Home » The Application of Double Planetary Mixers in Polymer Solution Production
The Application of Double Planetary Mixers in Polymer Solution Production
Double Planetary Mixer
Polymer solutions have gained significant importance in various industries due to their unique properties and wide range of applications. These solutions, consisting of a polymer dissolved in a solvent, can be used for coatings, adhesives, inks, and many other products. The production of polymer solutions requires efficient and reliable mixing equipment to ensure the uniform dispersion of polymers in the solvent, and one such equipment that has proven to be highly effective is the double planetary mixer.
Details of Double Planetary Mixer
- The common agitators include paddle type, twist type, claw type, and frame type.
- good mixing, reaction, kneading, and dissolution functions.
Application:
inks, colorants, dyes, coatings, and other industries.
Double planetary mixers, also known as double planetary kneaders, are innovative mixing machines widely used in the manufacturing industry. Their design consists of multiple planetary blades rotating on their axes within a fixed vessel, creating a double planetary motion. This unique motion ensures thorough mixing and blending of materials by combining both axial and radial movement.
The working principle of a double planetary mixer involves the rotation of the main drive, which spins the planetary blades on their axes while simultaneously revolving them around the center axis of the vessel. This combination of movements provides intensive and consistent mixing, preventing dead zones and ensuring the uniform dispersion of materials. The double planetary motion also enables the mixer to handle high-viscosity materials and effectively mix shear-sensitive substances.
Advantages of Double Planetary Mixers in Polymer Solution Production
1. Efficient Mixing: The double planetary motion of the mixer ensures efficient mixing of polymer and solvent, resulting in a homogenous solution. The blades sweep through the entire mixing vessel, leaving no unmixed areas or pockets. This uniform mixing creates a stable polymer solution with consistent properties throughout.
2. Enhanced Heat Transfer: Double planetary mixers offer excellent heat transfer capabilities during the mixing process. The continuous movement of the planetary blades helps dissipate heat generated during mixing, preventing localized overheating and maintaining the temperature within the desired range. This is particularly important for temperature-sensitive polymers.
3. Scalability: Double planetary mixers are available in various sizes, making them suitable for different production scales. They can be used in small-scale laboratories or large-scale industrial operations, allowing for easy scale-up of polymer solution production.
4. Versatile Applicability: Double planetary mixers are versatile and can be used for a wide range of polymer solutions. Whether working with low-viscosity solutions or highly filled solutions, the adjustable speed and customizable blade design of double planetary mixers can accommodate different requirements.
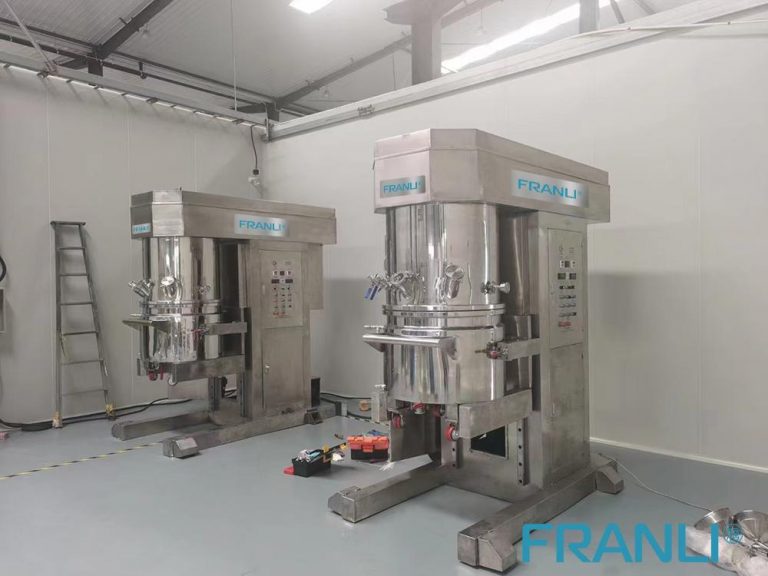
Considerations for Using Double Planetary Mixers in Polymer Solution Production
While double planetary mixers offer numerous advantages, several considerations are necessary for successful polymer solution production:
1. Material Compatibility: It is crucial to ensure that the materials used in the mixer, including blades, vessel, and seals, are compatible with the polymer and solvent being mixed. Certain aggressive chemicals or solvents may require specialized materials to withstand chemical attack and ensure durability.
2. Shear Sensitivity: Some polymers are sensitive to shear forces, which can degrade their properties. It is important to adjust the mixer’s operating parameters, such as the rotational speed and blade design, to minimize shear stress and maintain the polymer’s integrity.
3. Solvent Selection: The choice of solvent is crucial for polymer solution production. A compatible solvent must be selected to achieve proper dissolution of the polymer and to maintain stability throughout the mixing process.
4. Process Control: Monitoring and controlling the mixing process is important to ensure consistent quality and performance of the polymer solution. Parameters such as temperature, mixing time, and rotational speed need to be carefully monitored and adjusted as required.
Application of Double Planetary Mixers in Polymer Solution Production
1. Coatings Industry: Double planetary mixers have found widespread use in the production of coating solutions. High-speed blades combined with precise temperature control allow for efficient mixing of pigments, additives, and polymers, resulting in high-quality coatings with excellent color dispersion and uniformity.
2. Adhesives and Sealants: Double planetary mixers have proven to be effective in the production of adhesive and sealant solutions. The intense mixing action ensures complete dispersion and uniformity of the polymer, resulting in strong adhesion properties and consistent performance.
3. 3D Printing: In the rapidly growing field of 3D printing, polymer solutions play a vital role as printable materials. Double planetary mixers are used to prepare homogeneous formulations for 3D printing, enabling precise control over viscosity, flow properties, and cure characteristics of the polymer solution.
Double planetary mixers have become indispensable in the production of polymer solutions. Their efficient mixing capabilities, enhanced heat transfer, scalability, and versatility make them an ideal choice for a wide range of industries. With proper considerations such as material compatibility, shear sensitivity, solvent selection, and process control, manufacturers can leverage the advantages of double planetary mixers to produce high-quality and consistent polymer solutions for various applications.
As a professional double planetary mixer manufacturer, FRANLI provides a complete set of mature equipment for related machines and production lines for more than 60 countries and thousands of industries in the world, and in Russia, Turkey, Spain, Brazil, Malaysia, Indonesia, and other regions, for Many enterprises have established related production lines.
Welcome to send inquiry to us and let’s make a win win business together !
Guidelines For Double Planetary Mixer
FRANLI is a professional double planetary mixer manufacturer. Our double planetary mixer is especially suitable for dissolving, mixing, kneading, and reacting from powder to high-viscosity and high-density materials. According to different viscosities and material characteristics, Choose the right stirring paddle, and provide supporting equipment and production lines for double planetary mixers.

Advantages and Applications Of Dual Planetary Mixer
A dual planetary mixer is a versatile and efficient machine that is used in various industries, including food, pharmaceuticals, and cosmetics.

How to buy a double planet mixer?
This double planetary mixer can mix all types of viscosity of the material in no time. This double planetary mixer contains high-capacity blades that can work from 1 million centipoises to 8 million centipoises.

Double Planetary Mixer For Sale
FRANLI double planetary mixer is a high-efficiency, multi-purpose, and no-dead angle mandatory mixing and dispersing equipment.

Electronic Slurry & Double Planetary Mixer
Double planetary mixers are widely used, especially in the field of electronic slurry, whether it is stirring or mixing, the final output effect has been recognized by all walks of life.
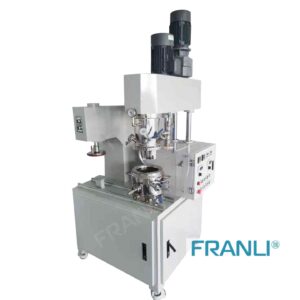
Double Planetary Mixer: Laboratory & Production
There are two types of double planetary mixers produced by FRANLI, which mainly involve two major application fields, one is laboratory research type, and the other is a factory production line

Structural Adhesive Production Equipment & Double Planetary Mixer
The double planetary mixer is one of the ideal types of equipment for low-viscosity materials. This facility has a low and fast mixing dispersing disc, which can complete the functions of high shear and dispersing low viscosity materials at the same time.