High Shear Mixers: Enables Fast and Efficient Mixing
High Shear Mixer
High shear mixers are specialized machines designed to generate intense mechanical forces that break down particles, disperse components, and create homogeneous mixtures within a short period. These mixers typically consist of a rotor-stator configuration where a high-speed rotor generates shear forces by interacting with a stationary stator. This unique design allows high shear mixers to achieve rapid and efficient mixing of even the most challenging materials.
Details of High Shear Mixer
- Suitable for the material before the process
- Small energy consumption
- Large capacity
- Certain self-suction and low lift transport function
Application: Paint, Adhesive, Battery, Pharmaceutical industry, Cosmetic
In the realm of industrial processing and manufacturing, the high shear mixer stands as a versatile and indispensable tool for achieving efficient and uniform mixing of various materials. This sophisticated machine, known for its ability to produce intense shear forces and create fine emulsions, dispersions, and blends, has become a cornerstone of modern production processes in industries such as pharmaceuticals, cosmetics, food and beverage, chemicals, and more.
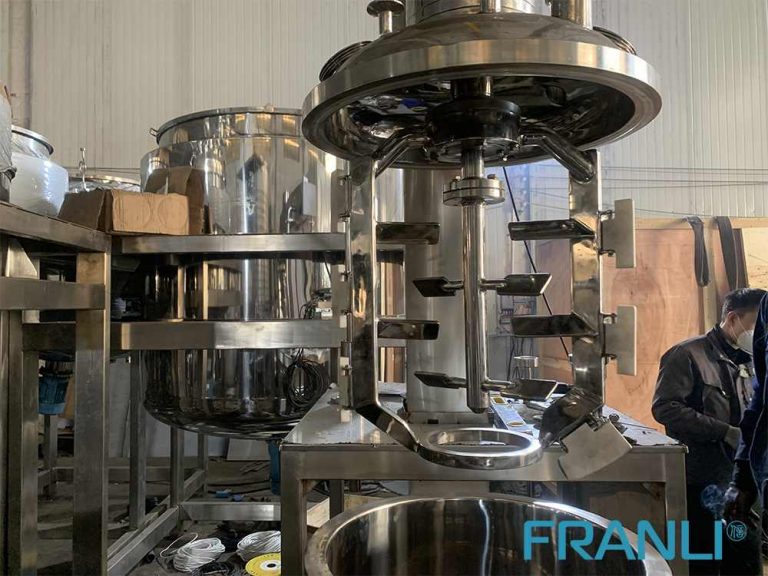
Key Features of High Shear Mixers
1. Rotor-Stator Configuration:
The rotor-stator configuration is the core design element of high shear mixers, enabling them to produce intense shear forces that promote efficient mixing and dispersion of materials.
2. High-Speed Operation:
High shear mixers operate at high speeds to generate the necessary shear forces for breaking down particles, creating emulsions, and achieving uniform blends in a short time frame.
3. Versatile Mixing Capabilities:
High shear mixers are capable of handling a wide range of materials including powders, liquids, solids, and viscous substances, making them suitable for diverse mixing applications.
4. Scalability:
Many high shear mixers offer scalability options that allow users to scale up production processes from lab-scale experiments to full-scale manufacturing without compromising on mixing performance.
5. Control Systems:
Advanced control systems in high shear mixers enable precise adjustment of mixing parameters such as speed, shear intensity, temperature, and time to achieve desired mixing results consistently.
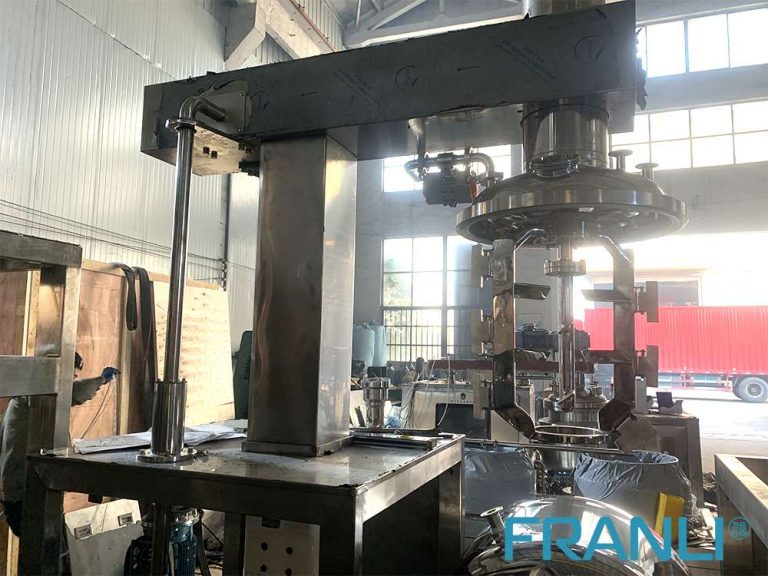
Applications of High Shear Mixers Across Industries
1. Pharmaceuticals:
In the pharmaceutical industry, high shear mixers are used for blending powders, granules, and excipients to produce uniform drug formulations such as tablets, capsules, and suspensions. They are also employed in the production of ointments, creams, and gels by achieving fine emulsions and dispersions.
2. Cosmetics:
High shear mixers play a crucial role in the cosmetics industry for creating emulsions, suspensions, creams, lotions, and other personal care products. They help achieve smooth textures, uniform color distribution, and stable formulations that meet stringent quality standards.
3. Food and Beverage:
In the food and beverage industry, high shear mixers are utilized for blending ingredients in products such as sauces, dressings, mayonnaise, dairy products, beverages, and confectionery items. They ensure consistent product quality, texture control, and flavor homogeneity.
4. Chemicals:
High shear mixers find extensive applications in the chemical industry for mixing polymers, resins, adhesives, paints, coatings, pigments, and other specialty chemicals. They enable efficient dispersion of additives and achieve uniform blends with precise control over product characteristics.
Benefits of Using High Shear Mixers
1. Improved Mixing Efficiency:
High shear mixers offer rapid mixing times and enhanced dispersion capabilities compared to traditional mixing methods, resulting in improved process efficiency and reduced production times.
2. Homogeneous Product Quality:
The intense shear forces generated by high shear mixers ensure thorough blending of materials and creation of homogeneous mixtures with consistent quality attributes such as particle size distribution and texture.
3. Versatility:
High shear mixers can handle a wide range of materials with varying viscosities and properties, making them versatile tools for diverse mixing applications across industries.
4. Reduced Energy Consumption:
By achieving efficient mixing in shorter time frames with minimal energy input, high shear mixers help reduce overall energy consumption during production processes.
5. Scalability:
Many high shear mixers offer scalable designs that allow seamless transition from lab-scale testing to full-scale production without compromising on mixing performance or product quality.
The machine application of high-shear mixers represents a significant advancement in industrial mixing processes across various industries. With their unique rotor-stator configuration, high-speed operation capabilities, versatile mixing capabilities, advanced control systems, diverse applications across industries such as pharmaceuticals cosmetics food beverage chemicals benefits including improved efficiency homogeneous product quality versatility reduced energy consumption scalability these sophisticated machines have become essential tools for achieving optimal mixing results enhancing product quality streamlining production processes ultimately contributing to the success of businesses worldwide. By understanding the key features and benefits applications considerations when choosing a high shear mixer companies can make informed decisions that align with their specific needs requirements ensuring efficient reliable mixing operations that drive innovation growth competitiveness in today’s dynamic market landscape.
Welcome to send inquiry to us and let’s make a win win business together !
Guidelines For High Shear Mixer
The mixing device of the high shear mixer is a rotor with four blades, which rotates at a high speed in a stationary stator to complete the entire stirring and mixing process.
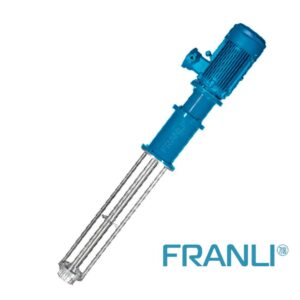
High Shear Mixers: A Guide to Applications in the Cosmetics Industry
A high shear mixer is one of the most versatile pieces of equipment used in the cosmetic industry. It is designed to mix, emulsify, disperse, and homogenize a wide range of cosmetic products.
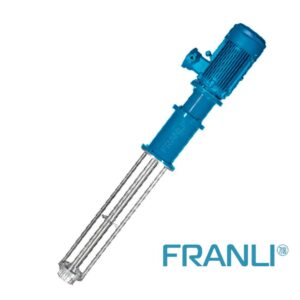
What is a High Shear Emulsifier?
High shear emulsifiers are innovative and efficient machines that are used in various industries for the purpose of emulsification, homogenization, and particle size reduction.
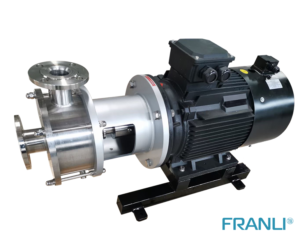
What is an Inline Homogenizer?
An inline homogenizer is a machine that is used to mix and blend different substances together to create a uniform mixture. It is an essential tool in the manufacturing industry, particularly in the production of food, pharmaceuticals, and cosmetics.
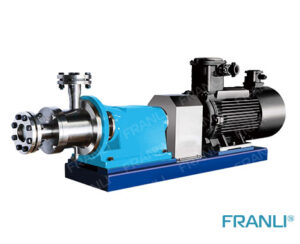
What is an Inline Emulsifier?
An inline emulsifier is a type of high shear mixer that is designed to create a stable emulsion by breaking down the droplets of one liquid into smaller droplets and dispersing them throughout the other liquid.
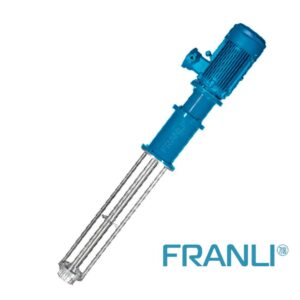
High Shear Mixer: An Essential Tool for Efficient Mixing
A high shear mixer is a device that is used to mix, emulsify, disperse, and homogenize materials. It is a versatile tool that can be used in a variety of industries such as food, pharmaceuticals, cosmetics, and chemical manufacturing.
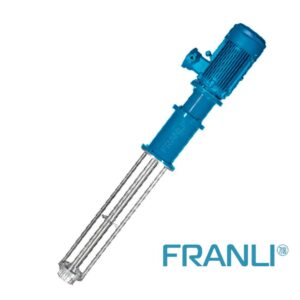
High Shear Mixers: Experimental & Production
High-shear mixers are primarily used in industry to produce standard mixtures of ingredients that do not mix naturally. When the total fluid of the material is composed of two or more liquids, after the work of the high-shear mixer, an emulsion is finally formed.