Home » Purchasing skills of vacuum kneader: sealing method & discharge method
Purchasing skills of vacuum kneader: sealing method & discharge method
Kneader
Details of Kneader
- The machine comprises a motor, cover press, main body, mixing chamber and rotor mechanism, gearbox, air control system, tilting machine, heating/cooling system, rubber belt transmission and base, etc.
- The kneader can be made into vacuum, pressure, atmospheric, Normal temperature, high temperature, low temperature, etc.
- The temperature adjustment method of a kneader can be the jacket, halfpipe, far-infrared tile, steam, hot water, heat transfer oil, electric heating, cooling water, chilled water, and other methods.
Application: Paint, Adhesive, Battery, Pharmaceutical industry, Cosmetic
The vacuum kneader belongs to a branch of the kneader and is mainly used in chemical production fields such as glass glue base material, butyl rubber, silica gel, hot melt adhesive, etc., which are prone to bubbles. The kneader has the characteristics of wide application, reliable and stable performance, long service life, low energy consumption, high output, simple operation, and convenient use. The kneader is mainly composed of five parts: the kneading part, the base part, the hydraulic system, the transmission system, and the electric control system.
When users purchase a vacuum kneader, they often have some doubts about its sealing method and discharge form. Conventional vacuum kneaders mainly have three sealing forms: packing seal, mechanical seal, and magnetic fluid seal. The method adopts hydraulic turning cylinder discharging, screw extrusion discharging, bottom discharging, etc., the most common one is hydraulic turning cylinder discharging.
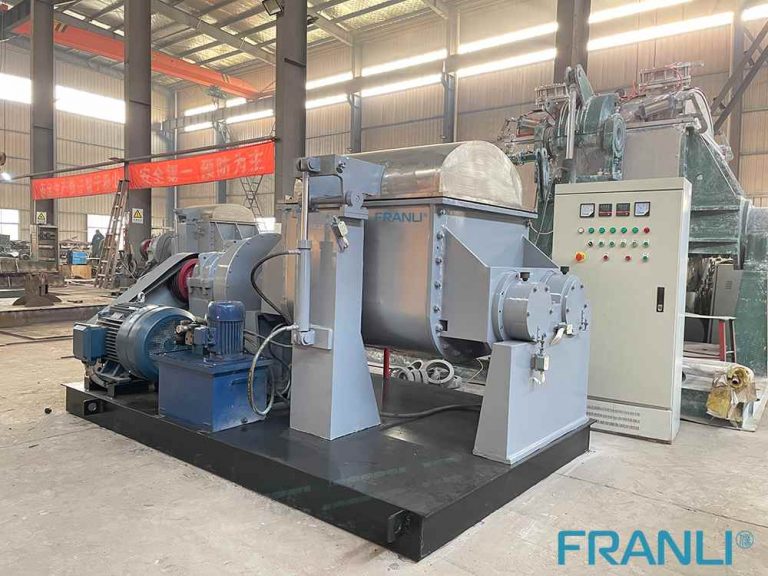
Sealing method of vacuum kneader
Mechanical seal: better sealing performance, less leakage, and long service life, but its price is relatively expensive, and the requirements for processing, installation, maintenance, and maintenance are higher than those of ordinary seals. Mechanical seals are more suitable for conveying petroleum and chemical media and are used for media with different viscosities, strong corrosion, and particles.
Packing seal: cheap price, simple structure, easy maintenance, but large power loss and large leakage. Therefore, the packing seal can be used to transport general media, such as water; it is not suitable for the transportation of petroleum and chemical media, especially in expensive, explosive, and toxic media.
Compared with the packing seal, the magnetic fluid seal has the following advantages: long service life, which can generally reach 1 to 2 years or longer in oil and water media, and can usually reach more than half a year in chemical media; During periodic operation, the sealing state is more stable and the leakage is smaller. According to rough statistics, its leakage is generally only 1/100 of that of soft packing seals; the scope of application is wider, and mechanical seals can be used for high temperature, low temperature, high pressure, vacuum, different speeds, and various corrosive media and media containing abrasive particles, etc. seal.
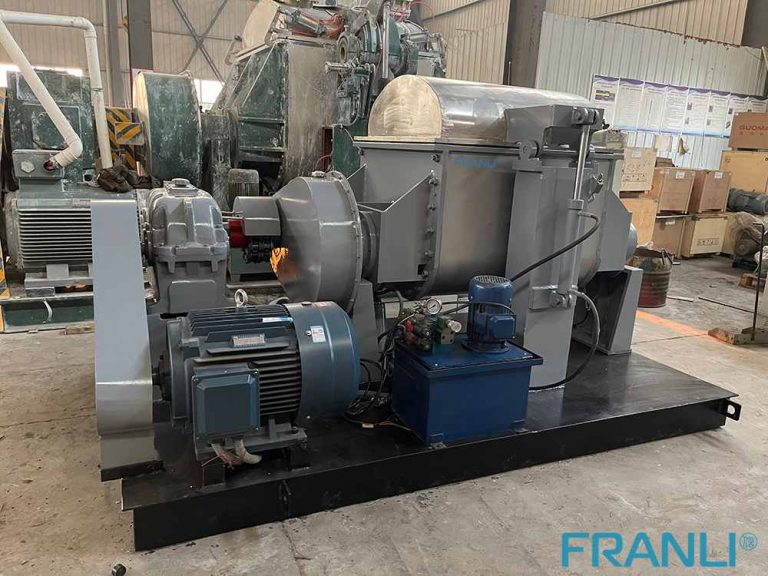
The discharge method of the kneader
The kneader is produced by a pair of blades that cooperate and rotates to produce a strong shearing action so that the semi-dry state or rubber-like viscous plastic material can make the material react quickly and get evenly mixed and stirred.
The discharge form of the vacuum kneader mainly adopts hydraulic cylinder discharge, and the kneading pot is composed of five parts: kneading, base, hydraulic system, transmission system, and electric control system. The kneading part is composed of the cylinder body, pulp shaft, wallboard, cylinder head, and other parts. The hydraulic system uses a hydraulic station to operate the large oil cylinder to complete the functions of opening and closing, closing and turning the cylinder, etc. The electric control system has manual and automatic electric control systems, which can be selected and requested by the operator at will. Easy to operate and reliable.
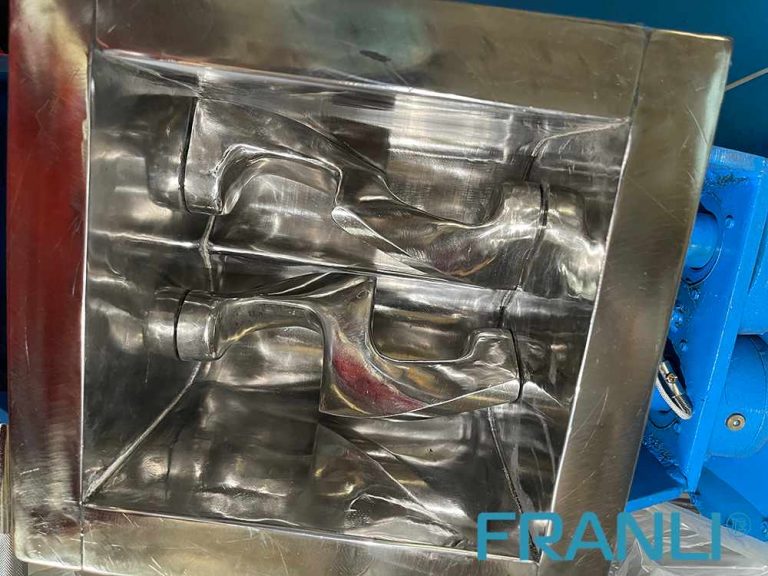
The transmission system of the vacuum kneader is composed of a motor, a reducer, and a gear, and it is matched with the motor according to the type of kneading pot of the kneader. During the transmission process, the synchronous speed can be achieved by the motor, and after passing through the elastic coupling to the reducer, the output device drives the fast paddle to reach the specified speed.
Welcome to send inquiry to us and let’s make a win win business together !
Guidelines For Kneader
The dispersion kneader is suited for rubber and plastic mastication, as well as the blending of different rubber and plastic components. Small and medium-sized rubber and plastics manufacturers with a wide range of product types and colours, as well as food, dyes, pharmaceuticals, and ceramics, can benefit from the internal mixer.
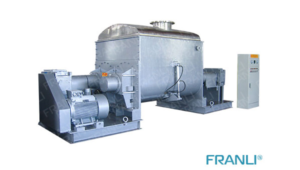
Sigma Kneader: The Solution for Mixing and Kneading
Sigma kneader is a versatile machine that can be used for mixing, kneading, and homogenizing a wide range of materials, including high-viscosity products.
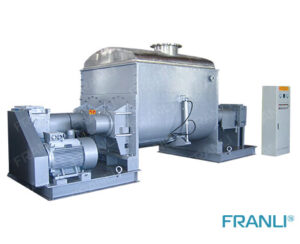
Sigma Mixer: Indispensable Equipment For Manufacturing
Sigma Mixer is a type of mixer that uses a unique mixing principle to achieve an efficient blending of materials. The mixer consists of two blades that rotate in opposite directions, creating a kneading and folding action that ensures thorough mixing. The blades are shaped like the Greek letter Sigma, hence the name Sigma Mixer.
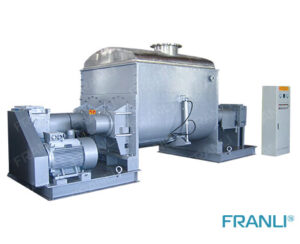
Sigma Blade Mixer: The Mixing Solution
The Sigma Blade Mixer is a robust and reliable mixing machine that uses a unique mixing principle to achieve superior results. It is a type of double-arm kneading mixer that features two blades that rotate in opposite directions.
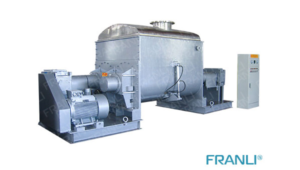
Vacuum Kneader: A Machine for Your Mixing Needs
The Vacuum Kneader is a type of mixer that utilizes a vacuum chamber to create a homogeneous mix of ingredients. It is designed to knead, mix, and disperse high-viscosity materials under vacuum conditions, resulting in a superior product.
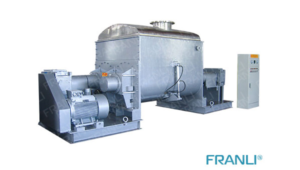
Efficiency and Effectiveness of Dispersion Kneader
The dispersion kneader has complete control over the mixing and blending of the raw materials to create an even mix that allows for better distribution. This device contains a mixing chamber with rotating blades made of high-quality steel.
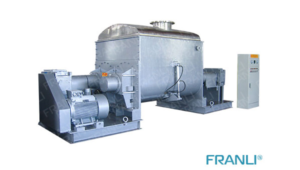
Vacuum kneader: high efficiency and environmental protection
A vacuum kneader is mainly used for stirring, mixing, and kneading high-viscosity and elastic-plastic materials. The most common fields include high-viscosity sealant, silicone rubber, neutral acid glass glue, chewing gum, bubble gum, aluminum silver paste, silica gel, paper pulp, cellulose, and other materials. It covers food, agrochemical, pharmaceutical, cosmetics, electronic paste, and other industries, and has been sought after by the industry.