Home » The Role of Ribbon Mixers in Powder Mixing
The Role of Ribbon Mixers in Powder Mixing
Ribbon mixer
Ribbon mixers, as the name suggests, derive their title from the ribbon-like appearance of the mixing elements attached to a central shaft that rotates within a cylindrical vessel (mixing chamber). The mixing elements, either a continuous helical ribbon or double-helix ribbon blades, facilitate the flow of powders in a spiraling motion along the length of the mixing chamber and up and down within the vessel. This dynamic promotes thorough blending of the powdery components and ensures a homogeneous end product.
Advantages of Ribbon Mixer
- fast and efficient
- safe and stable
Application: chemical, pesticide, dye, medicine, feed, fertilizer, metallurgy, mining, food, plastic, additives, and other industries.
Powder mixing is an essential process in various industries, such as food processing, pharmaceuticals, cosmetics, and chemicals. Efficient mixing of distinct powdery substances is of paramount importance, as homogeneous distribution and blending of components lead to consistent end product quality. Ribbon mixers are a popular choice in several industries due to their versatility, adaptability, and overall effectiveness in powder mixing.
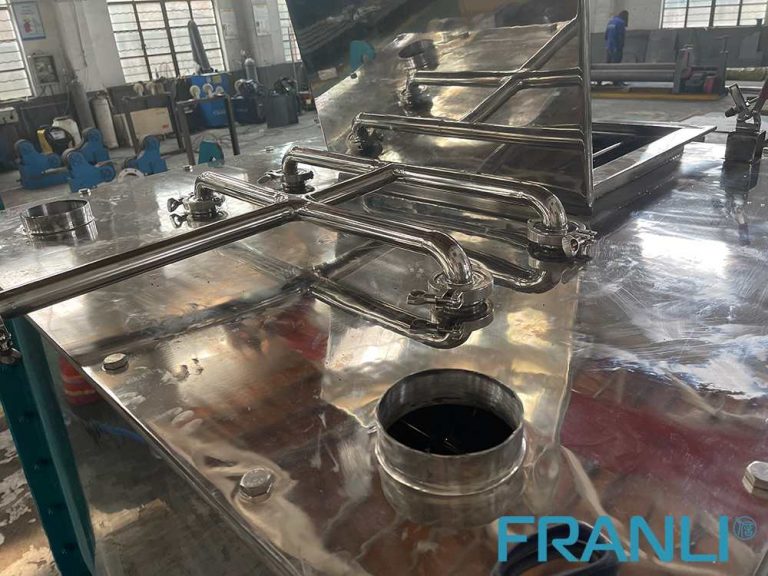
Operating Mechanism
The typical operation of a ribbon mixer involves the movement of powders at the mixing chamber’s axis and periphery simultaneously. The outer ribbon blades move the material toward the chamber’s center, while the inner ribbon blades move the material outward. A continuous convective flow results from this process, ensuring uniform blending of all powder components.
In addition to the ribbon blades’ design, the mixing speed and time play a vital role in the mixing efficiency. The rotation speed is typically 25-50 rpm (revolutions per minute) in a ribbon mixer. However, it is important to note that overly high mixing speeds can result in air entrapment and risk demixing. Since the process is not entirely gentle, the use of ribbon mixers for delicate, heat-sensitive, or breakable material needs to be evaluated on a case-to-case basis.
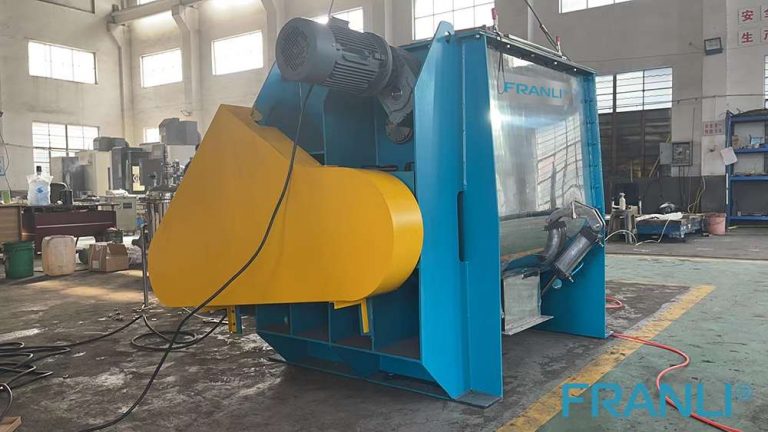
Types of Ribbon Mixers
Ribbon mixers are available as batch mixers or continuous mixers.
1. Batch mixers: Batch ribbon mixers are the most common type used in various industries. In this style, the mixer preloads a predetermined powder quantity into the mixing chamber to achieve the desired product mixture. Once the mixing cycle is complete, the contents are discharged from the mixer. These mixers are effective for small to medium-scale production and provide excellent quality control.
2. Continuous mixers: In continuous ribbon mixers, material runs continuously into the mixer at one end while discharging simultaneously at the other end. This method is suitable for high-volume, large-scale production processes where efficiency and consistent quality are essential. However, it is important to accurately control the feed rate to produce a uniform mixture.
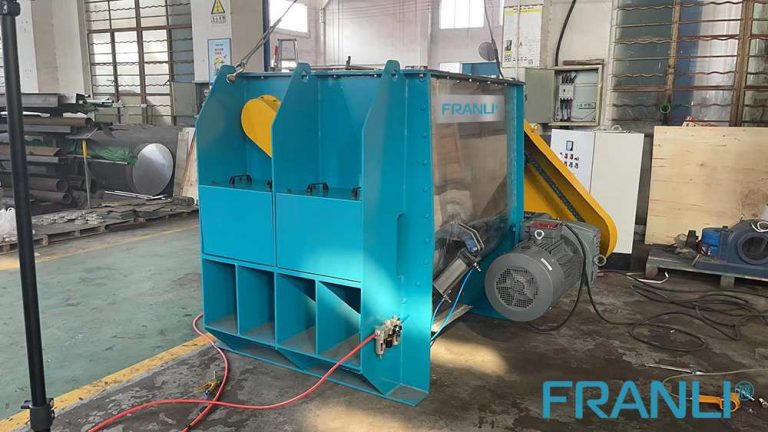
Advantages of Ribbon Mixers
1. Versatility: Ribbon mixers can mix a variety of dry materials, including powders, granules, and aggregates, and can incorporate liquid ingredients into the mix as well. Their adaptable design allows for customization to suit the requirements of individual applications.
2. High Mixing Efficiency: Owing to their operating mechanism, ribbon mixers provide excellent mixing efficiencies in a relatively short time, ensuring uniform blending of even dissimilar components. When properly operated, they can achieve, on average, within 95-98% homogeneity in just 15-20 minutes.
3. Easy Cleaning and Maintenance: The simplicity in the design and construction of ribbon mixers makes them comparatively easier to clean and maintain. Their large discharge valve allows for quick emptying of the mixing chamber, providing better accessibility for inspection and cleaning.
4. Low Energy Consumption: The convective mixing motion employed by ribbon mixers requires relatively low energy compared to other mixing devices. This factor reduces the overall operating costs and increases operational efficiency.
5. Scalability: The design of ribbon mixers allows for easy scalability of production processes, accommodating varying batch sizes or powder volumes as necessary.
Ribbon mixers provide multiple benefits across numerous industries, making them a popular choice for powder mixing. Some of the notable advantages include:
Factors to Consider When Choosing Ribbon Mixers
Selecting the appropriate ribbon mixer for any specific application is essential to enhance efficiency and achieve the desired results. Several factors should be considered when making the selection:
1. Material Properties: Properties like particle size, bulk density, and flowability affect the mixing performance and should be considered while choosing the mixer. Ribbon mixers are most effective for powders with similar particle sizes.
2. Mixer Design: The design of the ribbon mixer has a significant impact on the mixing efficiency. Factors such as the blade’s shape and pitch, mixer volume, and length-to-diameter ratio should be evaluated according to the intended application.
3. Consistency and Homogeneity: The desired level of consistency and homogeneity of the final product must be considered when selecting a mixer. Ribbon mixers offer a high degree of homogeneity, making them suitable for applications that demand uniform blending.
4. Cleaning and Maintenance: The structural design and ease of cleaning should be evaluated to minimize downtime during cleaning and maintenance.
Ribbon mixers have proven to be a versatile and efficient means of powder mixing in various industries. Their unique operating mechanism, comparatively low energy usage, and ease of maintenance make them an ideal choice for diverse applications. Understanding the principles of ribbon mixers and considering the factors mentioned can ensure the selection and implementation of a mixer that will deliver consistent, high-quality results tailored to both the industry and specific operations.
Welcome to send inquiry to us and let’s make a win win business together !
Guidelines For Ribbon blender
Ribbon blenders are essential equipment in various industries where the quality and consistency of the final product are critical factors. They are highly efficient, customizable, and reliable mixing solutions that offer unsurpassed performance and versatility. By integrating a ribbon blender into your production line, you can ensure consistent and reliable product quality, increased productivity, and reduced manufacturing costs.
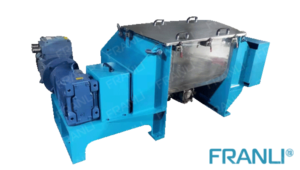
Ribbon Blender Mixer Equipment
A ribbon blender mixer, also known as a ribbon mixer or horizontal ribbon blender, is a powerful industrial machine designed for thorough and efficient blending of various materials.
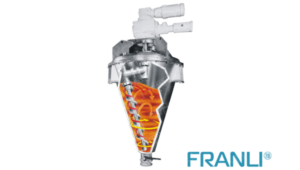
Ribbon Blender Mixer: The Right Choice for a High-Quality Blender
Ribbon blender mixers, also known as ribbon mixers or ribbon blenders, are horizontal mixing devices characterized by their unique ribbon-shaped agitators.
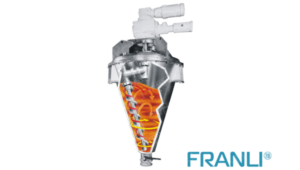
Vertical Ribbon Blender: Efficient mixing equipment for solids and powders
A vertical ribbon blender, also known as a vertical mixer, is a type of mixing machine widely used in various industries for the homogeneous blending of dry, free-flowing solids.
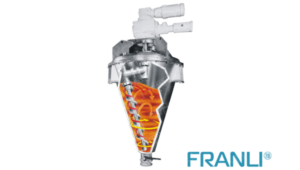
Powder Ribbon Mixer: Whirling Agitator and Horizontal U-shaped Housing
A powder ribbon mixer, also known as a ribbon blender, is a versatile and widely used machine for combining different powders, powder with liquid, powder with granules, and dry solids.
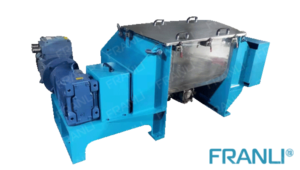
Small Ribbon Blender: A Versatile and Efficient Processing Equipment
The small ribbon blender is a versatile and efficient processing equipment used in the food, pharmaceutical, and cosmetic industries for blending, mixing, and uniformizing various types of materials.
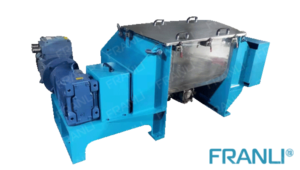
What is A Small Ribbon Blender?
The small ribbon blender is a versatile and efficient machine used for the mixing of various materials such as powders, pastes, and dried granules.