Home » Kneader | Kneading and Dispersing
Kneader | Kneading and Dispersing
Kneader
Details of Kneader
- The machine comprises a motor, cover press, main body, mixing chamber and rotor mechanism, gearbox, air control system, tilting machine, heating/cooling system, rubber belt transmission and base, etc.
- The kneader can be made into vacuum, pressure, atmospheric, Normal temperature, high temperature, low temperature, etc.
- The temperature adjustment method of a kneader can be the jacket, halfpipe, far-infrared tile, steam, hot water, heat transfer oil, electric heating, cooling water, chilled water, and other methods.
Application: Paint, Adhesive, Battery, Pharmaceutical industry, Cosmetic
The manufacturing principles of the kneader would be, at times, a lot bigger and a better one. It can however be yield a significant amount of units at costs that are lower than the outdated approaches for companies who wish to offer a broader range of products through the expansion of the scale for the productions here. There would also be a traditional fixed kneader that is completely moveable to consider the alternative here. Today, we will be explaining the manner in which they are offering a greater solution that would significantly increase the productivities along with boosting the profit margins.
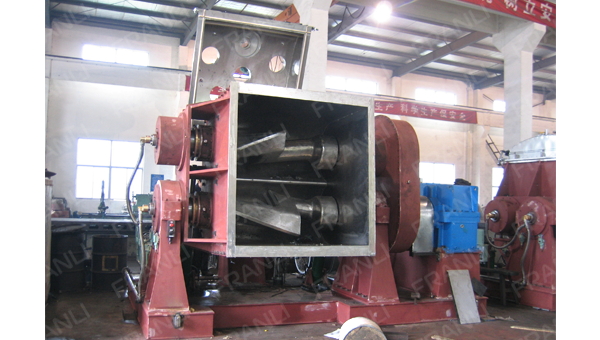
Aiming at the true scaling economies of the kneader
It was noted in the past that while the consumers were considered happy with quite fewer varieties where the manufacturers like Franli were able to prepare a product that is a single one in greater quantities here. These large single-lined processes of production were considered a great option in these few cases here. One also would be moving out to the batch processes that will be paying for the dividends if there is an expansion over the portfolio of the business products made out through the twin-screw kneader.
The reason here would be the greater number of drawbacks that are meant for the ones that are fixed. It is extremely an obvious reason behind your kneader consuming a greater time in terms of filling and in emptying up. It would be creating a bottleneck that would be slowing down the processing steps here as it is extremely generalized to be as the bigger within the industrial mixers that are consuming longer time in terms of emptying and filling up.
Being more flexible
It is through their nature that the materials here are being tipped into being a fixed kneader mixer while the rest of the processes here come to a halt. While the recipes here are being formulated, the product is mixed significantly while you are not able to prepare the other one with the help of the kneader. The two processing stages of the machinery here are still without an action being a product that is emptied out or is called off from its packing zone once the dispersion is completed here.
There would be no other steps involved here with the time that is consumed in terms of filling out the static kneader that would be discharging greater numbers of the massive bags that fills the machine significantly. It is also a process that is significant enough in terms of transferring the heights to which the risk of the materials getting desegregated increased through the bad quality of the product here.
The highly effective solution that can be involved here would be in making use of the contained-based systems here. These would be dispersing within the vessels in terms of accommodating the varied sizes of the batches here along with decoupling of the system which is getting transferred here lying in between the processing steps that would be meant to be holding up gets eliminated here.
It would therefore be offering a greater rate of flexibility that can be formulated easily offline while there are the rest of the batches are being blended together, either being packed or are mixed. The reason being the kneader is dedicated to using the fixed lines that can make the process of production a lot leaner.
Improving the efficiency of kneader
The kneader here is available in almost varied sizes that would be matching up well with the size of the batch, thereby filling and the emptying times that are being optimized here.
Efficient emptying solution
This kneader here would also be needing the line of processing that would be at a standstill while this product here is being emptied out.
Further, Improve Efficiency
These equipment are made available in their various sizes involved here, and it is done through the match up of the volume with the size of the batch that can help in filling and emptying of the times that are optimized significantly.
These can be efficient enough in terms of offering the kneading solutions in the most significant manner.
There are several filling applications that require the line of processing while attaining a standstill, with every product having its own specific time of filling up and emptying out.
The container is being moved into the area that allows the constant productions while the other batch is being mixed here, with it being significantly a notable choice of the same.
The process of dispersing
The mixture in which the particles of a single material are being distributed over at the continuous phase of the other is brought about by the kneader that is now being supplied and manufactured by the well-known company Franli.
This is a process that is quite complicated here. The goal that is involved here in the process of dispersion involves the mixing of the solids along with the liquid or even the liquid with other others. There are several finished materials that should possess a few of the finerparticles with the significant goal that involves the achieving of the particles that can spread evenly within the liquid here. The machine, however, would be taking the particles along with breaking them down in terms of creating the homogeneous mixture with the help of the kneader. The surface area would be exposed further on with the breakdown of the materials.
The process is driven through the help of shear or force with the edge of the impeller that can help create an action that necessitates the dispersion of the particles that also involves the spectrum that is quite soluble here. It is also the process that is performed mainly at greater speed, needing a lot more energy instead of the mixing methods that are conventional ones.
It is the process that involves mixing along with the dispersion of the elements with the help of a kneader. It is through a thorough understood that there are right similarities as well as the differences that are involved in the production of the material here. You also need to be able to figure out the kind of processes that are needed here for the distinctive application of the product.
Welcome to send inquiry to us and let’s make a win win business together !
Guidelines For Kneader
The dispersion kneader is suited for rubber and plastic mastication, as well as the blending of different rubber and plastic components. Small and medium-sized rubber and plastics manufacturers with a wide range of product types and colours, as well as food, dyes, pharmaceuticals, and ceramics, can benefit from the internal mixer.
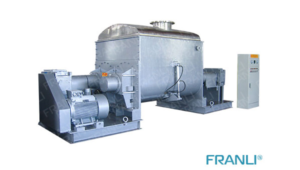
Sigma Kneader: The Solution for Mixing and Kneading
Sigma kneader is a versatile machine that can be used for mixing, kneading, and homogenizing a wide range of materials, including high-viscosity products.
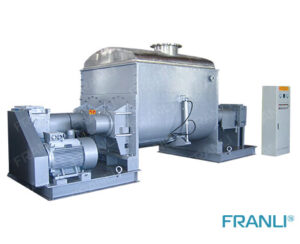
Sigma Mixer: Indispensable Equipment For Manufacturing
Sigma Mixer is a type of mixer that uses a unique mixing principle to achieve an efficient blending of materials. The mixer consists of two blades that rotate in opposite directions, creating a kneading and folding action that ensures thorough mixing. The blades are shaped like the Greek letter Sigma, hence the name Sigma Mixer.
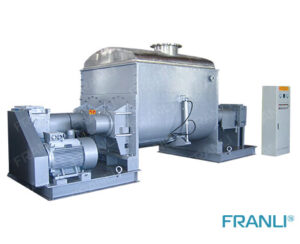
Sigma Blade Mixer: The Mixing Solution
The Sigma Blade Mixer is a robust and reliable mixing machine that uses a unique mixing principle to achieve superior results. It is a type of double-arm kneading mixer that features two blades that rotate in opposite directions.
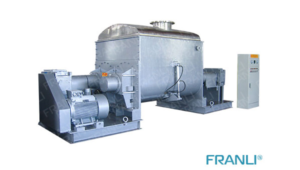
Vacuum Kneader: A Machine for Your Mixing Needs
The Vacuum Kneader is a type of mixer that utilizes a vacuum chamber to create a homogeneous mix of ingredients. It is designed to knead, mix, and disperse high-viscosity materials under vacuum conditions, resulting in a superior product.
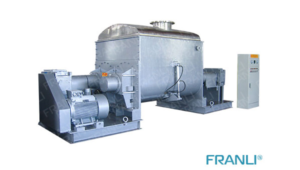
Efficiency and Effectiveness of Dispersion Kneader
The dispersion kneader has complete control over the mixing and blending of the raw materials to create an even mix that allows for better distribution. This device contains a mixing chamber with rotating blades made of high-quality steel.
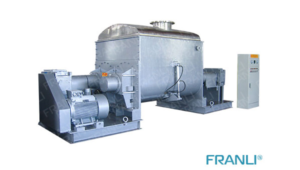
Vacuum kneader: high efficiency and environmental protection
A vacuum kneader is mainly used for stirring, mixing, and kneading high-viscosity and elastic-plastic materials. The most common fields include high-viscosity sealant, silicone rubber, neutral acid glass glue, chewing gum, bubble gum, aluminum silver paste, silica gel, paper pulp, cellulose, and other materials. It covers food, agrochemical, pharmaceutical, cosmetics, electronic paste, and other industries, and has been sought after by the industry.