformly and efficiently, without any dead spots or pockets of unmixed materials. Horizontal Ribbon Mixers are commonly found in food processing industries as they offer advantages such as fast blending, gentle blending, and a reduction in dust.
The vertical ribbon mixer is driven by the middle screw and the outer ribbon, and the material to be mixed moves up and down and circularly in the cylinder, to achieve the required mixing uniformity.
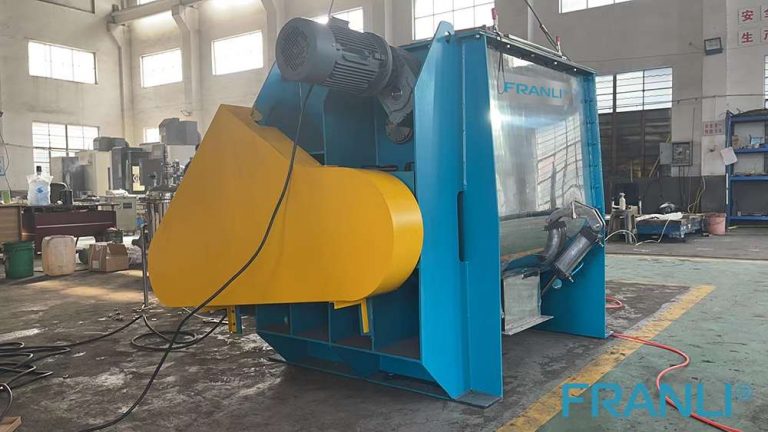
A. Stirring parts
According to different materials, the middle forward or reverse the spiral and the outer continuous or disconnected spiral can be selected to form the stirring assembly.
B. Application scope
This kind of mixer can be used for mixing viscous slurry and solid powder through different combinations of stirring parts. There is no transmission part in the cylinder, and no sealing and lubrication is required. Therefore, it is especially suitable for industries with strict control of impurities such as pharmaceuticals, food, and batteries.
C. cooling and heating
A jacket can be added outside the barrel of the mixer, and cooling or heating of the material can be achieved by injecting cold and hot media into the jacket; cooling is generally pumped into industrial water, and heating can be fed into steam or electric heating heat transfer oil.
D. Pressure-resistant type
The cylinder cover can be made into a head type, and the cylinder body is thickened to withstand positive or negative pressure, and at the same time, it can reduce residues for easy cleaning. This setting is often used when the cylinder body of the mixer needs to withstand pressure.
E. Feeding method
It can be fed manually, fed by vacuum feeder, or fed by conveying machinery. In a specific process, the barrel of the mixer can be made into a negative pressure chamber, and the dry material with good fluidity can be sucked into the mixing chamber for mixing by using a hose, which can avoid residue and pollution in the material feeding process.
F. Discharge method
Standard equipment generally adopts a plum blossom-shaped “displacement valve”, which is closely attached to the bottom of the long spiral, effectively reducing the mixing dead angle, and the driving form is optional with manual and pneumatic; according to user needs, side discharge, butterfly valve, Ball valves, flapper valves, star unloaders, etc.
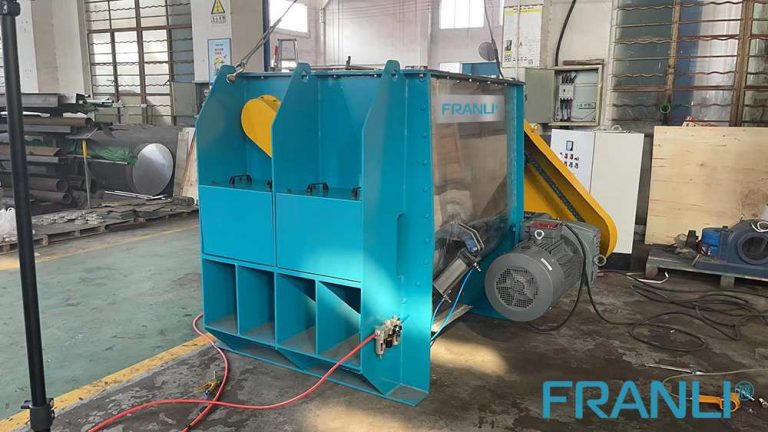
The ribbon blender is made up of a U-shaped trough and a ribbon agitator. The ribbon agitator consists of two helical ribbons that rotate on a central shaft. The ribbons are designed to move the materials in a horizontal direction, creating a gentle tumbling action that ensures that all particles are evenly mixed.
One of the main advantages of the ribbon blender is its versatility. It can be used to blend a wide range of materials, from powders and granules to pastes and slurries. It is also gentle enough to blend fragile materials without damaging them.
The ribbon blender is also an efficient mixing machine. Its design ensures that all particles are evenly mixed, which reduces the need for additional blending time. This can result in significant cost savings for manufacturers.
Another advantage of the ribbon blender is its ease of use. It requires minimal operator input and can be easily automated, which reduces the risk of human error and increases productivity.
The ribbon blender is also easy to clean, which is an important consideration for manufacturers in the food and pharmaceutical industries. Its U-shaped trough and ribbon agitator can be easily accessed for cleaning, and the machine can be disassembled for more thorough cleaning.
Welcome to send inquiry to us and let’s make a win win business together !
Guidelines For Ribbon blender
Ribbon blenders are essential equipment in various industries where the quality and consistency of the final product are critical factors. They are highly efficient, customizable, and reliable mixing solutions that offer unsurpassed performance and versatility. By integrating a ribbon blender into your production line, you can ensure consistent and reliable product quality, increased productivity, and reduced manufacturing costs.
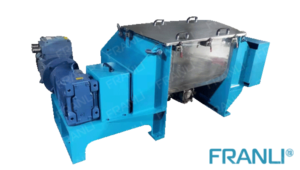
Ribbon Blender Mixer Equipment
A ribbon blender mixer, also known as a ribbon mixer or horizontal ribbon blender, is a powerful industrial machine designed for thorough and efficient blending of various materials.
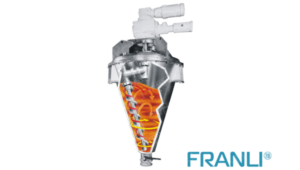
Ribbon Blender Mixer: The Right Choice for a High-Quality Blender
Ribbon blender mixers, also known as ribbon mixers or ribbon blenders, are horizontal mixing devices characterized by their unique ribbon-shaped agitators.
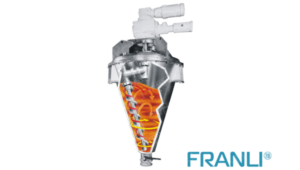
Vertical Ribbon Blender: Efficient mixing equipment for solids and powders
A vertical ribbon blender, also known as a vertical mixer, is a type of mixing machine widely used in various industries for the homogeneous blending of dry, free-flowing solids.
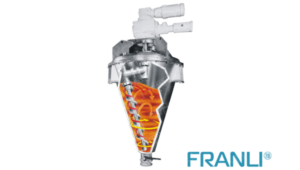
Powder Ribbon Mixer: Whirling Agitator and Horizontal U-shaped Housing
A powder ribbon mixer, also known as a ribbon blender, is a versatile and widely used machine for combining different powders, powder with liquid, powder with granules, and dry solids.
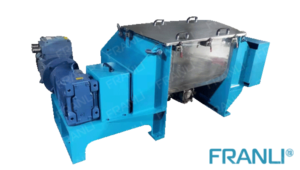
Small Ribbon Blender: A Versatile and Efficient Processing Equipment
The small ribbon blender is a versatile and efficient processing equipment used in the food, pharmaceutical, and cosmetic industries for blending, mixing, and uniformizing various types of materials.
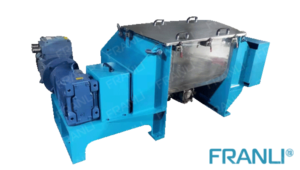
What is A Small Ribbon Blender?
The small ribbon blender is a versatile and efficient machine used for the mixing of various materials such as powders, pastes, and dried granules.