The Versatile Application of Horizontal Sand Mills
Horizontal sand mill
A horizontal sand mill also referred to as a horizontal bead mill or horizontal media mill, employs a unique grinding chamber filled with small grinding beads made of glass, ceramic, or steel. The motor-driven rotor rapidly agitates these beads, causing particle size reduction and dispersion of the material being processed. The horizontal arrangement of the chamber ensures improved flow and uniform distribution of the grinding media, resulting in efficient grinding and improved product quality.
Application: Paint, Adhesive, Battery, Pharmaceutical industry, Cosmetic
In the realm of particle size reduction and dispersion, horizontal sand mills have emerged as indispensable tools in numerous industries. With their ability to efficiently grind, disperse, and homogenize a wide range of materials, these advanced machines have revolutionized the manufacturing processes of paints, inks, dyes, coatings, and cosmetics, among other applications.
Applications in Paint Manufacturing
One of the primary applications of horizontal sand mills lies in the paint manufacturing industry. These mills enable the efficient dispersion of pigments, fillers, and binders into the paint formulation. By achieving highly consistent particle size distribution, horizontal sand mills facilitate the production of paints with enhanced color intensity, improved glossiness, and excellent stability. Moreover, these mills can handle both solvent-based and water-based paint formulations, making them incredibly versatile for a wide range of paint applications.
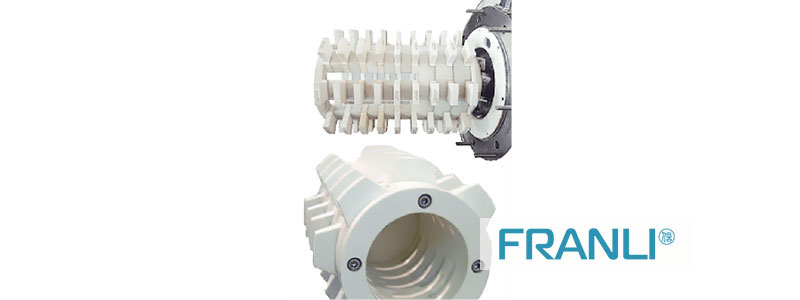
Use in Ink and Coating Productions
The ink and coating industries heavily rely on horizontal sand mills for the production of high-quality ink formulations. Whether it is flexographic, gravure, or screen printing inks, these mills enable the dispersion of colorants, resins, and additives, resulting in inks with excellent color saturation, printability, and adhesion properties. Additionally, horizontal sand mills contribute to the production of coatings by uniformly dispersing pigments and other functional additives, ensuring superior coverage, durability, and resistance to abrasion.
Role in the Cosmetics Industry
Horizontal sand mills play a crucial role in the cosmetics industry, where the uniform dispersion of pigments, oils, and waxes is essential for the production of various cosmetic products. From lipsticks and eyeliner to foundations and mascaras, these mills enable the formulation of cosmetics with consistent texture, color, and stability. By achieving optimal particle size reduction, horizontal sand mills ensure smooth application, long-lasting wear, and attractive aesthetics.
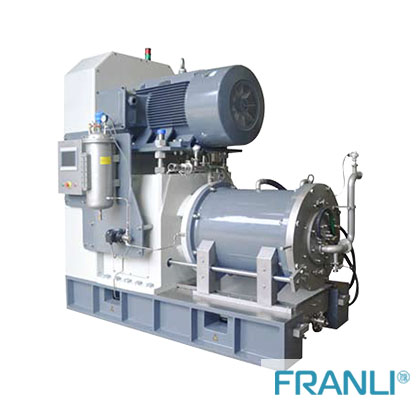
Advantages and Benefits
Horizontal sand mills offer several advantages that make them highly sought after in various industries. Firstly, their efficient grinding and dispersion capabilities dramatically reduce processing time, resulting in increased productivity and cost-effectiveness. Secondly, the ability to achieve precise particle size control allows manufacturers to tailor their products to specific requirements, ensuring consistent quality with each batch produced. Furthermore, the ease of operation, low maintenance requirements, and the ability to handle a wide range of materials make horizontal sand mills ideal for both small-scale and large-scale production facilities.
The horizontal sand mills have become integral to numerous industries as they contribute to efficient particle size reduction, dispersion, and homogenization of various materials. Their widespread applications in paint manufacturing, ink and coating productions, and the cosmetics industry highlight their versatility, enabling the production of high-quality and consistent products. With their multiple benefits, including enhanced productivity, product quality, and customization options, horizontal sand mills continue to revolutionize grinding processes, shaping the future of various manufacturing sectors.
Welcome to send inquiry to us and let’s make a win win business together !
Guidelines For Sand Mill
The sand mill mainly uses friction, shearing, and collision as effective grinding methods. It is one of the grinding equipment currently applicable to a wide range of material particle sizes and has high grinding efficiency. The energy density per unit volume is large. The control system can complete the continuous grinding and continuous discharging of the slurry, which greatly improves the production efficiency of the sand mill. It has the advantages of high energy density, fine product granularity, small environmental pollution, simple equipment structure, and convenient maintenance.
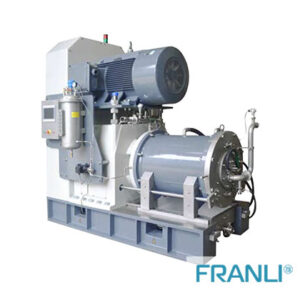
Sand Mill: Enhancing the Efficiency of Grinding & Dispersion
Sand mills, also known as bead mills or media mills, are mechanical devices used in the field of grinding and dispersion.
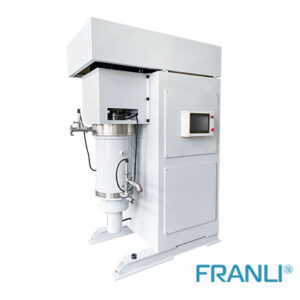
Instructions for use of vertical sand mill
The vertical sand mill is a nano-sand mill whose grinding cylinder adopts a suspended structure, raw materials enter from the bottom and discharge from the top.
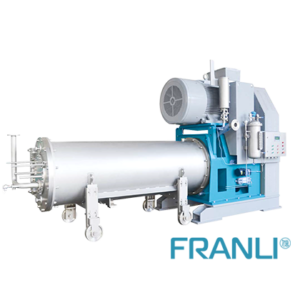
How to choose the right vertical sand mill & horizontal sand mill?
Vertical sand mills and horizontal sand mills are commonly used equipment for grinding in paint, coating, ink, and other industries. They all rely on the high-speed rotation between the grinding medium and the material for grinding work.
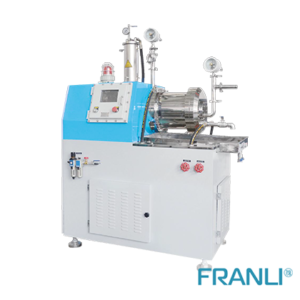
How to deal with the problem of sand mill?
The sand grinding machine, also known as the pearl grinding machine, is used to grind the paint of the pigment with hard wear -resistant beads, glass balls, etc. in a closed cavity.
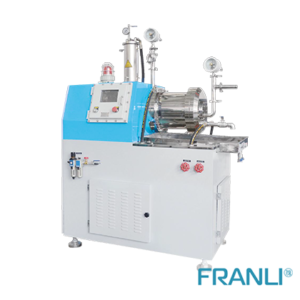
How to choose a sand mill for paint?
Sand mills are mainly used in industrial fields such as paint coatings, cosmetics, food, daily chemicals, dyes, inks, pharmaceuticals, magnetic recording materials, ferrites, photosensitive films, oxide ceramics, and new energy.
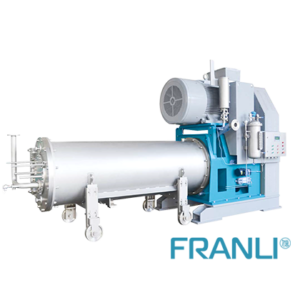
Grinding media for sand mills
Sand mill is a kind of high-efficiency grinding equipment, which is mainly used for grinding materials, and the particle size of the final grinding can reach the nanometer level.