Home » Water Ink Make equipment & production line
Water Ink Make equipment & production line
Ink production line
It mainly involves three roll mills, sand mills, high-speed dispersers, filling machines, planetary mixers, and other machinery, and with the automatic batching system, it can realize fully automated production.
Features of FRANLI water ink complete set of equipment
1. It has a high degree of automation, strong production capacity, and greatly reduces labor input. It is an efficient, environmentally friendly, and safety equipment;
2. The manufacturing process of the intelligent batching system will be designed according to the user’s formula, which has a completely stable effect, and to a certain extent, guarantees product quality and production efficiency;
3. The production process of water ink needs to be sealed to a certain extent, so there is no dust flying in the production workshop, and the environment is purified;
4. The water ink production line produced by FRANLI is a series of grinding combinations, which can fully grind the product fineness, and the required fineness is fully suitable for the needs of users;
5. The tool that general users must use when coloring water-ink is a multi-axis high-speed disperser. This kind of disperser can improve the efficiency of the coloring process, the product quality is stable, scraping and stirring, and the equipment is easy to clean ;
6. The filling machine in the production line has the advantages of simple operation and high accuracy of metering and filling;
7. This set of water ink production lines can not only meet the production of water ink, but also meet the requirements of various ink production processes, fully realize automatic production, reduce labor intensity, and avoid problems such as unstable product quality caused by human factors;
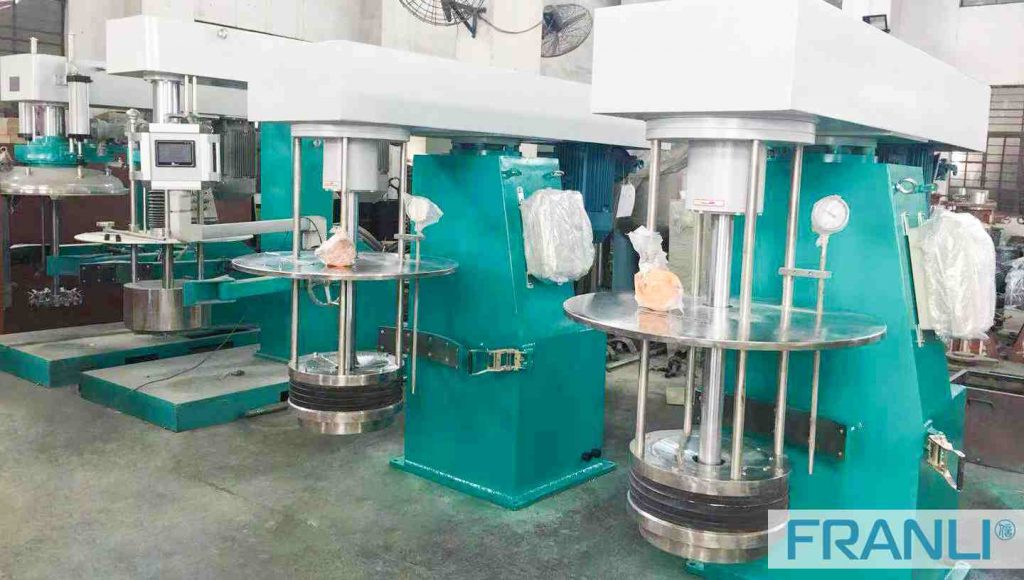
The main parameters of the production line
1. The whole set of production equipment can achieve an annual output of 500-100,000 tons,
2. The establishment of the production line can improve the design of different configurations according to the process and output.
3. The production line realizes storage, feeding, dispersing, grinding, cooling, painting, filtering, filling, and other fully automatic production;
4. The system of the production line is intelligently controlled by PLC throughout the whole process. Users or operators can perform online monitoring, pipeline valves, pumps, etc., all of which can be controlled by PLC to reduce manual errors or mistakes in production and manufacturing, and facilitate the production management. ;
5. When a general factory is carrying out small-scale production, the user can choose the appropriate suction method according to the production process, or choose vacuum suction, which can be completed through the integration of dispersion and grinding of the blue mill;
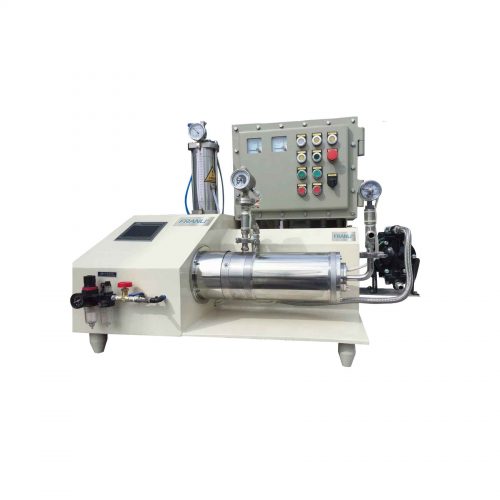
Production line control system
1. The industrial computer and PLC used in this production line are selected from international famous brand products as the upper computer of the system, and can fully guarantee the reliability of the control system.
2. The metering system adopts weighing metering or flow metering. These two methods are mainly because of high precision, good stability, fast response, and long service life; Perform precise measurements and display them on the host computer to avoid errors caused by human factors in feeding and paint mixing operations, and improve product quality.
3. Programmable logic controller (PLC) and analog input modules are all selected from international famous brand products, which have the characteristics of strong anti-interference ability and extremely high stability.
4. On-site operation is equipped with a control box (explosion-proof and non-explosion-proof), MCC cabinet, and PLC cabinet.
Ink is made by mixing resins, emulsions, solvents, pigments and fillers, additives, etc. Among them, the most critical role is the resin emulsion, which is also the foundation of the chemical characteristics of the ink!
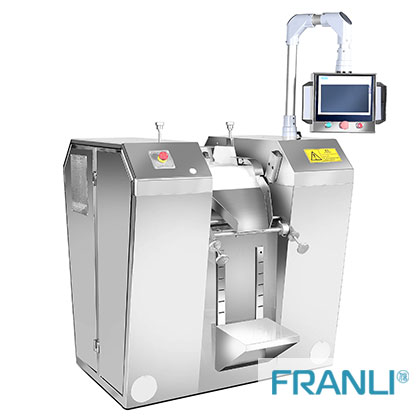
FRANLI water ink automatic production line
1. The batching unit of the production line
The batching unit is mainly carried out in four aspects, including resin, solvent, powder, and additives.
(1) The storage of resin is measured by liquid level gauge, and the addition is measured by weighing or flow meter;
(2) The storage of solvent is measured by liquid level gauge, and the addition is measured by weighing or flow meter;
(3) The storage level gauge of the powder is measured, conveyed by pneumatic force, screw, or pipe chain, and weighed and measured by the metering bin to determine the proportion;
(4) Small-scale raw materials such as additives are completed manually or by small-scale delivery units;
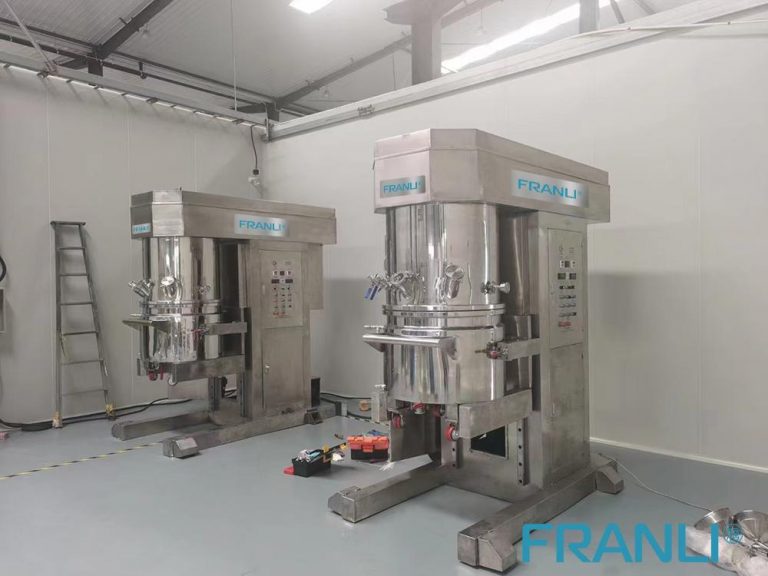
2. The production unit of the production line
(1) Intelligent batching system: Before the production of water ink, the user needs to set the production formula on the industrial computer or touch screen; then control the pump valve through the PLC to add the emulsion, solvent, and powder to the high-speed dispersion according to the formula. Kettle, and then through the PLC to control the frequency converter, the motor drives the disperser to start working at the set working speed, and finally disperses quickly to complete the pulping;
(2) Grinding system: After the pulping is completed, the PLC instructs the valve at the bottom of the pulping tank to open, and the material is pumped or flowed to the sand mill station by itself, and the pipeline level gauge reminds the PLC to turn on the feeding pump of the sand mill to start sanding. Machine feeding, sand mills in series (with self-protection devices) all start working one by one, with a transfer cylinder in the middle; complete grinding;
(3) Toning system: the grinding output is pumped to the toning kettle, and the toning is carried out according to the production plan;
(4) Filling system: After the color matching is completed, the finished ink is transported by the filter car to the finished product storage tank for storage, or transported to the filling machine station for filling;
Note: When toning, prepare the color paste (or color essence) that should be used, add 80% of the prescribed amount, and then slowly adjust the color tone until the color tone is satisfactory.
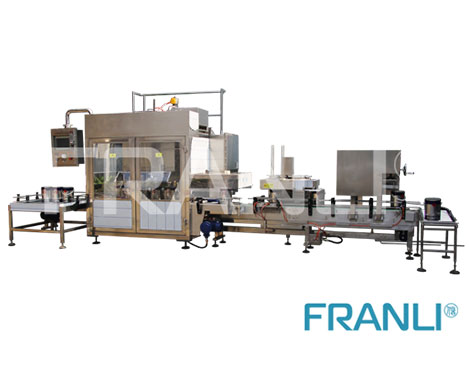
Inspection indicators: viscosity, fineness, gloss, color tone, hiding power, adhesion. Long-term indicators include whether there will be skinning and precipitation. Whether it will change color, and whether the salability of the primer after construction is qualified.
FRANLI is a water ink production line manufacturer, and we design the production ink production line, ink production complete sets of equipment, including a high-speed disperser, temperature-controlled stainless steel reactor, bead mill, filter, filling machine, three-roll mills, supporting workbenches, integrated control systems and other complete sets of equipment have been exported to Russia, Turkey, Egypt, Brazil, Malaysia, Indonesia, Spain, etc.
Welcome to send inquiry to us and let’s make a win win business together !
Guidelines For production line
FRANLI has several sets of wet grinding production lines, including PCB ink production line, ink production line, pesticide production line, automobile coating production line, etc.
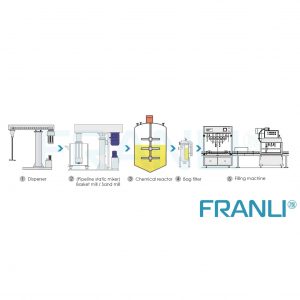
Pesticide Production Line
The production of pesticides mainly uses sand mills, emulsifiers, chemical reaction kettles, twin-shaft mixers, filling machines, and other equipment. This equipment thus constitutes a complete set of pesticide production lines, from the grinding and storage of particles to the reaction and Blending, and finally filling and packaging, the FRANLI pesticide production line is fully intelligent, with the characteristics of simple operation, safety, and stability.
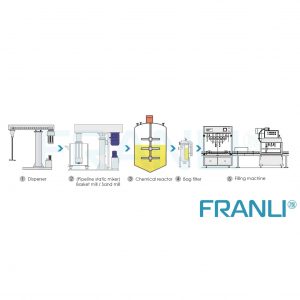
Gravure Ink Production Line: manufacturing process
The gravure ink production line is a professional manufacturing process that requires attention to detail and a commitment to quality.
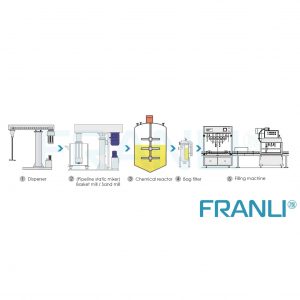
Printing ink production line
FRANLI Printing ink production line mainly takes intelligence, environmental protection, and high production efficiency as the main production standards.
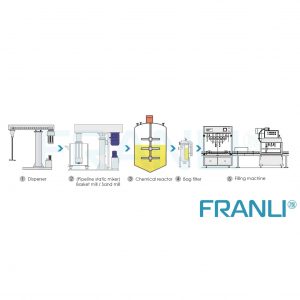
Water Ink Make equipment & production line
FRANLI water ink complete set of equipment and production line is mainly composed of an intelligent batching system, high-speed dispersion pulping system, metering system, horizontal grinding series system, multi-functional mixing and coloring system, cleaning system, automatic control system, automatic filling system, and other parts. Advanced production technology.
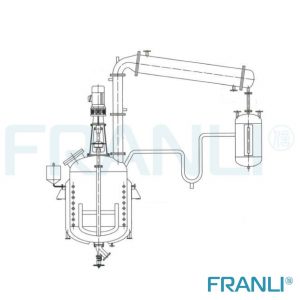
Resin Production Line & Complete Manufacturing Equipment
FRANLI provides complete sets of resin manufacturing equipment and production lines, which are mainly suitable for the synthesis of various chemical resins, such as unsaturated polyester resin, phenolic resin, epoxy resin, alkyd resin, ABS resin, etc. It can also be used for the manufacturing and production of Various types of emulsion resins, such as acrylic resin emulsion, etc.
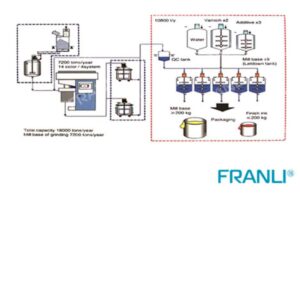
Ink production line
The main equipment of the ink production line includes material storage tanks, barrels, multi-model dispersing machines, chemical reactors, sand mills, three-roll mills, material operating platforms, filling machines, electronic process control systems, process pipelines, air compressors, A set of equipment such as cleaning equipment.